In the world of lubrication, hot topics come and go. Whether it’s synthetic oil, electric motor lubrication or ultrasonic-assisted regreasing, certain themes take on a greater profile from time to time. Lately, the hot topic that I’ve seen and have been asked more questions about than any other is varnish. From compressors to gas turbines, hydraulics to gearboxes, everyone seems to be talking about varnish. But, what is varnish? What causes it? And most importantly, how can it be prevented or eliminated?
In the past few years, significant efforts have been made to try to understand this ubiquitous material. You’ll find numerous articles, case studies and other information on the subject in Machinery Lubrication magazine and Noria’s own Lubrication Excellence conference proceedings. Some of the brightest and most competent lubrication chemists and engineers have studied the issue and done a tremendous job helping to explain the cause, effect and techniques for varnish mitigation.
But in talking to the layperson – the maintenance manager or reliability engineer who really doesn’t care about free radicals, carbon and oxide insolubles or peroxides, but rather how to control the problems associated with varnish – I still see a great deal of confusion and lack of understanding.
Unfortunately, the situation is not helped by a certain amount of information put out by well-intentioned but misinformed people or organizations. So in the interests of setting the record straight, I’ll attempt to shed some light on the topic of varnish and, in particular, try to provide some pointers to those dealing with this issue to help them wade through the plethora of fact and fiction.
What is Varnish?
First, let me state that there’s no such thing as varnish! By that, I don’t mean that varnish-like deposits in our machines are a figment of our imagination. Rather, varnish is a rather generic term used to describe the deposits formed by lubricant degradation. Usually when we’re talking about varnish and lubricant degradation, we’re talking about by-products of base oil degradation, but not always; in some cases, deposits can be caused by additive depletion or a chemical incompatibility between the additives and other foreign materials (chemicals, dissolved gases, water, etc.) that may be present in the lubricant.
When it comes to base oil degradation, there are four main ways in which base oils degrade: oxidation, thermal stress from hot machine (or other) surfaces, compressive heating due to air entrainment and electric arcing from stray currents. Since each of these mechanisms is different both physically and chemically, it stands to reason that the end result – the by-products of fluid degradation – also will be different. This is important to understand because the method by which we control and eliminate the deposits formed will depend on the method of formation.
Oxidation vs. Thermal Stress
A common mistake when talking about lubricant degradation is to state that the oil has “oxidized”; this is not always the case. In terms of lubricant degradation, oxidation has a very real meaning, representing the chemical reaction between oxygen present in the air with base oil molecules. Think of taking a bite out of an apple and watching the exposed flesh slowly turn brown over time. The brown coloration is a result of the oxygen in the air reacting with (oxidizing) the flesh of the apple.
Typically, oxidation builds up over a prolonged period of time and is not usually a result of an instantaneous event. While prolonged oxidation can lead to very tough deposits, by-products of oxidation usually can be dissolved in fairly mild solvents such as toluene or removed through mild abrasive cleaning.
Contrast this to thermal stress, which is caused by a high, localized heat source (machine surface, compressed gas bubble, electrical arc, etc.). Thermal stress usually occurs over a much shorter timeframe and results in deposits that are much harder to remove either through mechanical or chemical means. To understand the differences, consider cleaning a fry pan. If the food has been cooked slowly and properly, cleanup is fairly straightforward with warm water and dish detergent. But if the food has been burned, it will take much more scraping and maybe even cleaning solvents to remove all of the deposits. The same is true for oxidation vs. thermal lubricant failure.
Testing for Degradation
One of the tools we can use to detect the onset of lubricant deterioration is, of course, oil analysis. While later-term changes such as viscosity will occur with either thermal or oxidative failure, the fingerprint of early term oxidation is very different than that of incipient thermal failure. While with oxidation, acid number and Fourier transform infrared (FTIR) oxidation numbers typically rise, with thermal stress, acid number and FTIR oxidation will often remain low, appearing to be “normal” while other telltale tests such as FTIR nitration may prove a better indicator.
Color also is a good indicator of lubricant degradation. While a simple visual check is a good screen, other more sophisticated spectrophotometric tests such as quantitative spectrophotometric analysis (QSA) provide an excellent early warning of lubricant degradation. But with color changes, you should apply caution. While it’s true to say that an oil’s color will change when an oil oxidizes, the reverse is not always true. A change in color doesn’t always mean oxidation; it could equally be thermal stress.
Varnish’s Presence: Mineral Oil vs. Synthetic Oil
How do we prevent varnish? The answer to this question will depend on the reason the deposits are there.
For example, you will hear people tell you that synthetic oils or highly refined mineral oils will resist oxidation better than conventional oils. This is a true statement, but any oil (mineral or synthetic) thermally stressed by adiabatic compression (compressive heating due to gas entrainment) to 1,500 degrees Fahrenheit will thermally degrade.
Likewise, there’s the question of solvency. While highly refined mineral oils or synthetic hydrocarbons certainly resist oxidation better than most minerals oils, their lack of natural solvency means that once a problem starts, the deposit formation may occur much faster in a more highly refined oil. Conversely, the solvent action of conventional mineral oils is fairly mild. Just like dish detergent alone won’t remove burned-on food residue from a fry pan, conventional mineral oils will not solubilize stubborn lubricant deposits.
Techniques for Removing Degradation By-products
Once deposits form within a system, at some point, we’re going to want to remove them. There are a number of techniques for removing lubricant degradation by-products including the use of electrostatic separators, balanced charge agglomeration and cellulose media.
Numerous case studies have proved the efficacy of these techniques at controlling and removing deposits; but again, caution must be applied. While a certain technology may indeed prove useful in controlling “varnish” caused by oxidation, it may not do so well with “varnish” from thermal stress.
Root Cause Before Solution
What’s the answer to varnish mitigation? Just like a doctor should never prescribe a remedy until he or she has diagnosed the illness, we should resist the urge to jump to a solution that’s proven to remove varnish unless we know the symptom(s). Taking antibiotics to cure a viral infection won’t work. Likewise, using a technique to remove oxidative by-products may not work if thermal stress is the causative factor.
Therefore, before you jump headlong into a solution, try to determine the underlying root cause of varnish formation so you can be better informed to make the right choice of how to prevent and eliminate varnish from your machines.
As always, this is my opinion; I’m interested in yours.
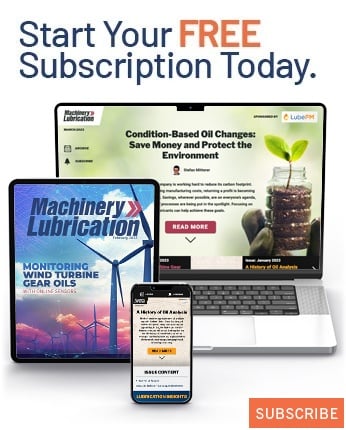