The past 10 years have seen a quiet revolution in electric motor bearing relubrication. Adherence to fundamentally sound practices, such as ensuring work area cleanliness during relube and following electric motor OEM lube selection and relube interval recommendations, has gained acceptance as standard operating procedures. Accordingly, many lubrication-related electric motor bearing failures have been reduced.
As bearing relubrication methods have improved, new lube-related challenges have emerged. These include the practice of running motors at higher speeds, which results in higher bearing temperatures, and the increasing use of variable frequency drives in electric motors, which can negatively affect both bearing and lubricant.
![]() |
Insulated bearings, such as the SKF Insocoat bearings shown here, feature ceramically coated outer rings. They prevent potential bearing and lubricant problems caused by electrical currents.
|
To counter these new challenges, industry is responding with solutions such as advanced polyurea-based greases and hybrid bearings that feature ceramic rolling elements. Hybrid bearings have lower lubrication requirements than standard steel bearings and are excellent in many lubed-for-life electric motor bearing applications.
New Long-Life, Low-Noise Grease
Although some electric motor bearings, such as those used with vertical motors for submersible pumps, are oil-lubricated via a sump system, the vast majority of motor bearings are lubricated with grease. Greases are composed of a base oil and a thickener, which carries the oil between its lattice-like fibers.
Base oils include mineral and other natural oils, and synthetic oils for high-temperature operation. Common thickeners include polyurea, lithium, calcium and sodium. Additives, such as antioxidants and antiwear compounds, are normally included in the mixture.
Recently, SKF selected an advanced rust-inhibiting, polyurea-based grease as the standard fill for its U.S. electric motor bearings. The new grease has a longer life expectancy and better quietness characteristics than the previously used polyurea grease.
It is compatible with other polyurea-based greases and lithium greases, which are widely used in industrial applications. To lubrication technicians and maintenance organizations, this means a reduced risk of grease in compatibility problems when relubricating.
There have also been improvements in bearing technology, providing electric motor OEMs with alternatives to all-steel bearings in some demanding applications. The use of variable motor drives is more prevalent today than in the past. These drives allow electric motors to change speeds and to operate more efficiently. But they can also cause electrical currents to travel through motor bearings. Strong electrical currents can damage bearing surfaces, causing pitting or spalling. Even currents not powerful enough to cause bearing damage can produce localized hot spots and burn the grease, destroying its effectiveness.
One potential solution is the use of hybrid bearings or insulated bearings in some variable frequency applications. Hybrid bearings contain ceramic rolling elements; insulated bearings feature a ceramic coating on the bearing outside diameter. Both hybrid bearings and insulated bearings are nonconductive and are designed to prevent current-related problems. In addition, hybrid bearings have lower lubrication requirements than steel bearings and can be substituted for steel bearings in some lubed-for-life applications.
![]() |
New advanced polyurea grease used as factory fill in today’s SKF electric motor bearings has a longer life expectancy than the previously used grease, as shown in the accompanying chart. Chart compares grease life expectancy for both standard steel and hybrid bearings. (Grease above is Hybrid Bearing Grease)
|
The Relubrication Decision
In many electric motor bearing applications, the critical question is not when to relubricate motor bearings, but whether to relubricate them at all. Although proper relubrication procedures are now generally standard practice, there is always the chance for error. When done improperly, relubrication can introduce solid or liquid contaminants into a bearing’s cavity, causing lubricant breakdown or damage to bearing raceways and rotating elements.
Also, technicians may inadvertently overgrease bearings, causing a condition called churning. Churning results in a higher operating temperature within the bearing and eventually leads to lubricant breakdown.
Even the lubrication procedure itself can have unintended consequences. Recently, for example, technicians at a power plant relubricated a shielded motor bearing using a grease gun. The entry of new grease caused increased pressure inside the bearing and forced the bearing’s shield into its rolling elements. Subsequently, the relubricated bearing failed prematurely. When it was removed for examination, the imprint made by the bearing balls on the shield was clearly visible.
With sealed or shielded bearings, which tend to be in the small- to mid-size range, the risks associated with bearing relubrication outweigh the potential benefits. The bearings are inexpensive and often the more financially prudent decision is to run them to failure.
Relubricating Larger Bearings
Larger electric motor bearings, such as cylindrical roller bearings used in some motor applications, are likely to require relubrication. Because these bearings tend to be more expensive, relubricating them makes financial sense.
Some relube tips:
Electric motor OEM recommendations regarding grease quantity and relubrication intervals generally reflect the expert input of the OEM’s bearings and lubricant suppliers. The recommendations are critical to achieving maximum electric motor bearing service life.
Although new-generation greases, such as the low-noise polyurea grease mentioned earlier, reduce the risk of compatibility problems, that risk still exists to some degree. When two incompatible greases are mixed, lubricating capability often deteriorates.
The resulting mixture tends to have a softer consistency and a lower operating temperature, leading to oil leakage and potential bearing failure. To avoid this problem, select a refill grease that is compatible with the original grease used in the bearing.
Most large electric motors are equipped with a grease fitting and a drain plug. When relubricating, thoroughly clean the grease fitting and the area around it to avoid contaminating the grease. Then pump new grease into the bearing through the fitting while allowing the old grease to exit through the open drain.
After injecting the recommended amount of grease, run the motor with the drain open until the bearing has a chance to purge all the excess grease. When the grease stops exiting the drain, plug the drain securely.
![]() |
Blackened lubricant shows the effects of electrical currents produced by variable frequency drives, which can create hot spots within the bearing. Solutions include the use of nonconductive hybrid or ceramically insulated bearings.
|
For certain applications, automatic bearing lubricators provide an alternative to manual electric motor bearing relubrication. These self-contained units, which deliver lubrication to bearings at a consistent rate, are particularly useful in remote or hard-to-access applications, such as exhaust fan motors located on factory roofs.
They yield additional user benefits in high-contaminant environments, where the consistent lubrication process flushes contaminants from bearing cavities.
The Continuing Challenge
Lubricant is the lifeblood of electric motor bearings. As industry continues to demand higher operating speed and performance from electric motors and their bearing components, it becomes increasingly important for maintenance personnel to stay abreast of advancements in lubrication technology and to continue following sound lubrication practices. In the end, it will be the lubricant and the lubricant technician that enable electric motors to run reliably at high speeds in day-to-day operation.
Bearing Shield/Seal Fundamentals
Questions regarding the use of shields and seals in electric motor bearings often arise among lubrication technicians. Here are some shield/seal basics that every lube technician should know:
-
Bearing shields help bearings retain grease and prevent large particles and contaminants from entering bearing cavities. Because shields do not make contact with the bearing inner ring, however, they cannot protect bearings from small, finely ground particles or from liquid
contaminants, including water. -
In high-contaminant applications, many users install sealed electric motor bearings. Unlike shields, bearing seals contact the bearing inner ring, preventing the entry of a wide range of contaminants, including liquids and small particles. But this seal-inner ring contact creates friction during operation and can potentially increase bearing operating temperatures. Consequently, sealed electric motor bearings are rated for lower speeds than shielded electric motor bearings.
-
Both sealed and shielded electric motor bearings are normally considered lubed for life. In other words, the life expectancy of these motor bearings is dependent on the life expectancy of their lubrication. Motor bearings without seals or shields, on the other hand, are usually designed to be relubricated.
-
When changing out sealed or shielded electric motor bearings, use similar replacements. Replace a shielded motor bearing with another shielded bearing of the same size and design; likewise, replace a sealed motor bearing with an identical sealed motor bearing. In high-contaminant environments or problem applications, technicians can consider replacing a shielded motor bearing with a sealed motor bearing for better protection against a wider range of contaminants. But as indicated above, this will usually require reductions in motor speed. Consult with the bearing manufacturer or electric motor OEM before changing components.
Chart and photos courtesy of SKF USA Inc.
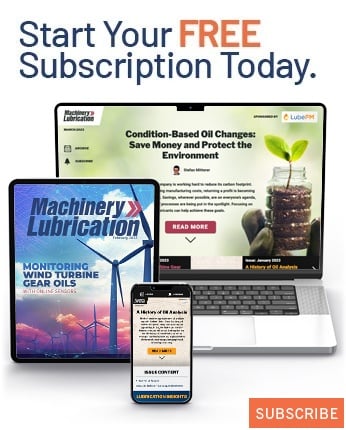