Sentelligence has created a flexible platform technology that can be applied to a wide range of fluid condition and quality monitoring systems for the automotive, industrial and mining industries. The company name, Sentelligence, is derived from the term "intelligent sensing," which defines the functionality and fundamental principles of the sensing devices developed by the company.
Demand for productivity improvement has led to a paradigm shift away from scheduled preventive maintenance toward condition-based maintenance practices in many industries. Traditional diagnostic methods of extracting fluid or other types of samples and sending them to a laboratory sacrifice valuable time. Also, it can be expensive if you're not in search of the root cause for a particular condition.
In today's environment, it is critical to know the general health of equipment in real time to optimize equipment productivity; and when downtime becomes apparent, to have the visibility to plan for it. From a product-development perspective, the company interprets this as miniaturizing key laboratory functions into a cost-effective, rugged intelligent sensor, then providing a meaningful communications capability to deliver useful and timely information.
The key to the sensor technology starts with matching key condition metrics from the laboratory with user requirements and ends with the combination of selected optoelectronics that provide the desired optical or spectral response within a given application or fluid environment. For example, the company was asked to identify key condemnation factors when attempting to extend oil drains in diesel engines.
Because major changes in emissions requirements are altering the composition of oil additives, reducing the sulfur content in fuel and altering the engine combustion process with the addition of EGR, identifying key factors for oil condemnation can be as fluid as the oil itself. While acid build in oil is a concern, it can be managed with advanced additive formulations and smart filter technology. Soot, however, cannot. Thus, the monitoring of soot requires that the primary optical function used in the company's oil condition sensor is light/energy absorption in the visible and near infrared regions of the electromagnetic spectrum. With adequate real-time monitoring, the doubling of routine oil drain intervals in diesel engines, as well as other equipment, will be available in the near future.
Additional forms of measurements, such as light attenuation, scattering and fluorescence optical emissions, are useful diagnostics for the characterization of specific fault conditions and/or the presence of undesirable materials. The majority of changes in properties or fluid performance can be correlated to the optical/spectral responses within various sensing components. These can be combined with the optimized coupling to an optical interface, which is designed to meet the needs of a specific application or operating environment. Generally, optics are nonconventional and are highly optimized to ensure efficient coupling of the key optical components of the sensing element and fluid.
An example would be the urea sensor under development by the company for a large European OEM. Changes in emissions regulations in Europe have prompted the use of selective catalytic reduction (SCR) systems for post-combustion control of NOx emissions. The quality and concentration of a urea-and-water mixture is important to the operation of the system. The sensor's platform design uses several different wavelengths to identify both concentrations of urea in the fluid and selected types of potential contaminants under potentially severe operating conditions. The sensor is a cost-effective way to help the system adjust to small changes in fluid concentration and help identify the source of potential problems in a relatively complex system.
The patented conceptual design can be applied to a variety of other fluids used onboard mobile or stationary equipment and in manufacturing process controls.
The sensor components are solid-state and are selected to perform under rigorous conditions encountered in commercial engine, transmission and hydraulic applications under normal extremes of temperature and pressure. All of the sensors have onboard data-handling functions that provide full sensor control, data acquisition, data pre- and post-processing, communications, and fault condition diagnostics.
The data acquisition and signal conditioning is handled by the onboard electronics, as well as the data processing and fluid condition assessment. In their primary intended use, the sensor devices interact directly with the fluid that is being monitored. If the measurement has been made indirectly or the fluid has been chemically modified, alternative configurations are possible, which can extend the role of the sensors into measuring reactive gases and vapors.
LayoutThe optoelectronic sensor provides a functionalized schematic for the sensors, where the optical interface and the optoelectronics are customized for individual applications. Figure 3 shows a general layout of this sensor. The customization is based on the selected wavelengths and dimensions of the interface.
Up to four wavelengths can be independently monitored by the coupling of the source to an independent set of optical detectors. Individual wavelengths can be separated by position and modulation frequency. In the standard sensors, the range of the wavelength is considered to be from the short wave visible (400 nm) to the end of the short wave near infrared (1,100 nm).
If necessary, the optical interface can accommodate more wavelengths, which is useful for even the most sophisticated applications. While most applications are handled by four default wavelengths, the sensor also features a reference detection system that monitors the source emissions from the optohead prior to the optical interface.
Condition diagnostics relates to the fluid in the component. For this type of measurement, the sensor monitors specific signals and trends. For example, the sensor keeps track of oil changes and top-offs in the oil condition monitor. However, it also tracks the trend in terms of rate of change and direction of soot concentration. Both trend rates and changes to trend rate, as well as deviations in the normal trend direction, are highly diagnostic and can be correlated to a number of performance conditions, including abnormally high fuel consumption and adverse conditions such as filter plugging and dispersant failure.
The sensors are fully programmable. The electronics include a boot loader that enables sensors to be reprogrammed and recalibrated. With condition monitoring, the sensor can be set up to handle normal, abnormally high and abnormally low trend rates, as well as alarm conditions.
Applicable DesignCurrently, two forms of the sensor are in the final stages of development. Customization to meet the specific needs of various applications is necessary, and because of the platform design, a practical measurement system can be tested for concept within a few months.
The sensors are designed for low-cost, high-volume production as well as for low-volume applications with maximum functionality and flexibility. The current fluid sensors can be adapted to a wide range of liquid media applications. And with minor modifications, they can be adapted to monitor certain gases and vapors (such as oxygen, carbon monoxide and reactive NOx gases).
The principles of signal handling, signal conditioning and data extraction can be extended within a platform-style concept to make base measurements beyond the current optical/spectral detection. Applications of spectral measurements derived from electrical property measurements and electromagnetic measurements can extend the applications beyond those currently defined for the optical sensors.
The current and projected fluid sensors designed by Sentelligence focus on diesel engine oils, gasoline engine oils, fuels (including bio-fuels), transmission oils, hydraulic oils, coolants, gases/vapors and all functional fluids.
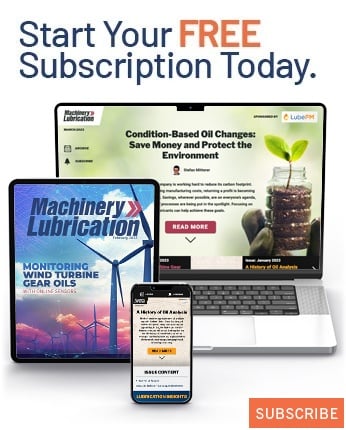