Background
The
idea behind the OILmiser FILLorDRAIN dates back to the mid- 1970s. I was assigned
the job of replacing a leaking cover gasket on a reservoir supplied to a local
sawmill. The fix was straightforward: transfer approximately 80 gallons of oil
into two empty drums. Remove the inspection cover. Replace the cover gasket.
Re-attach the inspection cover. Transfer the oil back into the reservoir. Clean
up the work area, and the job was done. With the assistance of sawmill personnel,
I stood ready to do my part when the reservoir was drained.
The next few hours were painful to watch. Under less than “clean room” conditions the filler/breather was removed. Then, in a tangle of hoses and confusion, suction and return wands were passed back and forth between reservoir and drum, each time contributing to a cleanup time that all but equaled the job time. With previous experience in industrial engineering - in an industry driven by efficiency and productivity - this was a nightmare of inefficiency and waste.
Two years later, this same sawmill was the first customer for the OILmiser FILLorDRAIN. With the support of a maintenance superintendent who was sold on the merits of preventive maintenance, eight hydraulic reservoirs were fitted with FILLorDRAIN.
The design criteria mapped out two years earlier was achieved:
- Establish a permanent suction/filling wand.
- Provide a simple retrofit for existing reservoirs.
- Provide an efficient and replaceable air filter.
- Establish a standardized reservoir attachment.
The
FILLorDRAIN
Using the conventional footprint (six holes, on a 2.88" bolt circle), a
FILLorDRAIN can be quickly retrofitted in the field. A typical installation
includes the following steps:
1. Clean the immediate area
of dirt and debris.
2. Remove the existing filler/breather.
3. Pre-cut a one-inch pipe to the proper length, threading one end only.
4. Turn this pipe into the bottom port of the FILLorDRAIN.
5. Position the “fluid access adapter” on the pipe, just clear of
the bottom of the reservoir.
6. Secure the fully assembled FILLorDRAIN onto the reservoir. This completes
the installation.
Removing uncertainty from a maintenance procedure translates directly into productivity gains. The payoffs are more predictable activity times, less resistance, more compliance and better results. With the FILLorDRAIN, much of the guesswork is removed from the fluid handling equation.
Contamination control ranks high on the list of priorities for the FILLorDRAIN. The standard filter element is a 5m (resin impregnated, pleated paper), automotive style air filter, easily accessible for inspection and replacement. In addition, a variety of top-end adapters accommodate most other types of air breathers, including desiccant breathers for water vapor removal.
While good filling and draining procedures are important for productivity, reducing their frequency remains the overall objective. To this end, oil sampling and oil analysis continue to deliver the needed confidence level. The FILLorDRAIN contributes to the reliability of the analysis by assuring the reliability of the sample.
The risk of introducing contamination in drawing the oil sample for analysis is significantly reduced. The large air passage in the FILLorDRAIN provides a clean and unobstructed passage for the sampling tube, directly into the reservoir.
But perhaps the best reason for using a FILLorDRAIN is to standardize oil maintenance procedures on every reservoir. Used as the suction or return wand in typical installations, or as the added return line for kidney loop applications, the OILmiser FILLorDRAIN can be the answer that bridges the divide between intent and implementation.
Contact Information
Dick Gangnon, President
JLM Systems Limited
23091 Westminster Highway
Richmond, BC, Canada V6V1B9
Toll Free: 888-736-8645
Fax: 604-521-1244
E-mail: info@oilmiser.com
Web site: www.oilmiser.com
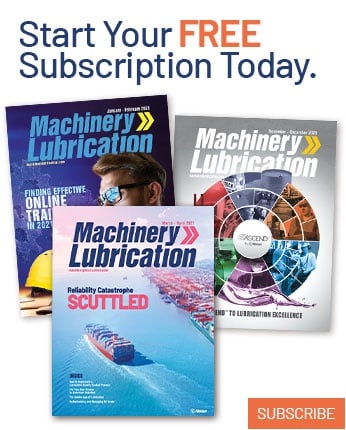