Maybe you've just started your oil analysis program. Or maybe you've been performing oil analysis for years, have an effective lubrication program in place, and everything's running like a well-oiled machine. No matter what state a lubrication program is in, every user of oil analysis will at some point receive that report that causes a panic. So how does one handle it?
I was recently asked this question, more or less in exactly the same words as the title of this column ("What to Do When Your Oil Analysis Results Go South"). After taking mild offense (I'm from the southern hemisphere) I explained that, statistically speaking, it's more likely something has gone north that's causing the alarm. And just because there's a variance in the report, it doesn't necessarily imply a problem with the machine - all it means is that some detective work is needed.
Don't Jump the Gun
The first step is to read the report thoroughly to make sure it can be understood. The more experience one has in interpreting the numbers, the more likely he or she will be able to decide whether the diagnosis has hit or missed the mark. Compare the numbers to past results because a bad diagnosis suggests something has changed from past trends. Compare the results to similar machines in similar operating environments. Don't look just at the offending numbers; try to absorb the bigger picture. If a problem has occurred, it likely has been noted in other places in the report as well. If no other trend upsets are apparent, it could simply be an analysis error. If this is believed to be the problem, or if clarification on other test results is needed, contact the lab. Most labs will be happy to entertain any concerns, and just as happy to rerun tests or suggest other confirmatory analyses that users may not know about.
The second step involves deciding the urgency of the problem. If the aberrant results have just topped the warning level, a basic inspection may be all that is required; therefore the test needs to be run again at half the normal analysis interval. If the critical limits have been shattered, it is likely that a problem has occurred.
Question, Question, Question
Once it has been determined that there is indeed a problem, it's time to go and look at the machine. Gather a group of operators, lube techs and mechanics to visit the machine - standing next to it might jog some memories that otherwise would not surface in a control room or workshop. Question the operators about any changes in operating patterns and ask the lube tech how the sample was taken. If the usual lube tech did not take the sample, that may be the answer right there. Find out if any undocumented oil changes or top-ups took place. Information may have to be obtained from personnel on other shifts, and there could be a long list of people to talk to. Find out from the mechanics if any repairs or modifications were undertaken before the last sample, even on the outside of a machine - a poorly located or connected ground wire on an arc welder has been known to cause damage. Inquire if there was any construction in the vicinity - excessive vibration or stresses introduced by poorly constructed pipe-work have also been known to cause lube upsets.
Actions Speak Louder than Words
By now there should be enough information to decide whether an environmental upset has taken place. It's time to inspect the machine. Look at the breather and sight glass. Measure the temperature and feel for any excessive vibration. Listen. Take a sample for a visual analysis - look for sediments, contamination by water, dirt or metal. If a visual analysis indicates something is amiss, then sending a sample to the lab is probably not warranted. Take immediate corrective action, like filtration, vibration or thermography before performing another lab analysis.
If an environmental or mechanical problem has been discovered, the path to resolution should be clear. A confirming sample may need to be procured, but is not necessary if the answer is apparent. If nothing is out of synch, it's time to take a confirming sample and rush it to the lab. Order the full range of tests, and ask the lab for its advice.
Once the likely cause has been determined and corrective action taken, it's time to retest again. Keep doing this at frequent intervals until the problem has been sorted out.
Trouble-shooting oil analysis problems can be both frustrating and rewarding. With a little bit of experience and lateral thinking, hopefully the sum of different experiences will balance out on the rewarding side.
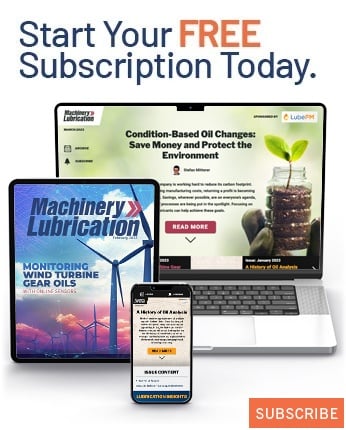