Over the years, dozens of articles have been written on the use of filter carts for decontaminating new and in-service oil. Though offline portable filtration for hydraulics or lubrication systems is not a new idea, it would seem that designing a filtration system for higher-viscosity systems is a relatively new thing.
For years, hydraulic shops and parts suppliers have built and sold simple filtration systems made with components intended for hydraulic systems to be used on hydraulic fluid. It all makes sense.
Take this hydraulic gear pump, use this hydraulic hose and attach these hydraulic filters, and you get a filter cart built with hydraulic components to filter hydraulic fluid. This has been happening for decades, and with great success. It's easy to clean hydraulic fluid. Its relatively low viscosity makes it easy to push through ultra-fine filtration.
The success on hydraulic systems was so great that people started to imagine what an offline system could do for critical gearboxes and other high-viscosity applications. In many cases, the same systems were used on lubrication systems.
Although the fluid may have moved through the system, in most (if not all) cases, the high-viscosity fluid would have sent even a new filter into bypass, allowing the fluid to move through the system unfiltered.
One of the more common oversights consumers make about filter carts is the size of their filter, or more specifically, the available surface area of filtration media and the level of filtration the media can provide. All filters are not created equal, and the most efficient filters may be too fine to properly decontaminate your lubricant.
Filters are designed so that the fluid to be pushed through the media is stripped of solid particles greater than the pore size of that particular media. As the fluid passes through the media, a pressure differential is created. Factors that influence the pressure differential across the filter media include media pore size, total media surface area, fluid viscosity and the amount of dirt already captured in the filter media.
So, why is understanding the pressure differential important? Most filter assemblies are designed to include a relieving valve in the filter head to allow fluid to bypass the filter when pressures exceed a given rating.
This protects the filter from damage during shock-loading in the system and also allows fluid to continue through the circuit even after a filter has reached its maximum dirt-holding capacity. If the pressure differential is too high, even on a new filter, the relieving valve may be fully or partially open, allowing some or all of the fluid to bypass the filter completely.
Figure 1.
Collect the Data
The first step to properly selecting filters to be installed on a filter cart is to collect data on the lubricant you intend to decontaminate. You must know the lubricant's viscosity at 40 degrees and 100 degrees
Celsius, the specific gravity, and the range of operating temperature anticipated for the in-service lubricants. You must also know the actual flow volume of the pump built into the filter cart.
For this example, let us examine an ISO 220 EP gear lubricant that has a viscosity of 220 centistokes (cSt) at 40°C and 18.7 cSt at 100°C. The specific gravity of this lubricant is 0.895. The flow volume of the filter cart pump is 10 gallons per minute. You then need to collect a sample of temperature scans off of components using this lubricant and intended for periodic decontamination with the filter cart you are designing.
From the data collected on 10 gearboxes under normal operation (Figure 1), you can conclude that the likely upper temperature limit would be 60.56°C, the lower temperature limit would be 29.44°C and the mean operating temperature would be 45.55°C.
Based on these operating temperatures, you need to figure the actual upper, lower and average operating viscosity of the lubricant. To do this, you need to plot the lubricant's viscosity data on a viscosity vs. temperature chart (ASTM D341) to understand the viscosity index (Figure 2). Viscosity index (VI) is the relationship of how viscosity changes with temperature.
With the viscosity data plotted on the graph, the viscosity of the lubricant at each operating temperature, or the viscosity index, is evident.
Once you know the viscosity index of a particular fluid, you know what the viscosity will be at any given temperature, and you can record this viscosity as the adjusted value (Figure 3).
Figure 3.
Selecting a Filter
Based on the information found using the temperature vs. viscosity graph, you have found that at the given operating temperatures of your in-service lubricants, the upper limit of viscosity reaches 431 cSt at 29.44°C.
Using this collected data, you then need to select a filter that will meet the cleanliness needs of the component. It is difficult to say with much accuracy how clean a filter will get your lubricant. Of course, you want to keep your systems as clean as reasonably achievable to suit the needs of the system, while keeping cost at a minimum.
For this example, let us investigate the possibility of using a b4 ³ 1000 spin-on filter with an effective filtration surface area of 1,266 square inches. Based on the flow curve information provided by the OEM on this particular filter, you know that at 10 GPM, the pressure drop across a new b4 ³ 1000 filter is approximately 3.5 psi when tested on a 32cSt hydraulic fluid at 37.7°C with a specific gravity of 0.9. Pressure drop is the value you need to monitor; to do this, you can use the following formula:
DPD = DPE (cSt/32) (Sg/0.9)
Where: DPD = the adjusted pressure drop
DPE = the pressure drop constant (taken from the pressure drop curve provided by OEM)
cSt = the viscosity in centistokes of the lubricant to be filtered, adjusted for operating temperature
Sg = the specific gravity of the lubricant to be filtered
The filter OEM will provide pressure drop vs. fluid flow information of their filter media and filter heads. The information given is typically based on a 32 cSt oil at 100 degrees Fahrenheit (37.7°C) and a specific gravity of 0.9. In this case, at 10 GPM, the filter media alone shows a pressure drop of 10 psi, while the filter head alone shows a pressure drop of 2 psi (Figure 4). The sum (12 psi) of both pressure drop calculations needs to be used for our equation.
Gearbox #1 DPD = DPE (cSt/32) (Sg/0.9)
Where: DPD = the adjusted pressure drop
DPE = 12 psi
cSt = 309.55
Sg = 0.895
Gearbox #1 DPD = 12 (309.55/32) (0.895/0.9)
Gearbox #1 DPD = 115.43
Following the same equation as above, the adjusted pressure drop is calculated for each scanned temperature (Figure 5).
Figure 5.
Calculations and Conclusions
Evident from the adjusted pressure drop calculation, assuming a clean filter, the pressure drop across the filter is enormous for all 10 gearboxes that were temperature-scanned (figures 5 and 6).
As mentioned earlier, standard filter heads include a bypass valve typically designed to allow full flow at 25 psi of back pressure. Given the adjusted pressure drops of our selected media rated at b4 ³ 1000, you can conclude that even with a clean filter installed on the filter cart, the filter will be in full bypass at each of these operating temperatures. The task now is to perform the same calculations on a newly selected filter.
Try to reduce the amount of pressure drop to as low as reasonably achievable so you can get the most value from the filters that you buy. Pressure drop occurs systematically as the filter media becomes clogged with debris.
To ensure you can reach the expected dirt-holding capacity prior to reaching the cracking limit of the filter bypass valve, you must begin the decontamination of the lubricant with a very low new-filter pressure drop.
Some options are still available if you must maintain the b4 ³ 1000 filtration that was selected earlier. Because pressure drop is a product of the type and efficiency of filter media, the total area of filter media available, the total flow through the media and the temperature of the fluid running through the media, you can attempt to change one of these variables in your favor.
You need to continue this exercise until you arrive at a result that satisfies not only your filtration requirements, but fits your budgetary requirement as well.
An Educated Purchase
Filter carts are an ideal way to periodically decontaminate lubricated systems. In an effort to aggressively decontaminate systems, plant professionals often specify filters that are much too fine for the intended lubricant.
In these cases, the lubricant often passes right through the bypass valve, never passing through the filter. Before buying that off-the-shelf filter cart, educate yourself on the specific requirements intended for your filter cart and pass this information on to your supplier. You'll be glad you did.
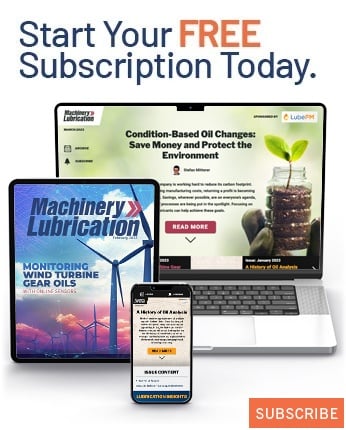