When an oil’s viscosity makes a significant change it is meaningful. The majority of the characteristics associated with wrong, contaminated or degraded lubricants will cause a change in viscosity.
Restated, when trending the viscosity of a used oil and no reportable change occurs, one can conclude that many of the things that could be happening to the oil are not yet occurring. These include oxidation, shear thinning, thermal degradation and many other common condemning conditions.
The signs of viscosity change are numerous. For many organizations, improperly diagnosed causes lead to problem reoccurrence (from the same cause) with each oil change. This occurs when oil labs see a change in viscosity and only recommend the oil compartment be drained and the lubricant replaced.
This article was written to provide an organized listing of common and not-so-common reasons for nonconforming lubricant viscosity. The varying applications of lubricants are so extensive and records of viscosity failures of in-service lubricants so incomplete, it is likely that many conditions responsible for viscosity extrusions have been overlooked here.
How Viscosity Changes
Think of an oil’s molecules as a large basket of mixed whole fruit. When you tip the basket, the fruit becomes a fluid body and flows out of the basket. In the basket there are cherries, plums, lemons, apples, grapefruit and melons. The fruit are different sizes and weights just like the molecules of common mineral oil.
When crude oil is refined, the molecules are separated by their molecular weight into broad groups (small, medium and large for instance). An oil’s viscosity basically correlates to the average size of the molecules of a given oil, i.e., small molecules are associated with low viscosity (thin oil) and large molecules with high viscosity (thick oil).
To change the viscosity, the average size of the molecules needs to change. Most mineral oils of a particular viscosity have molecules of an assortment of sizes. However, if the oil viscosity is high, the predominant size is large.
The opposite is true for a low viscosity oil. Going back to the fruit analogy, the viscosity of the basket of assorted fruit would change if all the cherries were removed. This would increase the average size of the fruit and the viscosity. In the case of a lubricant, hot-running oil can boil off small molecules, creating the same effect.
To decrease the viscosity, the melons could be quartered to make them smaller. With oil, molecules can “cleave” or crack into pieces when they are exposed to extremely high temperatures. Another way to reduce the viscosity of the fruit basket would be to add more cherries, lemons and plums to the mix.
This is similar to adding a low viscosity oil to a higher viscosity oil. The blended viscosity is somewhere in between the two. This type of thinning also occurs when a motor oil is contaminated with fuel.
The following summarizes how viscosity can change using our fruit basket analogy:
Decrease Viscosity:
1. Add more small fruit (mixing fuel with oil).
2. Remove some of the large fruit (electrostatic removal of oxide insolubles).
3. Cut the larger fruit into smaller pieces (shear thinning of VI improvers and lubricant cracking).
Increase Viscosity:
1. Add more large fruit (adding a more viscous make-up oil).
2. Remove some of the small fruit (boiling off light hydrocarbon fractions).
3. Glue several small fruit into a large poly-fruit cluster (oxidation, polymerization, etc.).
Zero-sum Viscosity Effects (two simultaneous offsetting events):
1. Small fruit and large fruit are added at the same time (when motor oil is contaminated with both fuel and soot, the fuel decreases the viscosity and the soot increases it.).
2. Cleave (cut into pieces) large fruit and remove small fruit at the same time (high temperatures thermally crack oil molecules to evolve gas that evaporates out of the oil).
Side Bar - What Causes Viscosity to Change (Click Here)
Early Detection, Key to Health Management
In some cases, slight viscosity changes are normal; for instance, the minor shear thinning of VI improvers of an all-season hydraulic fluid. However, in other cases, an oil’s change in viscosity might be the first indication of a more serious problem. For example, when an oil loses its oxidation stability the viscosity will trend upward.
If the problem is not recognized and corrected, an innocuous five percent uptick in viscosity soon becomes a 50 percent uptick, rapidly increasing to 500 percent. In such cases, the worse things get, the faster they worsen. So early detection is the strategic imperative.
There are two important strategies one should apply. The first is to set a proper baseline (don’t use published “product typicals”). Because the viscosity of a new oil can vary as much as 20 percent and stay within its designated ISO Viscosity Grade, the actual starting viscosity must be measured and recorded.
After all, it would be rather difficult to pick up a 10 percent shift in the viscosity of an in-service used oil if the correct starting viscosity is unknown and assumed to be somewhere in the 20-percent range. It is better to measure the new lubricant’s viscosity in the same way you are planning to monitor the used oil’s viscosity, with the same instruments, same temperature, same procedure, etc.
Because some lubricants are blends of fluids from different batches, sometimes progressively mixed new and used oils in a large reservoir, the “blended” starting viscosity is best set as the baseline, as opposed to the viscosity of any single batch of new oil.
Once a lubricant has been baselined, set limits. Many oil analysis software products will do this automatically. Because both southward and northward viscosity excursions are worthy of concern, limits in both directions must be set.
This, in effect, puts a “band” or “envelope” around the oil’s baseline viscosity. If the viscosity should trend higher or lower by significant measure, a limit is breached and the condition is flagged or alarmed.
Most top-shelf oil analysis programs apply tight limits above and below viscosity baselines. For crankcase oils, viscosity is typically measured at 100°C (212°F) while nearly all other lubricants are tracked at 40°C (104°F). If a reliable viscosity baseline is in place, it is recommended that cautionary and critical limits be set.
Figure 1 suggests some limits conventionally used for both crankcase and industrial lubricants. Once the baseline and limits are in place, data from used oil analysis becomes easier to understand. Refer to the troubleshooting chart in Figure 2 as a guide on how to interpret nonconforming viscosity data.
Figure 1. How to Set Viscosity Limits | |||
Limit
|
Crankcase Oils**
|
Industrial Oils**
|
Severe Environment Industrial Oils**
|
Critical (upper) |
+20%
|
+10%
|
+7%
|
Caution (upper) |
+10%
|
+5%
|
+4%
|
Caution (lower) |
-5%
|
-5%*
|
-5%*
|
Critical (lower) |
-10%
|
-10%*
|
-10%*
|
* Twice this amount for oils with VI improvers. |
Impact of Specific Gravity on Viscosity
Most commercial oil analysis laboratories deploy the use of kinematic viscosity using gravity flow capillary viscometers according to ASTM D445 (IP 71S1/97). One well-known limitation or interference relating to kinematic viscosity measurement occurs when an oil’s specific gravity changes. Typically it increases as the oil ages or becomes contaminated. This can occur at the same time viscosity changes or it can occur independent of viscosity.
If specific gravity increases without a change in absolute viscosity (the oil’s resistance to flow or shear) there will be a decrease in kinematic viscosity proportional to the change in specific gravity. While not a true viscosity change, it has the potential to be misrepresented as such. Examples of how specific gravity can increase viscosity include contamination (heavy solid and liquids), oxidation, evaporative losses, wear debris, glycol contamination, etc.
In many cases, when an oil’s specific gravity increases there is also an increase in absolute viscosity. The resulting effect is an understatement of the reported increase in kinematic viscosity.
Getting the Most from Viscosity Monitoring
Adding routine viscosity analysis to a lubricant condition-monitoring program makes good strategic sense. From the many different conditions that influence lubricant viscosity, as listed on the previous page, a lack of viscosity change is comforting indeed. For this reason, many reliability programs add viscosity analysis onsite and check critical lubricants and hydraulic fluids regularly.
When nonconforming viscosity trends occur, best practice is to determine the root cause of the excursion so that it can be prevented from reoccurring. This is particularly true in cases where viscosity changes early in a lubricant’s life and/or when large shifts in viscosity are observed.
Finally, as with most oil analysis instruments and maintenance technologies, viscosity analysis alone does not provide a complete picture of everything that is happening to the oil and to the machine. Other tools and methods are equally important in deploying your condition-monitoring arsenal.
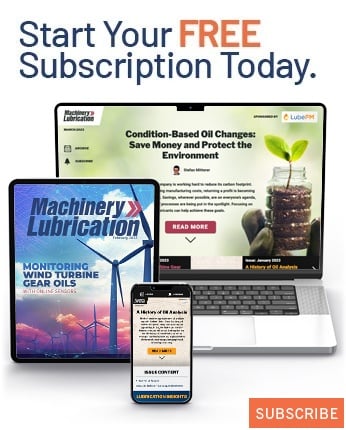