The study of journal bearing lubrication has been devoted to the understanding of the critical operating parameters of the bearing, namely the machined clearance and the film thickness needed for proper operation. There is a clear definition of the minimum film thickness that is prescribed by the bearing size, rotation and load.
However, it is equally important to consider particle size and the fluid cleanliness level required for journal bearing operation. Removal of clearance-sized particles is required for wear reduction, and can be achieved by implementing high efficiency filtration to lubrication systems equipped with journal bearings.
Journal bearings used in industrial turbines and compressors typically range in size from two inches to eight inches in diameter. The machined clearance of a journal bearing is the clearance between the sleeve and the journal when the journal is positioned symmetrically in the center of the sleeve and is equidistant from the sleeve on all sides. Machined clearances within bearings of this size are on the order of 25 microns to 50 microns for one inch of journal diameter.

The minimum film thickness is found at the closest point of contact between the journal and the sleeve. Theoretical analysis reveals that for these journal-bearing sizes under normal operating conditions, a 1-20 microns thick hydrodynamic film forms to separate the journal from the pads (Figure 1). Bearing manufacturers understand the important role that minimum film thickness plays in proper journal bearing operation and have provided formulas for determining this thickness at the point of use.
Since film thickness is dependent on fluid viscosity, as the fluid temperature rises, the film thickness may be reduced by as much as 20% for some lubricants. Theoretical analysis shows the minimum film thickness is between 1-20 microns; however, empirical results reveal that even though dimensional clearances within a journal bearing may differ, and the load and rotational speed may vary, the actual film thickness is on the order of approximately 10 microns.

There is a direct relationship between the minimum film thickness and the most damaging particle size. Particles of clearance-size can bridge the gap between the journal and the sleeve, causing bearing wear (Figure 2). Abrasive wear occurs when clearance-sized particles come between two surfaces that are under load, such as in the journal and the bearing.
The clearance-sized particles can enter the journal bearing through a clearance space, an oil supply line, or through lubricant supply holes or grooves. They are then carried into the contact area where the film thickness is at a minimum. The load of the bearing is transferred to the particles and these particles are pressed into bearing surfaces to act like cutting tools. This results in degradation of the surfaces, dimensional changes of the surfaces and the release of wear metals.

Wear rate measurements which compare journal bearing wear of two different materials (Babbitt and Copper-Lead) was obtained by Ronen, et al. as shown in Figure 3. These tests were conducted over a 20-hour period with interruptions for wear measurements, at five hour intervals. It can be seen that more than a ten-fold increase in bearing wear results from contaminated oil.

A study by Wantanabe, et al. provides the clearest evidence of the relationship between film thickness, particle size and journal bearing wear rate. These authors found that the wear rate depended heavily on the ratio of the film thickness to particle size. Surprisingly, the maximum wear rate occurred when this ratio was equal to one (Figure 4), meaning less wear occurs from particles both larger and smaller than the oil film thickness.
As a result of the abrasive effects of particles that are of the size of the minimum film thickness, removal of these clearance size particles is of great importance. Consequently, filtration requirements for these types of bearings should be based on the minimum film thickness formed under normal operating conditions.
Filtration plays a key role in reducing the wear rate of a journal bearing. Implementation of high efficiency filtration to remove clearance-size particles can therefore significantly reduce the abrasive wear rate of the journal bearings. The filtration requirement is most critical at the commissioning of turbines, compressors or other equipment and when the equipment is rotating at low rpm. It is at these times that the hydrodynamic film is the thinnest.
Unfortunately, some equipment designers tend to consider the overall capital costs rather than the technical requirements of the system when choosing filtration systems. Field experience has proven that this approach can result in much higher operating costs when the costs for repairs, maintenance, parts replacement and lost production are considered.
Given that the film thickness that exists under normal operating conditions is approximately 10 microns, the appropriate filtration should exhibit high removal efficiency of particles of this size and smaller. Since the film thickness is further reduced during startup and at low viscosity condition or with lower viscosity fluids, it is recommended that the filter employed exhibit a high removal efficiency of particles down to 5 microns or finer.
For machines equipped with journal bearings, the filter element should be rated at no less than B7(c)>1000, where micron(c) refers to filter ratings measured per the new Multi-pass test method, ISO 16889. This represents a removal efficiency of 99.9% for particles 7 microns(c) in size and larger.
This same high efficiency filter will remove 90% of 3 microns(c) particles as well. The use of such filters should result in maintaining fluid cleanliness
levels at 16/14/12 or better (ISO 4406).
In addition, it is also recommended that the system be flushed to an even cleaner standard prior to machine commissioning to provide maximum protection against abrasive wear under critical start-up conditions.
Conclusion
Contamination control aimed at the removal of clearance-sized particles is strongly recommended to extend journal bearing life. Bearings in the 2-8 inch range have an average film thickness of 10 microns or smaller; consequently, filter elements rated at 7 microns(c) (B7(c)>1000) should be employed to eliminate the harmful effects of abrasive wear on journal bearing surfaces.
REFERENCES
1. Duchowski, J.K., “Examination of Journal Bearing Filtration Requirements”, presented at 51st STLE Annual Meeting, Cincinnati, OH, May 19-23, 1996.
2. Raimondi, A.A. and Szeri, A.Z., “Journal and Thrust Bearings,” in CRC Handbook of Lubrication and Tribology, 2, Booser, E.R., ed., CRC Press, Inc., Boca Raton, FL, pp 413-462, (1994).
3. “Guidelines for Maintaining Steam Turbine Lubrication Systems,” Electric Power Research Institute Publication EPRI CS-4555 Project 1648-7, Final Report, EPRI, Palo Alto, CA (1986).
4. Winer, W.O. and Cheng, H.S., “Film Thickness, Contact Stress and Surface,” in Wear Control Handbook, Peterson, M.B. and Winer, W.O., eds., ASME, New York, pp 81-92, (1980).
5. Booser, E.R., “Bearing and Lubrication Technology,” Enchotech Incorporated, Schenectady, NY (1995).
6. Gardner, W.W., “Hydrodynamic Oil Film Bearings - Fundamentals, Limits and Applications,” Waukesha Bearings Corporation, Waukesha, WI, pp 2-15, (1982).
7. “Hydraulic Fluid Power - Fluids - Method for Coding Level of Contamination by Solid Particles,” International Standards 4406.2, International Standards Organization, Geneva (1999).
8. “Hydraulic Fluid Power - Filters - Multi-pass Method for Evaluating Filtration Performance,” International Standard 16889, International Standards Organization, Geneva, (1999).
9. Ronen, A., Malkin, S., and Loewry, K., “Wear of Dynamically Load Hydraulic Bearings by Contamination Particles.” Journal of Tribology, 102, pp.452-458, 1980.
10. Wantanabe, S. Saki, K., Asanabe, S., and Fukutomi, M., “Evaluation of Wear Life of Journal Bearings by Contaminated Oils,” Proc. JSLE International Tribology Conference, Tokyo, Japan, pp. 85-90, 1985.
Contact
Pall Corporation
25 Harbor Park Drive
Port Washington, NY 11050
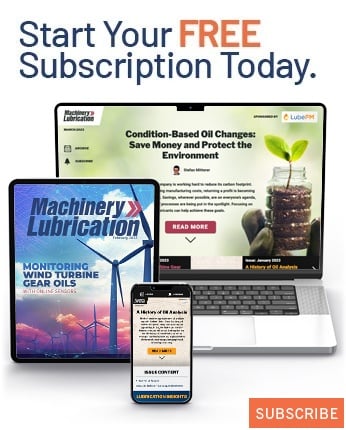