A group of Virginia Tech students have produced more than 200 gallons of biodiesel as part of a senior design project for the department of mechanical engineering. The Virginia Tech Bio-Fuels group (http://www.vtbiofuels.com/) is putting the fuel to direct use, running two pickup trucks on the liquid in a bid to not only stave off the use of foreign-bought oil but also to be environmentally friendly.
The B100 biodiesel is made from waste vegetable oil (WVO) obtained from local restaurants and processed in a nondescript warehouse along Virginia Tech's Plantation Road, surrounded by fields dedicated to farm animals. The 200 gallons were made during the past two months, mainly by processing equipment donated to the student team.
The project is overseen by Foster Agblevor, associate professor of biological systems engineering for the College of Engineering and the College of Life Sciences and Agriculture. Agblevor already has made headlines with experimental alternative fuels such as converting poultry litter into bio-oil.
The project began in 2008 when the now senior team consisted of juniors. The first year consisted of planning, research, and obtaining the funding and needed equipment for the project. This year consisted of more research, design, construction of process equipment, and converting the WVO into biodiesel for consistent use. The group produces B100, or 100 biodiesel.
"In the summer, the viscosity of the 100 percent biodiesel is low enough to use," said Christopher Block, who received his bachelor's degree in mechanical engineering in spring 2009 from Lake Forest, Ill. During winter months, certain biodiesels derived from animal fat have been known to gel or freeze in the tank. Therefore, the fuel must be mixed with regular petroleum to operate properly. "We learned via emissions testing that the B20 and B50 blends produce more favorable emissions than the B100 fuel," Block said, referring to mixes that use 80 percent petroleum and 20 percent biodiesel, and an even split, respectively.
The group limited its project to 200 gallons of biodiesel because of space limitations at the warehouse, but could produce more if needed. For now, the team can make up to 50 gallons at a time, so the potential for fueling a small fleet is possible. Already there are some takers.
"We are building a new team for next year who will take it to the next level," Agblevor said. "Giles County Wheatland Eco-Park would like them to install the unit on their property for education and other purposes." An unnamed company is interested in commercializing the project, and that the university's cafeterias could provide the waste grease product. "I will be encouraging [biological systems engineering] department to start using our biodiesel on some of the equipment that runs on diesel fuel," he added.
Block will remain on campus next year as he pursues a master's degree in mechanical engineering. He hopes to continue with the biodiesel project, but a permanent home for the operation must be found. The team had hopes to acquire a trailer so they could take the equipment around the state, including the Virginia State Fair, for tours. However, the idea proved too expensive.
The student team, in addition to Block, includes:
· Christopher Chelko of Huntersville, N.C., mechanical engineering;
· Matteo del Ninno of Alexandria, Va., mechanical engineering;
· Brian Eggleston of Blacksburg, Va., mechanical engineering;
· Blake Gordon of Bluefield, W.Va., mechanical engineering;
· Meredith Herrmann of Manasquan, N.J., industrial systems engineering; and
· Andrew Yard of Frenchtown, N.J., mechanical engineering.
The process of making the oil is straight forward.
1. The collected oil is pre-filtered using a centrifuge unit to remove sediments and food debris. Oil that hasn’t been used long is best. The filtering process continues as the oil is pre-heated in a tank, and then put through filter bags.
2. The level of the oil’s acidity is then determined. This determines how much methoxide, a combination of potassium hydroxide and methanol, to add to the oil. The vegetable oil is kept at roughly 140 degrees Fahrenheit during this process.
3. The mixture is agitated for roughly 8 hours at the same temperature. During the reaction stage, the catalyst -- caustic potash or Potassium Hydroxide -- attacks the oil and begins breaking the molecules apart into glycerol and fatty acid chains. Just after the molecules are broken apart, the methanol begins to react with the fatty acid chains. Glycerin, a side product, is produced when the glycerol molecules separated from the reaction mixture.
4. The solution is then moved into settling tanks, where the glycerin settles to the bottom of the tank while the freshly made biodiesel remains at the top. The glycerin is drained out, and used for several purposes including composting or with animal feed.
5. The biodiesel now must be washed with water that is sprayed into the tanks containing the unwashed fuel. As the water falls, excess methanol and soap molecules dissolve in the water and settles in the bottom layer, thereby cleansing the biodiesel.
6. The soapy waste water is now drained off the oil, leaving behind “wet” liquid biodiesel. To “dry” the fuel of water, the biodiesel is heated for several hours to evaporate the water.
7. The finished biodiesel is then pumped through a final filter into a diesel vehicle’s fuel tank.
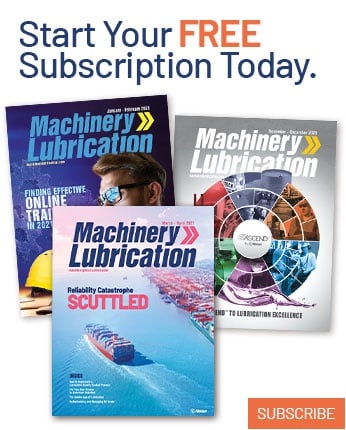