Note from Editor
This paper was presented at Practicing Oil Analysis 2000 International Conference
and Exhibition and was published in the proceedings. Due to the popularity of
this topic we chose to re-print this paper in the magazine. It has been divided
into two parts due to the length. Converting to Condition-Based Oil Changes
- Part II will be published in the March-April 2001 issue of Practicing Oil
Analysis magazine.
Introduction
Every year, millions of gallons of lubricants are prematurely changed in equipment
resulting in the disposal of oils which still have remaining useful life. The
practice of Preventive Maintenance results in oil changes and equipment repairs
done at predetermined intervals without regard to oil and equipment condition.
This practice is still utilized by many companies and results in high economic
loss from both the cost of new and disposal of old lubricants. Also, lubricants
can exceed their useful life before the scheduled change interval resulting
in premature equipment failure based on poor lubricant quality.
The more progressive companies utilize oil analysis to schedule oil changes resulting in the maximization of lubricant life and a proactive approach to preventing equipment failures related to oil quality.This paper will examine the use of oil analysis as a tool to monitor oil condition, thereby maximizing oil and equipment life. Each of the major tests used to determine oil condition will be examined as it relates to lubricant life. Typical cautionary and critical limits will be established for each of the major oil types. These limits are based on reviewing many different published sources and interviewing other professionals.
The following industries will be discussed as they relate to oil types used and conditioning monitoring techniques. Real world case histories will be used to demonstrate successful practices:
Part I
- Chemical
- Pulp and Paper
Part II (to be continued in the next issue)
- Power Generation
- Natural Gas Engines
- Diesel Engines
Lubricant Degradation
Lubricants consist of either a mineral or synthetic oil basestock fortified
with additives to impart unique properties based on the application. The lubricant
degrades through a breakdown in the basestock such as thermal cracking and oxidation.
Also, additive depletion can result in making a lubricant ineffective by removing
the oil’s protective qualities such as antiwear, rust and oxidation protection.
Oil contamination is the overriding reason oil is condemned. Major contaminants
are particles and water.
Condition
Monitoring in the Chemical Industry
Chemical plants mostly contain pumps and compressors. Depending on the operation,
some plants have a large number of gearboxes. Many of the compressors are centrifugal.
R&O oils are used for pumps and compressors. Gear oils are also used along
with some hydraulic oils.
Larger plants have circulating oil systems for compressors that can range from 200 to 2,000 gallons. Many of the plants have the ability to recondition oil by removing water and particles with the use of centrifuges and vacuum dehydrators.
Typically oils are condemned because of contamination and cannot be reconditioned. Oxidation and additive depletion are not among the common reasons for replacing oils. Oil in small sumps (i.e., pumps and small gearboxes) is changed on a predetermined schedule without the use of oil analysis.
Flash point is not a routine test used by chemical plants, but it has been able to identify where process contamination can occur in compressors before serious problems arise.
Water limits are being tightened by many of the more progressive companies.
More plants are establishing ISO cleanliness code guidelines not to exceed 17/14 on compressors and 16/13 in hydraulics.
Viscosity changes usually result in contamination from process fluids and gases or adding the wrong oil.
FTIR cannot be used on synthetic oils that contain esters to measure oxidation. The two most common synthetics are diesters, which definitely absorb at the same wavelength as oxidation products, and polyalphaolefins, which usually contain a small amount of diesters in the formulation.
Oils that do not reach the cautionary stage are still serviceable. Once oils breach cautionary limits, plans should be made to schedule an oil change or reconditioning.
Case
History #1 - Oil Change Interval Doubled
A large chemical plant in East Texas used oil analysis to determine the optimum
change frequency cycle on centrifugal pumps. Normally, oil was changed every
year because the sumps are only 2 1/2 quarts. A statistical sample was taken
on the pumps and oil analysis was conducted. This resulted in the decision to
double the change interval to two years. The savings were calculated as follows
for 1,500 pumps:
Yearly oil saved 1,500
gallons @ $4.00/gallon = $6,000
Manpower savings - one hour/pump @ $30/hour = $45,000
This plant implemented the extended change program many years ago without affecting pump reliability.
Most plants routinely change pump lubricants every six months to once a year. Savings can be achieved by using oil analysis to lengthen the change cycle by verifying fluid condition.
Case
History #2 - Combining Oil Analysis with Lubricant Reconditioning
Many years ago, a large chemical plant located along the Gulf Coast developed
one of the most successful oil condition monitoring programs. This program resulted
in excellent equipment reliability and long oil life. The plant performs its
own oil analysis, which includes viscosity, AN, pH, particle counts, direct
read and analytical ferrography. It also has the capability to recondition oil
with the use of centrifuges and vacuum dehydrators.
This plant has 40 reservoirs of 500 gallons or greater for compressors, turbines and large gearboxes. Typically, oil is changed every three to five years, much longer than conventional change intervals. Some have gone five to eight years before a change. Sampling is done on a monthly basis.
Critical process pumps are normally sampled every six months. If a problem is observed, sampling becomes more frequent. Oil is normally changed yearly.The following criteria were established to determine when oil should be reconditioned, changed or sweetened (reconstruct vital additives):
- Oil reconditioning and/or sweetening will be done on reservoirs greater than 55 gallons to improve the oil quality.
- Perform oil change-outs for all oils contaminated with process fluids or corrosive gases.
- Using this plan, oils rarely need to be changed due to severe oxidation.
Condition
Monitoring in the Pulp and Paper Industry
The paper industry has a large number of gearboxes, pumps and hydraulics,
but the major piece of equipment in a mill is the paper machine. Paper machines
have large reservoirs that can contain 1,000 to 5,000 gallons or more. Hydraulic
reservoirs can hold up to 200 gallons and gearboxes can hold up to 50 gallons.
A paper mill uses many lubricants. Any program that extends oil life can have
significant impact on the bottom line.
Paper machine oils usually last five to seven years if they are monitored regularly and reconditioned on condition by removing water and particles. Therefore, oil analysis becomes very important in maintaining paper machine oil quality. Paper machine oils are unique in their formulations, containing not just rust and oxidation inhibitors, but also detergents and an anti-wear package. Since water separation is an important property, they contain demulsifiers as well.
Paper machine oils (PMOs) are expected to last at least five years. Therefore, it is important they be carefully monitored through oil analysis to extend their life. Demulsibilty and oxidation life is very important and should be monitored on a yearly basis on large reservoirs. If the cautionary limits are reached, plans should be made to sweeten the oil or, after consulting with the lubricant representative, add a demulsifier package.
Unlike some other oils, additive washout in PMOs is a common occurrence in the presence of high water rates. Therefore, additive depletion should be carefully monitored. Consult your lubricant representative regarding their minimum additive levels. Alternatively, run tests on new lubricant samples to baseline the additive concentration.
The standards for water level have been tightening on PMO’s in recent years. The more progressive mills have adopted these standards and are keeping their water level under 250 ppm. Previously, oil was not condemned nor reconditioned until water exceeded 5,000 ppm. With the ability to remove water onsite, there is no reason to run high water levels.
Case
History #3 - Clean and Dry Oil Extends Life of Paper Machine Oil
A large paper mill in East Texas decided to improve lubricant contamination
control in an effort to extend lubricant life. The mill has a large number of
hydraulic and gearbox reservoirs which had historically been changed every six
months. Oil analysis was targeted as a strategic part of their contamination
control program.
This mill improved its hydraulic and paper machine filtration by installing three-micron absolute filters. It installed desiccant breathers on the reservoirs to exclude particles and water. The plant has been able to keep its ISO cleanliness codes to 14/12 or lower. This has extended oil change frequency from six months to one year. Currently, the plant plans to further extend these levels based on oil analysis data.
The savings from extending oil changes for the hydraulic system and some gearboxes resulted in a reduction of 1,500 gallons/month in lubricant usage. This translates to 18,000 gallons/year or $72,000/year. This does not include manpower savings to change the lubricant, which is much greater than the oil savings.
Many of the paper machine oil reservoirs at this plant were being changed every three years. With a good oil analysis program and improved contamination control, the goal is to lengthen the change interval to six years.
Condition-based oil changes are proving to be very beneficial to the bottom line. It helps reduce downtime, which increases a machine’s output and saves money in the long run. Make sure you look for more condition-based oil change case histories in the next issue of Practicing Oil Analysis.
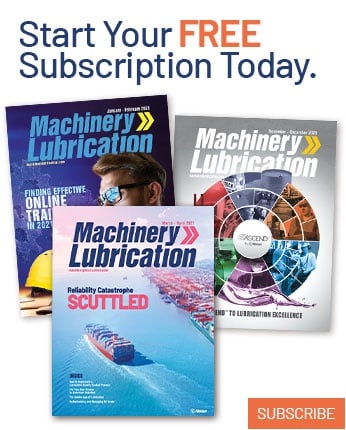