There exists a critical need in the mobile and fixed asset market to empower field units to determine oil quality on demand and provide complementary oil condition information that has been traditionally obtained from oil analysis labs. The current methodology of testing in off-site labs is nonoptimal and costly due to the logistical challenges of shipping samples and the time delay in getting information back to personnel to be able to make quick and informed decisions. Determining oil quality in real-time with embedded and portable oil assessment devices operated by mechanic personnel provides the operational flexibility and rapid means of screening oil quality that is key to establishing a program to provide real-time condition-based monitoring products for the care of all assets.
Measuring the viscosity of oil is a rapid method of determining oil condition, and is considered an important parameter in assessing asset readiness. The viscosity sensor which can complement infrared (IR) spectroscopy and other bulk property sensors provides instantaneous on-line viscosity and temperature data, has no moving parts and a wide operating range, and offers universal plug-n-play connectivity for integration with and into other handheld products. The sensors have been tested in actual commercial-specified oils in order for a correlation function to be established between the ASTM methods acquired dataset and the sensor generated viscosity values; these correlation functions can be stored on any handheld for automatic conversion. The viscosity sensor is currently installed in commercial markets such as machine tool oil monitoring and coating applications in rigorous environments where return on investment (ROI) benefits have been realized and are evaluated for mobile and fixed assets where oil condition monitoring is of paramount importance.
Acoustic wave (AW) sensors offer a number of advantages over conventional mechanical and electromechanical viscometers because they are small, solid-state devices that can be immersed in the oil providing an instantaneous viscosity data stream for embedded OEM or end-user spot-check applications. Because the sensors are unaffected by shock, vibration or flow conditions, they can be used in harsh operating conditions to measure viscosity from zero to 500 cP with a temperature range of -25°C to 125°C with a high degree of accuracy. At the same time, sensor measurements are not affected by particulates in the oil.
Conventional mechanical and electromechanical viscometers designed primarily for laboratory measurements are difficult to integrate into the control-monitoring environment. As a consequence, many companies rely on decisions based on intermittent "snapshot" data acquired from periodic sampling where conventional instrumentation can be affected by temperature, shear rate and other variables.
Figure 3. Cross-section of the sensor showing transducers on the lower surface and liquid molecules (gold balls) on the upper surface.
Given that contaminants in oil (water, solvents and fuel) are known to degrade viscosity and cause damage to internal components of diesel assets, whether they are trucks or construction equipment or military vehicles, it important to not rely on snapshot data alone. High water contamination levels in diesel fuel have been shown to cause corrosion and pitting, leading to increased metal wear particle counts. The presence of residual cleaning solvents and fuel contamination has caused seals to swell and create less-than-ideal engine operating situations. Knowledge of viscosity in real time provides a significant benefit to measure aging of oil, ingress of contaminants during commercial operations and prevents incipient mechanical failure due to loss of oil lubrication properties.
This article shows a next-generation sensor packaged as a treaded bolt (Figure 2), targeted at embedded integration to fixed and mobile diesel assets. Also presented is data from a customer who has tested the next-generation sensor on 600 samples of new and used oil ranging from hydraulic to turbine to gear to diesel engine oils. The data has been correlated to lab measurements by this and other customers, thereby resulting in viscosity data which bridges the traditional dataset to the new methods of measurement.
Viscosity Monitoring Technology
Vectron, a designer and manufacturer of acoustic wave (AW)-based sensor products, has developed a viscosity sensor with a wide dynamic range (air to several thousand cP) in a single sensor (Figure 1).
The Vectron ViSmart™ is a commercially available, robust, reliable and cost-effective surface acoustic wave solid-state viscometer for integration into in-line, real-time monitoring and process control systems for scalable applications (Figure 2).
The sensor has no moving parts (other than the atomic scale vibration of the surface) and, due to the high frequency of the vibration, several millions of vibrations per second, is independent of flow conditions of the liquid and immune to vibration effects of the environment. High temperature electronics allow a wide operating temperature range for the sensor.
The importance of these acoustic sensors lies in the distinctly different measurement principle. Whereas one class of mechanical devices measures kinematic (flow) viscosity and the other class measures intrinsic (friction) viscosity, the acoustic wave (AW) sensors measure acoustic impedance, (???)½, where ? is the radian frequency (2pF), ? is the density and ? is the intrinsic viscosity.
The viscosity measurement is made by placing the quartz crystal wave resonator in contact with liquid. The liquid's viscosity determines the thickness of the fluid hydrodynamically coupled to the surface of the sensor. The sensor surface is in uniform motion at frequency, ? =2pF, with amplitude, U. The frequency is known by design and amplitude is determined by the power level of the electrical signal applied to the sensor. As the shear wave penetrates into the adjacent fluid to a depth, d, determined by the frequency, viscosity and density of the liquid as d=(2?/??)½, shown in Figure 3.
Acoustic viscosity is calculated using power loss from the quartz resonator into the fluid. The unit of measure is acoustic viscosity (AV) and is equal to rh, (g/cm3 cP) (density times dynamic viscosity).
The acoustic wave resonator supports a standing wave through its thickness. The wave pattern interacts with electrodes on the lower surface (hermetically sealed from the liquid) and interacts with the fluid on the upper surface. The bulk of the liquid is unaffected by the acoustic signal and a thin layer (on the order of microns or micro inches) is moved by the vibrating surface. Also present is a proprietary hard-coat surface that is scratch-proof and abrasion-resistant which allows the sensor to operate in extreme environments and makes the AW sensor a suitable candidate for oil condition-based monitoring applications in mobile and fixed asset markets.
Oil Analysis Applications
Significant testing has been accomplished by the oil analysis community to ascertain the performance for the solid-state viscometer. The tested oils fall in two categories: clean and contaminated. The viscosity values for the oils are measured at ASTM-approved rheometer equipment (at 512 1/s shear rate) and with the solid-state sensor at the following temperatures of 30°C, 40°C, 60°C, 100°C. Based on this data, functions are generated to interpolate the viscosity for intermediate temperatures.
The Vectron low shear solid-state viscosity sensor measures the acoustic viscosity (AV), which is the product of dynamic viscosity and mass density. Dynamic or kinematic viscosity is more commonly used in industry. The goal by customers is to establish correlation between acoustic viscosity and dynamic viscosity.
Correlation and Performance
The viscosity data of all oil (hydraulic, gear, engine, turbine and other) samples at different temperatures are plotted and curve-fitted (Figure 4). Most data points fall in the same trend except for a few points. The correlation factor R-square is 0.9107, which means an accuracy of 91 percent. The outliers are from extremely thick (1,000 and 3,000 cP) synthetic oil that almost reaches the limit of the viscosity sensor measurement range. If these outliers are taken out, the curve becomes steeper and the correlation factor slightly improves (Figure 5).
The equation in Figure 5 can be used as a default correlation equation when oil type is unknown or when the oil type is not covered by correlation study and represents 92 percent accuracy for the Vectron solid-state viscosity sensor.
The viscosity data for mineral oils in the sample inventory are plotted and curve-fitted in Figure 6. These oils are mostly Mobil or Exxon mineral oils and are inclusive of other manufacturers.
The correlation factor R-square is close to unity for mineral oils for the Vectron solid-state viscosity sensor.
The viscosity data for synthetic oils within the sample inventory are plotted and curve-fitted in Figure 7. If one curve is used to fit all the synthetic oils, the correlation factor is 0.9249.
It is important to note that Figure 8 shows the correlation function to a single oil (Mobil SHC 639, ISO 1000 grade); observe the 99 percent accuracy for the Vectron solid-state viscosity sensor.
All the correlation equations are in the form of:
Where, X is the acoustic viscosity and Y the dynamic viscosity. A and B are parameters that depend on oil types.
If Vectron does not have information about oil type, standard equations can be used with the correlation factor is 0.9107. If Vectron determines the oil type, the correlation can be further improved (determination either with a quick test, or look up in the database).
The conclusions that can be drawn from the data above and the customer testing are:
- There is correlation between lab method and Vectron viscosity sensor for each oil (or group of oil), and that a library of fresh oil correlations is practical.
- The Vectron ViSmart™ viscosity sensors operate at repeatable shear rates relevant to the assets lubricated under normal operating conditions.
-
The ViSmart™ sensors offer acceptable correlation to lab measurements at these shear rates.
-
The correlation created from virgin oil provides the reference points from which changes in viscosity due to aging and contamination of the oil can be easily determined.
-
Deviations of the oil from a predefined interpolation function at any temperature is a significant means of screening oil quality and is more accurate than "compensating" to 40°C.
-
Evaluating deviations in acoustic viscosity is of comparable value to using kinematic viscosity. That is, independent and accurate knowledge of density is important only for correlation between on-site sensor testing and lab data.
Benefits
The commercially available viscosity sensor can be readily applied in field operations or installed directly on the equipment for continuous monitoring of viscosity, enabling the mechanic personnel to test the oil in minutes. It complements lab oil analysis testing by providing real-time viscosity data and enables streamlining of logistic costs. And because no calibration is required for the rugged vibration and shock-proof sensor, once it is installed in a harsh industrial environments, maintenance costs are extremely low.
The sensors are currently used in 24/7 applications in the commercial sector, with real-time data transfer for decision-making abilities. The real-time in-line threaded bolt sensor can be immersed in the oil or simply used for spot-checking. Providing real-time viscosity data and using the sensor continuously provides the necessary information to personnel to make critical decisions in actual field applications leading to extension of machine life and maintenance schedules while complementing the other oil quality parameter data stream obtained from the labs.
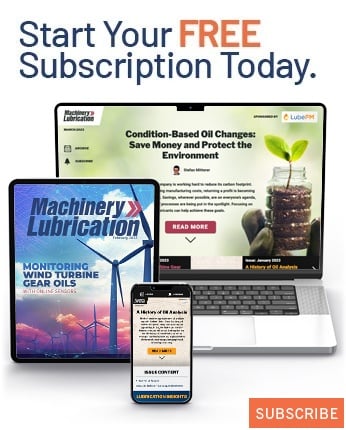