The
analysis of used lubricating grease has become a benchmark procedure as part
of the UK Health and Safety Executive guidelines on managing the safety of pedestal
cranes, specifically in the offshore exploration and production industries.
The duty holder, because he is responsible for safety, receives data concerning
the current status of critical plant components; in this case the slewing bearing.
When the asset is deemed suitable for continued service, the duty holder can
defer physical inspection. This can result in a bearing exceeding its design
life without intrusive inspection and without failure.
The safety record of lifting appliances in the offshore industry has improved dramatically over the last 20 years, mostly as a result of improved design, safety management procedures and increased safety awareness. Lloyd’s Register recognized that the provision of independent analysis service in crane slewing bearing reliability was an essential requirement if improvements in reliability were to be achieved. This was based on the operational experiences of its Lubricant Quality Scan (LQS) service. Simply using a general lubricant monitoring system would not be focused enough to deal with the unique issues surrounding this application.
Lloyd’s Register, along with major UK offshore operators, developed a test protocol to fully appreciate the limitations of such a service. They considered such issues as loading, bolt integrity, automatic logging of loads, relevant tests, limits of acceptability, frequency of sampling and other pertinent and practical procedures. One aspect of this is the application of grease analysis. Lloyd’s Register extended its testing and advisory services to include analysis of used lubricating grease from the slewing bearings.
UK legislation compels duty holders to be able to demonstrate the condition of all safety critical plants, either directly by inspection or by suitable noninvasive testing. For offshore cranes, the majority of critical components can be inspected while in operation. The slew bearing, which is a main structural load-bearing device that attaches the crane to the platform, is a potential source for catastrophic failure. Previously in the UK, there were instances in which the crane detached from the platform because the slewing bearing failed. UK legislation determined that in the future, the slewing bearing had to be physically inspected regularly every five years to reduce the risk of such failures.
This change lead to significant and often unnecessary costs. Ultrasonic testing of the bearing could not discriminate enough to ensure that a bearing was in a satisfactory condition for extended service. Even with fingerprint data references taken during the installation phase, ultrasonic testing, by itself, was not sufficient. Therefore, a reliable system based upon a low-cost procedure was needed.
A recent independent study compared the four most commonly used crane pedestal integrity testing methods: bolt security, ultrasonic testing, vibration monitoring and grease analysis. Considering failure modes and the probability of such failures against the cost of performing the monitoring, the study found grease analysis to offer the most effective solution.
The problem with grease analysis, however, is the integrity of the sample. The sample must be as representative as possible. A feature of grease analysis, as opposed to oil analysis, is that contaminants and wear debris are not uniformly distributed throughout the lubricant. This can lead to samples with huge variances in debris content. Specific to the application of slewing bearings is the extent to which the loaded surfaces are stressed.
Slewing bearings may never fully rotate because of crane location and its relationship to other fixed structures. Therefore, while there may be one physical sump or void, the lubricant will not migrate freely. To maintain confidence in the condition of race and roller, one must consider the loaded sectors and samples taken from more than one point. For conventional slewing bearings (< 4m dia.), convention and popular best practices dictate that four sectors are sampled: north, south, east and west; or forward, aft, port and starboard. With a representative sample, the analyst will have the ability to see the whole bearing. Larger bearings (> 4m dia.) may require more samples depending on the size and degree of movement. FPSO mooring turrets, some of which are also monitored by grease analysis, may have up to 12 sampling points due to the low relative movement and load configuration.
No single or mixed sample will truly reflect the condition of the bearing due to dilution and the corruption of evidence. As a result, relying upon mixed samples for analysis is not ideal and is generally used only because of commercial factors. For accurate statements of machine condition, the sampling method must be procedurally correct. The analyst will have to work with samples taken from positions directly adjacent to the loaded contacts.
One procedure to acquire a representative sample involves pumping in new grease to displace the final sample. Certain bearings with sampling ports allow for the insertion of specially designed tubes for grease analysis. If this is not available, the sample must be taken from the expelled grease at the bottom seal. This raises other sample contamination issues regarding the cleanliness of the seal prior to sampling. If a degree of cleanliness is not maintained, then environmental contaminants will be evident.
Assuming the sample is clean and from the correct point in the pack, the analyst must consider other issues regarding testing. For the most part, modern manufacturing techniques produce greases that are consistent and homogenous. However, certain conditions will lead to separation, water emulsification, contamination, etc. These features, along with wear debris, may not be uniformly distributed within the sample. Certain allowances must be made and certain procedures must be in place in order to enable the engineer to work within an acceptable level of confidence. Each individual sample must be mixed thoroughly. Prior to mixing, one should make a visual analysis to determine the presence of free or emulsified water, and the presence of debris such as visible metals/fibers.
The condition of the bearing is the focus; the condition of the grease is of secondary importance. Therefore, tests relating specifically to the grease are of little value. The engineer needs to know what contaminants are present and what they indicate in respect to the safe operation and reliability of the bearings. Because of this, the test protocol component of the bearing management program has been developed to be as cost effective as possible. That is, the tests focus on the presence of metallic elements and water.
To analyze the grease for metals, the whole of the sample should be tested. As the preferred method of identifying and quantifying metallic elements, Inductively Coupled Plasma (ICP) spectroscopy does not detect larger particles (>10mm). Therefore, greases cannot be used without dilution using the direct spray method. Because sample dilution would lead to further inaccuracies, acid digestion of an ashed sample is the preferred method. This ensures that all materials within the sample are measured, because particle size is no longer a limiting factor. The sulphated ash percentage, derived during the preparation of the sample prior to metal analysis, should also be quoted as an initial indicator of base components and contaminant content.
Typical raceway material specifications include 36NiCrMo 10V (2.5% Ni and 1.4% Cr), while typical roller specifications include X40Cr 13 (12% to14% Cr). This and other factors allow the analyst to determine whether the wear is predominantly from the race or the roller. Statistics show that race fatigue is more likely because roller damage is usually found after a period of abrasive contamination in which the rollers are forced to slide over hard particulates such as sand, rust or other externally generated contaminants. The engineer can therefore concentrate his efforts on iron, nickel and chromium. Certain bodies even suggest ignoring the iron content by focusing the ICP detector on the alloying elements only, which is a realistic strategy, yet untested.
Copper and other brass/bronze elements may indicate condition, dependent upon bearing design. These are seen where copper based spacer rings are used. LQS shows that copper based spacers tend to prevail in the larger slew rings such as those used on the turrets of FPSOs and moorings, and are not commonly used for offshore cranes. Secondary data from ICP includes lithium and calcium - basic metallic soap constituents; silicon, aluminum, magnesium - airborne dust and dirt; then sodium, zinc, phosphorus and lead - which tend to originate in the anti-corrosion, anti-wear and EP additives used to improve the performance of the grease.
This allows the analyst to check operational issues such as the correct grade in use, greasing schedule effectiveness and seal efficiency. The overriding point regarding the use of lubricating grease as a transport system for component/equipment condition data, is the quality and reliability of the sample and that the developing trends give consistent results for the purpose for which they are intended. Once accepted, the inaccuracies of used grease testing can be built into the reactive phase of the maintenance loop by rechecking for confirmation and by concurrent use of other parameters.
Lloyd’s Register has been able to provide duty holders with an effective system for monitoring bearing condition by adopting limits of acceptability for critical elements such as iron, nickel and chromium, and by the intelligent use of supportive techniques such as analytical ferrography to check morphology and criticality of debris type. This ensures that these systems operate within a continuously safe and reliable condition and that such a condition can be demonstrated.
If any organization is involved in the maintenance of cranes or other safety critical equipment regardless of industry sector, this type of approach can be considered to provide a viable solution.
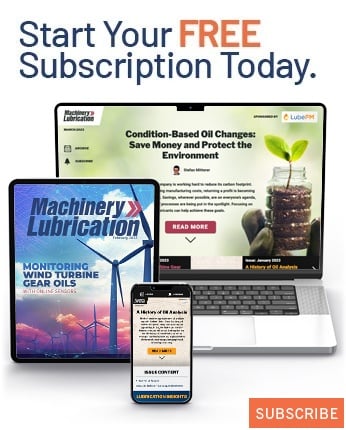