Bearing manufacturers have long been aware of the relationship of heat to bearing life and have designed formulas to accurately calculate safe operating temperatures. The results show a temperature band in which both bearings and lubricants will operate at peak performance with the least stress.
Once outside the ideal temperature range, they will degrade at an accelerated rate. So how do you interpret temperature readings, and how should they affect your maintenance procedures? This article describes some temperature-oriented methods for determining bearing health and life expectancy, both in the plant and in the field.
Figure 1. Heat Ranges of Bearings1
Figure 1 shows the thermal range of a typical rolling element bearing. Note that bearing metal temperature is often higher (10 to 25 degrees Celsius) than the oil temperature in the bearing within an oil circulation system. The green zone represents the sweet spot for bearing and lubrication temperature; operating in the yellow zone reduces lubricant and bearing life; and if your bearings are in the red zone, expect both the bearing and the lubricant to be destroyed rapidly.
There are different temperature bands for different combinations of bearing and lubricant, but they will have the same general trend regarding the best operating temperature and its effect on accelerated wear and failure. In most standard lubricants, for every 15°C1 increase in temperature above 70°C, the lubricant life is more than halved and there is a negative effect on bearing life. Any mineral oil operating at a temperature above 80°C or 90°C will have a greatly diminished life. In no case should bearing temperature ever exceed the maximum rating of either the bearing or the lubricant.
Monitoring Bearing Condition
Machine bearings are generally monitored through vibration analysis, oil analysis and/or ultrasound techniques. Through these, it is possible to compare current data to historical data and accurately assess the life of the bearings. Temperature increase due to increased friction is not even considered as a symptom of bearing failure in many bearing analysis texts2 until Stage 3 bearing failure occurs.
If temperature is a reliable method of bearing life prediction, why is it ignored until after it's too late? The monitoring of temperatures with thermography has been considered unreliable because so many variables such as ambient temperature, speed, load and runtime all have a pronounced influence on bearing temperature.
This article compares identical or near-identical bearings on the same shaft which cancels the effects of these variables because they are common to both bearings. The remaining temperature differences between the two bearings on a common shaft with the same load, can only be the result of friction, an indicator of bearing problems.
Perhaps subtle changes are hidden because there are so many variables that can potentially contribute to bearing temperature. In addition to friction, other factors that can contribute to temperature variation are load, speed, ambient environment temperature and runtime duration. If these conditions could be predicted and accounted for accurately, then increases in temperature would reliably indicate bearing problems.
In most cases vibration analysis and oil analysis are still the best ways to determine bearing health. Unfortunately, it's not always possible or affordable to use these methods in hostile production environments. Any environments where staff or technicians cannot easily access the machine without taking it offline, or cannot access the machine due to hazardous conditions or inconvenient locations make vibration or oil analysis expensive at best, or even impossible.
There are many industries and production environments where bearing failure represents catastrophic loss, yet vibration analysis is not practical. Photographic film and paper manufacturing, chemical processing and metalworking plants are a few examples of industries that depend greatly on bearings, but where bearing accessibility can be a major problem. Most manufacturers have at least some vital equipment in areas that are not easily accessible.
Infrared Sensors
Outside of manufacturing, other industries are similarly affected. Wheel bearings on railroad cars are a specific case in point: they are underneath trains, which are not hospitable places for performing these tests while the cars are moving. Secondly, there is no practical method of checking all such wheel bearings in a timely manner because of the sheer number of them in use.
Currently in the railroad industry, the only practical method for detecting impending bearing failure is to use so-called hotbox detectors. These are infrared sensors located along the train tracks that detect high temperatures in wheel bearings as the train passes. These are extremely limited and can detect bearings only in Stage 4 failure where catastrophic failure (a wheel burn-off) is imminent. An alarm requires immediate emergency action, disrupts train schedules, and is extremely costly.
When these detectors miss bad bearings or the alarm is not tended to immediately, the resulting wheel burn-off may lead to a train derailment, widespread hazardous chemical spill, loss or severe damage of client merchandise, or loss of human life. Because the consequences are so dire, every false positive results in delays and inspections that can negatively affect the entire industry.
Studying Temperatures
If bearing temperature changes due to maintenance-related problems could be isolated from all the other factors that contribute to bearing heat, a properly designed monitoring device could detect bearing failure at the Stage 2 level.
A newly patented technique is being evaluated that could have significant benefit to industries that need to analyze bearing and lubrication life in difficult-to-reach areas, such as under train cars. The heart of the patent is a technique that cancels all thermal variables except the increase in bearing temperature due to wear or lubrication failure.
The procedure takes heat data from each bearing on a common shaft and compares the data. Because the load, speed, ambient temperature, and run duration are common to all the bearings common to the shaft, their effects on temperature are canceled.
Any recorded temperature variation is the result of unwanted maintenance- or repair-related conditions such as over- or underlubrication, bearing damage, misalignment, or loose-foot condition. If one bearing is more than 15°C greater than another on the same shaft, the bearing health is in question and the root cause of the increased bearing temperature must be determined. The bearing comparison is accomplished with electronic temperature sensors and comparators powered by a self-contained power supply that recharges its battery through the motion of the equipment.
The methodology involves the following:
-
Temperature sensors are attached in close proximity to all the bearings on a common shaft or axle.
-
The sensors apply input to a sensing unit that is self-contained and has wireless technology for communication with warning devices.
-
The temperature data of each unit is analyzed and compared electronically.
-
If any bearing temperature varies more that 15°C, an alarm is transmitted and an LED indicator will light.
-
The system is self-powered by a small power supply which is actuated by the movement of the equipment.
-
There is a maximum allowable temperature in case all bearings are out of normal operating range.
This technique will never be as accurate as oil or vibration analysis, but in remote or hazardous locations where these tools are not an option, it will provide an increased level of condition monitoring that was not available in the past.
References
1. SKF bearing manual.
2. Entek IRD Volume I Vibration Analysis, p. 6-48.
Four Stages of Bearing Failure
Stage 1. Earliest detectable indication of bearing failure using vibration analysis. Signals appear in the ultrasonic frequency bands around 250 KHz to 350 KHz. At this point, there is approximately 10 to 20 percent remaining bearing life.
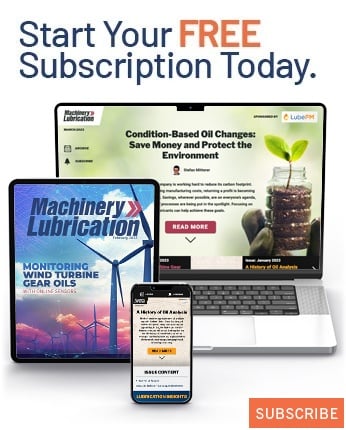