A gear is a component within a transmission device that transmits rotational force to another gear or device. Depending on their construction and arrangement, geared devices can transmit forces at different speeds, torques or in a different direction from the power source. The most common situation is for a gear to mesh with another gear, but a gear can mesh with any device having compatible teeth, such as linear moving racks. The most important feature is that gears of unequal sizes (diameters) can be combined to produce a mechanical advantage, so that the rotational speed and torque of the second gear are different than those of the first.
What follows is an explanation of the four most prevalent gearing types/configurations found in an industrial environment. The main purpose of this article is to inform you of a few popular gear types. I made a mistake earlier this month during a seminar and assumed that everyone in the class had an understanding of this topic. It is very hard to understand that different gear types have different lubricant needs if you do not first understand the different types or variations of gear sets.
Spur Gears
Spur gears are the simplest and most common type of gear. Their general form is a cylinder or disk with teeth projected radially. In these "straight-cut gears", the leading edges of the teeth are aligned parallel to the axis of rotation. These gears can only mesh correctly if they are fitted to parallel axles. A single spur gear is generally selected to have a ratio range of between 1:1 and 1:6, with a pitch line velocity up to 25 meters per second. The pinion is typically made from a harder material than the wheel. Select a gear pair to have the highest number of teeth consistent with a suitable safety margin in strength and wear.
Helical Gears
Helical gears offer a refinement over spur gears. The leading edges of the teeth are not parallel to the axis of rotation, but are set at an angle. Since the gear is curved, this angling causes the tooth shape to be a segment of a helix. The angled teeth engage more gradually than do spur gear teeth. This causes helical gears to run smoother and quieter than spur gears. Helical gears also offer the possibility of using non-parallel shafts.
With parallel helical gears, each pair of teeth first makes contact at a single point at one side of the gear wheel; a moving curve of contact then grows gradually across the tooth face. It may span the entire width of the tooth for a time. Finally, it recedes until the teeth break contact at a single point on the opposite side of the wheel. Thus, force is taken up and released gradually. With spur gears, the situation is quite different. When two teeth meet, they immediately make line contact across their entire width. This causes impact stress and noise. Spur gears make a characteristic whine at high speeds and cannot take as much torque as helical gears because their teeth are receiving impact blows.
Whereas spur gears are used for low-speed applications and those situations where noise control is not a problem, the use of helical gears is indicated when the application involves high speeds, large power transmission or where noise abatement is important. The speed is considered to be high when the pitch line velocity exceeds 5,000 feet per minute.
A disadvantage of helical gears is a resultant thrust along the axis of the gear, which needs to be accommodated by appropriate thrust bearings and a greater degree of sliding friction between the meshing teeth, often addressed with specific additives in the lubricant.
Worm Gears
A worm gear is used when a large speed reduction ratio is required between crossed axis shafts which do not intersect. A basic helical gear can be used, but the power which can be transmitted is low. A worm drive consists of a large-diameter worm wheel with a worm screw meshing with teeth on the periphery of the worm wheel. The worm is similar to a screw and the worm wheel is similar to a section of a nut. As the worm is rotated, the worm wheel rotates due to the screw-like action of the worm. The size of the worm gear set is generally based on the center distance between the worm and the worm wheel.
If the worm gears are machined basically as crossed helical gears, the result is a high stress point contact gear. However, the worm wheel is normally cut with a concave (as opposed to a straight) width. This is called a single-envelope worm gear set. If the worm is machined with a concave profile to effectively wrap around the worm wheel, the gear set is called a double-enveloping worm gear set and has the highest power capacity for the size. Single-enveloping gear sets require accurate alignment of the worm wheel to ensure full line tooth contact. Double-enveloping gear sets require accurate alignment of both the worm and the worm wheel to obtain maximum face contact.
Bevel Gears
These are gears cut from conical blanks and connect intersecting shaft axes. The connecting shafts are generally at 90 degrees; and sometimes, one shaft drives a bevel gear which is mounted on a through shaft, resulting in two output shafts. The point of intersection of the shafts is called the apex, and the teeth of the two gears converge at the apex. The design of bevel gears results in thrust forces away from the apex. With the bearing limitations, the gears have to be carefully designed to ensure that they are not thrown out of alignment as they are loaded.
Straight bevel gears are used widely in machine drive systems to effect 90-degree direction changes. They have the same limitations as spur gears and are, therefore, not used on high-duty, high-speed applications.
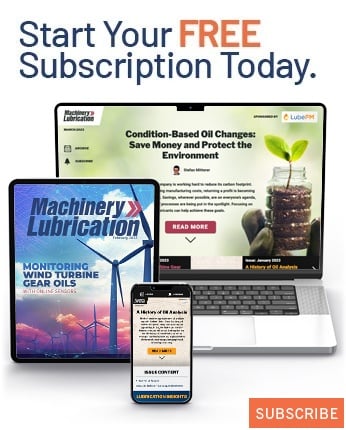