The latest dry lubrication technology from SKF, a leading knowledge engineering company, is enabling line efficiency to be optimized safely and cost effectively across a diverse range of food and beverage applications. A dry film of lubricant is distributed by a central system, minimizing lubricant consumption and eliminating the cost and operational implications of using water-based lubricants.
Effective lubrication is vital to the productivity of food and beverage production lines, but manual lubrication and conventional automated systems can escalate operational costs, contaminate products and present a hazard to line operators.
By comparison, the latest dry lubrication systems provide a safe, efficient and cost-effective solution. By limiting the moisture present on the production line, the systems optimize line efficiency and ensure product quality, while at the same time eliminating the risk of operator slippages and complying with strict health and safety standards.
Using dry lubrication prevents food and beverage products becoming contaminated by foreign bodies, which can be carried in conventional lubricants. Additionally, by minimizing both maintenance requirements and the volume of lubricant needed, automated dry lubrication systems can help food and beverage processing and packaging companies to keep waste and operating costs down.
Increasing the versatility and performance of its centralised lubrication systems still further is SKF’s extensive range of lubricants, ensuring the right solution can be found for any food and beverage application.
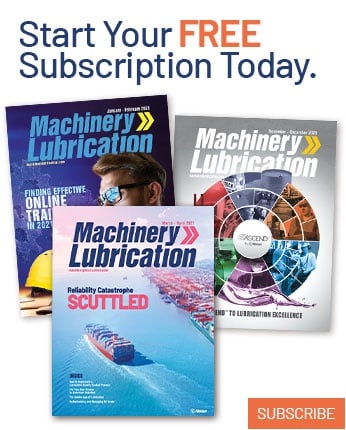