I often mention the wear debris universe when I lecture on oil analysis topics. This refers to the extensive array of wear particle technologies and tactics that can help reveal the true tribological condition of a machine.
Individually, these tools are often inconclusive when it comes to identifying the source, cause and severity of abnormal wear conditions. They may not even be able to identify the problem at all. Yet when used in combination, they can expose a vivid image of a current or impending failure condition.
A skilled analyst should be well aware of the strengths and weaknesses of these technologies and tactics. Not all of these tools need to be at your fingertips, but nonetheless should be available when called upon. Too often, an inexperienced technician will attempt to draw a premature conclusion from little more than a sliver of information in the wear debris universe.
Examples might be a muted iron trend from elemental data or stabilized ISO codes from particle counting. Used alone, these technologies might telegraph to the diagnostician the erroneous appearance of machine health (or disease). Unseen may be an incipient but serious wear condition in need of attention.
Common front-line technologies used for screening purposes include ferrous density analysis, elemental spectroscopy, particle counting and patch testing. Collectively, these technologies pack a powerful punch and are credited with scores of predictive maintenance "saves".
However, in a high percentage of cases, these technologies would not have earned their hero status if it weren't for the other tests and methods that peered deeper into the core of the problem.
These include secondary sampling points, filter debris inspection, magnetic plug analysis, sump sediment analysis, SEM-EDS, XRF, ferrography (all methods), acid-dissolution spectroscopy, particle heat treatment, particle impaction testing, chemical microscopy, digital shape profiling, percent of large ferrous particles, rotrode filter spectroscopy, TGA, gravimetric analysis, ultracentrifuge (separation of soluble metal fraction), pore blockage particle counting … and the list goes on.
In Search of the Pin Drop
We all know that when diseases are caught early, they frequently can be remedied without long-term consequences. The key is early detection and swift corrective measures. The same is true with lubricants and machinery.
In fact, for the lubricant analyst, ignoring the information potential of early detection could border on maintenance irresponsibility. While the previously mentioned screening technologies are essential to this strategy, so much more is needed for vigilant and comprehensive early stage fault detection.
One of the keys to this is the weak signal, also known as the "pin drop". Don't wait until problem trends shout the need for an unscheduled outage or repair. Instead, search for the quieter weak signal that doesn't demand urgent downtime to remove the root cause and remediate the problem.
By this, I'm not referring to proactive maintenance but rather incipient-stage predictive maintenance. Instead of catching a problem hours or days before a catastrophic event, the fault is red-flagged months earlier without costly business interruption.
Common strategies for detecting weak signals include:
-
Frequent sampling - Frequent sampling enables data to be reported earlier in the failure-development period.
-
Downstream sampling - By sampling downstream of the wear-generating source and upstream of filters and reservoirs, the data is not stripped by filtration or muted by dilution.
-
Clean oil - Clean oil strengthens the signal-to-noise ratio. Without the background noise of dirty oil, even the weakest signals sometimes can be detected.
-
Tight cautionary limits - Set your cautionary limits on key parameters sufficiently low to direct attention to a potential weak (but important) signal for further inspection.
-
Bundle trend plots - By combining several trend plots, even subtle data inflections can become more pronounced. Individually, they might go unnoticed, but when two, three or even four trend lines move in lockstep, you have the equivalent of a strong signal that needs immediate attention.
Seeking the Virgin Particle
Visual inspection of particles is always important to expanding the informational wear debris universe. There are various methods for doing this, but glass slide and patch ferrography are the most common. Success is often more about searching for the right particles to analyze than trying to interpret the meaning and identity of particles found in the routine sample pulled from a primary sampling port.
Too often, the primary sampling port only possesses the weak signal, but more revealing and comprehensive information must be sought out and found elsewhere for diagnostic purposes. What we're looking for are freshly minted and unadulterated particles. These are the particles in their original size and shape as produced from their generating source (bearing, gear, cam, etc.).
Older particles can become nearly impossible to recognize because they have been "reworked" by the machine and its environment through crushing, laminating or corrosive action. This can render the wear mode and location nearly impossible to recognize.
The best places to find virgin particles are used filters, sump sediment, magnetic plugs, chip collectors and similar sources. For circulating systems with high-capture filters, any particle larger than the mean pore size of the filter might represent a virgin particle (when sampling upstream of the filter). While the number of these particles may be few, their appearance and composition could be highly meaningful.
In sum, take wear debris analysis to another level by digging deep to expand your wear debris universe. Leverage contract specialty laboratories to provide analytical capabilities needed only "on exception". Develop new in-house skills and tactics that enable weak signals to be detected and virgin particles to be found and analyzed.
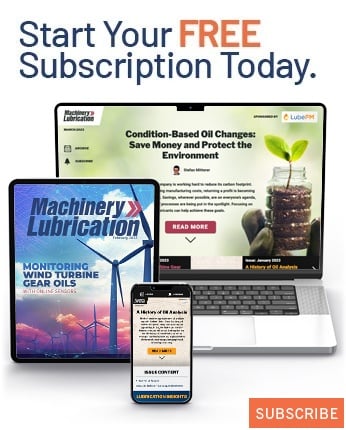