World-class lubrication programs are shifting away from interval-based regreasing schedules and into condition-based schedules. Choices for tools include simple high-frequency ultrasonic detectors and audio stethoscopes to digital data collectors that can directly interface with the grease gun.
Lube techs face new challenges as they harness the power of the acoustic inspection. This short article demystifies the technologies and techniques surrounding acoustic regreasing as an effective lubrication practice.
All sounds are produced by vibrations in bodies. In musical instruments, the sound is emitted by vibrating strings or a reed. Our voice is the result of vibrations from our vocal cords. The number of vibrations a body makes per second is called its frequency and is commonly referred to as hertz. Ultrasound is defined as “sound waves having a frequency above the limits of human hearing, or in excess of 20,000 cycles per second (hertz).”
So by definition, ultrasound is totally undetectable by human ears unless aided by instruments capable of translating ultrasound to audible sound. In the marketplace, these instruments are commonly known as ultrasonic detectors and have been used for various maintenance-related functions for more than 25 years.
Procedure
The lubrication practice that I am accustomed to is to pump a half-stroke of the grease gun and watch for a response on the analog meter either “up” or “down”. If the needle on the analog meter moves upward, wait 15 seconds for the needle to return to the original setting or lower before proceeding. If the needle doesn’t move downward or back to the mid-range after 15 seconds, suspend lubricating.
The bearing has enough grease and is now churning. If the needle moves lower than the mid-range after a half-stroke or several half-strokes, the procedure is to continue until the needle doesn’t move downward, but starts to move upward again. Again, at this time, implement the 15-second rule before proceeding or ending the lubrication practice.
Note: The above procedure is correct as long as the following volume is not exceeded. Using this formula, calculate the maximum grease charge in ounces:
G = 0.114 x D x B
G = the amount of grease in ounces, D = the outside diameter in inches and B = the bearing width in inches.
Recommended Practice
-
No matter whose ultrasound instrument you use, always calibrate the grease gun. Use a one-ounce container (shot glass), and pump grease into the container using half-strokes while counting the number of strokes it takes to fill it.
-
Be sure the area and fittings are clean. Wipe away dirt or grease before and after lubricating.
-
Know the lubricant to be used. Do not mix lubricants or grease.
-
Designate a grease gun to be used with an acoustic grease adapter and clean the adapter each time the adapter is moved to another grease gun.
-
Use half-strokes vs. full strokes when using a manual-lever grease gun.
-
When using a battery pack or pneumatic handheld grease gun, use a timing method such as 1001, 1002, etc. while holding the trigger to simulate half-strokes.
-
Make sure that drain plugs are accessible, open and unobstructed.
-
Know the type of bearing being lubricated. A sealed bearing can’t be regreased. Shielded or double-shielded bearings can be greased but done slowly as to not over-pressurize the cavity and push the bearing shield against the cage.
-
Use a grease gun with very little or no loss of movement of the pump handle.
-
Periodically clean the inside diameter of the pipe supplying grease to the lube point.
-
If grease or lubricant is seen exiting the bearing, schedule to replace the bearing.
Parting Thoughts
Acoustic lubrication is not a cure-all. It is, however, a methodology that can be learned and used to standardize within a plant. As with any new program, everyone must be on board, from management to the man or woman pumping the grease.
It takes time to implement. Time is money, and in today’s world of cutbacks, staff reductions and more for less, it may be hard to totally implement. If implemented, this practice will lessen downtime and reduce repairs.
Reference
Hall, Jim (2006), “Acoustic/Ultrasonic Lubrication”.
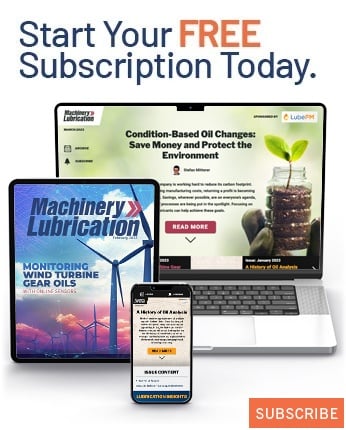