Evaluating data for oil samples can be a tricky venture. The person tasked with the diagnostics of sample data must be aware of the different parameters of the machine tested, as well as the laboratory testing procedures and processes.
When teaching the skills of data evaluation, much of the focus is given to topics such as setting alarms and limits and establishing targets. While the establishment of appropriate alarms is vital in helping to identify current and potential problems, there is a level of evaluation that simply cannot be defined by conventional black-and-white rules.
Apples to Apples
In addition to utilizing the standard alarming tools to trigger various condition potential and corresponding evaluations, there should also be a level of cross- equipment evaluation. Cross-equipment evaluation is a practice by which the results of like equipment are compared to determine if an actual condition exists or if there are similar values across the equipment that point to another possible situation.
During a recent on-site visit, oil sample results were reviewed to establish appropriate alarms for wear, contamination and fluid properties. It was noticed that four different pieces of equipment appeared to have the same diagnosis. All four samples came from different units with like components and received comments related to the viscosity of the samples. The recommendations for all four samples were to change the oil and look for the source of the cross contamination. The viscosity of each sample was said to be significantly lower than the oil that was identified as used in the components.
Upon closer inspection, it was noted that all four samples had the same sample date. The lab numbers assigned to the samples indicated they were in the same batch. Each sample had a lab number within three digits of one another. This resulted in an understanding that there were, in fact, two samples between each of the four samples in question.
The viscosity values of each of the four samples were within .3 centistoke (cSt) of one another. These values included 104.1, 104.3, 104.3 and 104.4.
Contact the End User
With results such as these found in equipment of the same make and model, there is an extremely low likelihood of a common cross-contamination condition that would result in values this similar. This condition should have alerted the evaluator to a situation warranting a direct contact with the end user. If this contact had taken place, the evaluator would have realized that the change of lubricant type was never correctly entered into the laboratory database, thus resulting in a comparison to an inaccurate baseline sample.
Although this should have been addressed before the sample results reached the end user, this situation is easy to remedy in an environment where the sample results are consistently reviewed and re-evaluated on-site prior to action being taken. Facing the greatest risk are end users who use automated software applications to import data and trigger work orders.
Some applications are capable of triggering key action comments that may be imported into the application. These action comments can create a work order. In the case described earlier, four work orders would likely have been created for lubricant changes. Without some type of human interface, this would have resulted in more than 40 gallons of perfectly good lubricant being thrown to waste while being replaced with the exact same lubricant.
Data evaluation of oil sample results requires a high level of skill and attention. It is important to understand some of the tricks of the trade to find the nonroutine situations that may arise.
Likewise, in the push for a more streamlined approach to data entry and work order generation, applications have been created to trust the results that come from the laboratory. The laboratory can be responsible for only so much, and the overall responsibility for work performed lies in the hands of the end-user. Knowing this, it is vital that some type of human involvement take place, even in the smallest action triggered via oil analysis. POA
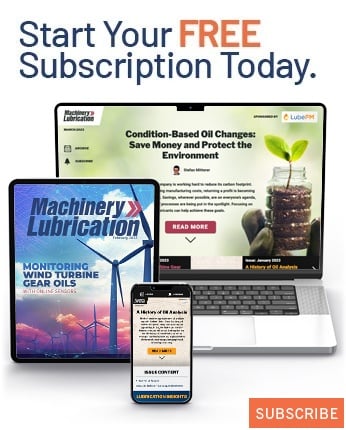