Like viscosity, the flash point test has always been a standard part of a lubricant’s specification. And, because of its low cost, simplicity and versatility, the test is popular among the used oil analysis community as well. Most commonly used as a quick pass/fail test for fuel dilution, more applications have surfaced in recent years. The lab analyst can deploy information about a used oil’s flash point to troubleshoot such problems as thermal failure, gamma radiation, solvent contamination, mixed (or wrong) oils, and antifreeze contamination.

What is an Oil's Flash Point?
The flash point is the lowest temperature at which the vapor above the oil sample will momentarily ignite or flash when an ignition source is passed over it. The flash point (typically 225 degrees C or 440 degrees F for mineral oils) is an indication of the safety hazards of a lubricant with respect to fire and explosion. The flash point and the slightly higher fire point are covered by ASTM D92 and D93.
However, the flash point should not be confused with the auto ignition temperature (AIT), which is the temperature (typically 360 degrees C or 650 to 700 degrees F for mineral oils) at which the oil vapor will combust spontaneously without an ignition source. This is an important property of fire-resistant hydraulic fluids in EHC systems on steam turbines.
According to ASTM, which first standardized the test in 1924, the flash point is the lowest temperature at which an ignition source causes the vapors of the specimen (lubricant) to ignite under specified conditions. The oil is said to have “flashed” when a flame appears and instantaneously propagates itself over the entire surface.
The oil flashes because a flammable mixture results when it is heated sufficiently, causing vapors to emerge and mix with oxygen in the air. The flash point temperature of an oil corresponds roughly to a vapor pressure of 3-5 mm Hg.
When a small flame (ignition source) is applied to the oil’s surface this vaporous mixture will burn momentarily and then extinguish if the critical temperature has been reached. Continued heating of the oil (typically 50-75° F above the flash point temperature) will cause the “fire point” to be reached. As the name implies, the fire point is the temperature at which a sustained flame results (longer than four seconds).
Using Flash Point to Detect and Quantify Fuel Dilution
Originally, the flash point was developed for the purpose of determining the fire hazard of fuels and oils being stored or transported. However, combined with other tests such as viscosity, viscosity index, and specific gravity, the flash point can help reveal both the quality of the crude oil from which the lubricant was derived and the quality of the refining process.
The flash point can also identify whether the base oil was a wide or narrow single cut or whether it represents a blend of two fractions (two base oils of different viscosities mixed together). And, the flash point may give some indication about the volatility and content of the most volatile components of the test oil. The flash point tells nothing, however, about the volatility of the oil as a whole.
Unlike mineral oils that start to evaporate long before their flash points are reached, some synthetics do not evaporate until they begin to decompose (destructive distillation). Hence, the flash points of these synthetics can range much higher than those of mineral oils of conventionally refined similar viscosities.
While there are more precise methods for measuring fuel dilution (e.g., steam distillation for gasoline and gas chromatography for diesel and gasoline fuels), the flash point is very useful as a pass/fail screening tool that is adequate for most used oil analysis applications. Because of the low flash points of most fuels, a sudden drop in flash temperature in a crankcase oil can usually be relied upon as an indication of dilution. However, there are exceptions, particularly in the case of diesel fuel.
Because there is often some overlap of the light-end volatile constituents of some lube oils with the heavy ends of the fuel, the presence of fuel dilution may be less distinct. This is particularly true when all of the fuel dilution is the result of blow-by, i.e., fuel entering the crankcase by way of the combustion chamber.
In such cases only the heavy ends may enter the oil with the oxidized light ends as a part of the exhaust gases. However, in the case of leakage of raw fuel, including dribbling injectors, all or a high percentage of the fuel light-ends can be blended with the crankcase oil. Another influencing factor is that hot running crankcase temperatures alone are often sufficient to boil off light-end fuel fractions, leaving the less volatile and more viscous heavy-ends mixed with the oil and potentially undetectable with the flash point test.
Fuel dilution reduces viscosity of a lubricant. However, if viscometry was used alone to screen for fuel, it is possible that little to no thinning could be detected for the reasons described above.
This is further compounded by the often interfering effects of viscous thickening from soot (also a product of blow-by), base oil volatility (thickening), and VI improver shear thinning. It is possible that a crankcase oil could be thinning from fuel dilution (or not if the light ends boil away), thinning from VI improver sheardown, thickening from volatilization, and thickening from rising soot load - all at the same time.
On the surface this might seem like a problem that’s not a problem if the blended viscosity is not changing. However, despite the neutral viscosity effect, potential destructive consequences, including loss of dispersancy, antiwear protection, and oxidation stability, represent a serious risk.
Flash point can enhance the ability of an oil analysis program to reliably identify abnormal levels of fuel. Even when used only as an exception test, it can guard against a false positive conclusion on fuel dilution from an original low viscosity result.
If, for example, the low viscosity was caused by improper makeup oil (of lower viscosity), the flash may confirm this by indicating no change from the new oil baseline. Fuel dilution, however, would almost certainly register a lower flash point from the reference new oil. Figure 3 shows a graph that presents the general relationship between flash point and percent dilution (raw fuel).
Because it often takes 30 minutes or longer to obtain the flash point using common Cleveland Open Cup or Pensky Marten Closed Cup procedures many labs prefer the Small Scale Closed Cup procedure described in ASTM D 3828. In this procedure (Method A) a target flash point is preset, say 20 - 30° C lower than the new oil baseline (Figure 4), corresponding to 1.5 - 2.0% fuel dilution.
The small quantity of oil used (2 ml) enables the target temperature to be reached quickly, typically within 1-2 minutes. The ignitor is then applied to initiate the flash. If a flash is obtained the test fails the oil, suggesting the possibility of fuel dilution.
In the case when an oil fails the flash point screening test, one or more exception tests could then be prescribed to both confirm and quantify the fuel dilution. Possible exception tests include gas chromatography and infrared spectroscopy. So too, determining the finite flash point temperature can be deployed to estimate percent fuel dilution (Figure 3).
Depending on application, for diesel engines, a cautionary limit is typically set at around 1.5% dilution (about -20° C flash) and a critical limit at 3% to 5% dilution (-40° C to -60° C flash). Application-specific calibration curves based on the actual test protocol (open cup, closed cup, etc.), motor oil brand/grade, and fuel type, will greatly improve precision in translating a drop in flash point to percent fuel dilution.
Besides viscosity and flash, other routine oil analysis tests that might reveal fuel dilution include elemental analysis (proportionally reduced additive concentrations), blotter spot test, crackle test, odor, and oxidation stability (e.g., RBOT and DSC). It has also been reported that viscosity index will change sharply due to fuel dilution.
Diesel fuel concentrations in excess of five percent have been found to cause premature loss of dispersancy, leading to deposits and filter plugging. This might be observed from the blotter spot test or by defining the a ratio of coagulated pentane insolubles to uncoagulated pentane insolubles (ASTM D 893), sometimes called the dispersion index. A low index number suggests poor dispersancy.
Other Applications For Flash Point Testing in Used Oil Analysis
It is not common for labs to employ flash point testing in applications outside of used engine oil analysis. However, depending on the machine application, operating environment, potential for contamination, and stressing conditions, a flash point test may provide the earliest indication of certain failure and root cause conditions.
Therefore its use should be considered in defining routine test slates for all used oil analysis programs. And, it definitely should be among several strategic exception tests used to confirm and diagnose occasional non-conforming conditions flagged by routine tests such as viscosity and infrared spectroscopy. Below is a list of applications for flash point testing other than fuel dilution:
Base Oil Cracking
Occasionally, very high, localized temperatures can lead to cleavage and gas evolution within the oil, lowering the flash point. This might occur from the high flash temperatures (not to be confused with flash point) of highly loaded squeeze films in the rolling contacts of certain bearings and gear units. It can also occur where machine surface temperatures are extremely hot due to close proximity to steam or furnaces.
The mis-application of high watt-density tank heaters can also cause thermal cracking. And, aeration of hydraulic systems commonly subject the fluid to extremely high adiabatic temperatures when air bubbles are suddenly pressurized (it can also occur in compressors and load zones of bearings). In hydraulic systems, the condition is referred to as micro-dieseling when the temperatures within the compressed air bubbles are high enough to auto-ignite.
Regardless of the source of heat, if localized oil temperatures are permitted to exceed 550° C there is real risk of cracking (depending on oil type and other operating conditions). The cracking can lead to the formation of carbon fines (coke) and low boiling-point volatiles within the oil that reduce the flash point temperature. Also, exposure to Gamma radiation, such as in the case of fuel handling hydraulics in a nuclear power plant, can cause gas evolution and lower flash point.
Contamination
Because the flash point is sensitive to low-boiling point constituents within the oil a change in flash point (up or down) might indicate the presence of an uninvited guest, i.e., a contaminant. Besides diesel and gasoline fuel, other common low-boiling point contaminants include natural gas (gas engines and compressors) and solvents.
Solvent contamination might be found when, for instance, a gearbox is cleaned out with naphtha, kerosene, or other flammable cleaner. Certain contaminants are known to actually raise the flash point. This can occur from a high level of water contamination in the oil, a common interference in flash point testing. Water contamination can also give a false low flash, particularly in certain mini-flash systems that use change in pressure to detect flash.
The boiling off of the water can give a false positive on fuel for instance. Water can also snuff out the flame in cases where a gas pilot flame is used. One solution to dealing with water is to add particles of calcium sulfates or calcium carbonate prior to performing the flash. Centrifuging is yet another solution. It has also been reported that coal dust and glycol (antifreeze) can synthesize volatile oil components resulting in an up-tick in flash point.
Wrong Oil / Mixed Oil
As shown in Figure 5, flash points for conventionally refined mineral oils can range from 165° C for an ISO 22 viscosity oil to a high 260° C for an ISO 1000 viscosity oil. Flash points also vary somewhat within viscosity grades as influenced by the crude oil type and refining process.
As previously mentioned, synthetic lubricants typically exhibit higher flash points than their mineral-oil counterparts. Therefore, it is sometimes possible to detect a wrong or mixed oil with the use of flash point testing. However, from a practical standpoint, other routine tests such as infrared spectroscopy, TAN, viscosity and color are more effective in alerting users to wrong or mixed lubricants. In these instances, the flash point test better serves in a confirming role.
Subtractions From the Oil
A lubricant subjected to high operating temperatures over a long period of time might lose a considerable portion of its light ends from evaporation. Some lubricants, because of base oil refining and “dumb-bell” blends, (a high viscosity mixed with a low viscosity to produce a blended medium viscosity) are more susceptible to volatilization than others.
Additionally, it is possible that the routine use of vacuum dehydrators at high inlet temperatures can cause evaporation of certain additives and low-boiling point base oil fractions.
Sampling and Sample Handling
In order to insure accurate flash point results it is important that a representative sample be presented to the instrument. For various reasons, this is easier said than done. It is worth noting that the precautions here are equally true for any test (FTIR, gas chromatography, etc.) used to measure low boiling point contaminants such as fuel.
Many fuels, for instance, will evaporate from the oil over time if the sample is not properly sealed. And, light fuel fractions can literally diffuse through the walls of certain sample containers such as those made of polyethylene and polypropylene. In such cases, PET plastic and glass bottles are preferred.
There may also be loss of light fuel fractions when vacuum sampling pumps are used to pull hot engine oils from crankcases. The vacuum generated not only draws the oil but can sharply reduce the boiling point of the fuel, leading to its evaporation. For this and other important reasons, the preferred sampling location for crankcase oils is on the pressure line between the pump and the filter using an acceptable live-zone sampling procedure.
Caution needs to be taken by the laboratory as well. Samples should not be left uncapped, subjected to vacuum, or heated prior to flash point testing or any test for fuel dilution. There are many detailed procedures and guidelines included in the ASTM flash point standards that should be observed to insure quality and test accuracy.
Standarized Flash Point Tests for Lubricants
In order to insure accuracy and quality it is best to follow standardized flash point procedures and instrument configurations. There are many different tests published by standards authorities such as ISO, ASTM, and IP. However, only three are commonly used for lubricants and hydraulic fluids. And, because of the differences in these procedures, a flash point temperature must be always quoted specific to the procedure employed. A brief description of the three flash point procedures follows (see also Figure 6):

Cleveland Open Cup (COC)
This test procedure utilizes an open metal container that is filled with the sample oil. The oil is then heated at a prescribed rate and periodically a small pilot flame (ignitor) is passed over its surface. This continues until a flash appears.

The oil temperature is then recorded as its flash point. The procedure is the most widely used in presenting a new lubricant’s physical and chemical properties. In the used oil analysis lab however, the procedure can require more oil than typically available and an exceedingly long test time.
And, for fuel dilution the lower limit of sensitivity may be inadequate because, being open, it does not retain the vapors long enough to get a flash.
Pensky-Marten Closed Cup
With this test, the sample is confined in a closed container into which the pilot flame is periodically introduced. Additionally, the lubricant is agitated during the heating period and the lowest temperature at which a flash appears is recorded.

As with the COC method, a considerable amount of fluid and time is needed to perform the test. However, fully automated instruments are available from various suppliers. In measuring fuel dilution, one advantage the Pensky-Marten has over the COC method is improved sensitivity to lower concentrations of fuel dilution (Figure 7).
Small Scale Closed Tester
This small-scale flash point tester goes by various names (e.g., mini-flash) and is perhaps the most adaptable for routine used oil analysis. While both the Pensky-Marten and COC can be used as a pass/fail tester, this procedure accomplishes the screening test (Method A) with only 2ml of fluid in just 1-2 minutes.
The finite flash point can also be obtained (Method B) but more fluid and time are needed. It is also worth noting that both the repeatability and reproducibility of this procedure is distinctly better than the previous two tests (Figure 8). Many high-production used oil analysis labs use this procedure with auto sampling in the pass/fail mode in screening for fuel dilution.
Conclusions
The flash point has endured the test of time. In many applications of used oil analysis the flash point test remains the method of choice in detecting certain contaminants and non-conforming lubricant conditions. In other cases the flash point serves as a dependable diagnostic tool or confirming test when a suspect condition has already been flagged. And, like most everything in the world of oil analysis, success in using the flash point depends on the careful adherence to such things as sample handling and test protocol.
Reference
ASTM Annual Book of Standards (1999)
Gill, Augustus H., A Short Hand-Book of Oil Analysis, J.B. Lippincott Company, 1898.
Caines, A. J. and R. F. Haycock, Automotive Lubricants Reference Book, SAE 1996.
Snook, Willett A., Lubrication, Volume 54, No. 9, 1968. Texaco Publication
Moller, U.J. , Lubricants in Operation, Mechanical Engineering Publications, Ltd.
Shublein, R.L., Synthetic Lubricants and High Performance Funtional Fluids, Marcel Dekker, 1999
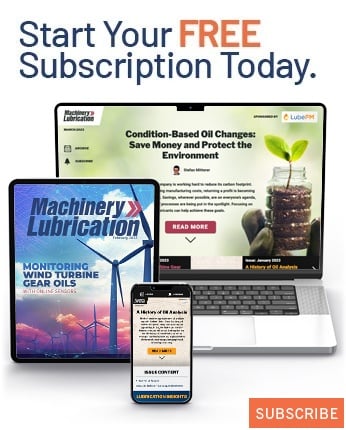