People love “do’s and don’ts” lists. A quick Google search will yield 10.9 million hits for what to do and not do. A quick scan through the endless supply of D&D lists will show that many of the subjects people feel the need on which to provide unsolicited consulting really don’t have a defined method of approach beyond common sense.
For example, the do’s and don’ts of air travel barely stretch outside the realm of common sense. Advice such as “Do not place your firearm in your carry-on luggage” or “Do not smoke while in the aircraft” goes without saying. Then there are the do and do-not-do lists for topics that are highly subjective such as fashion (Don’t wear white after Labor Day).
Thankfully, in the realm of oil analysis and machinery lubrication, few do’s and don’ts can be considered subjective. In this case, we’re talking about what to do and not do related to oil sampling for analysis. These simple rules will make or break the integrity of your sample, which is meant to drive your maintenance and reliability decisions.
Follow the Rules
Oil analysis is a condition monitoring tool designed to monitor:
- fluid properties, or the condition of the oil and the additives;
- fluid contamination; and,
- machine wear.
However, the analysis of a sample greatly depends on the quality of the sample itself. A high-quality sample translates into one that is rich with data and free from noise. The content of this article is nothing new. Dozens (if not hundreds) of articles, papers and books have had some advice for us to follow when extracting a sample of oil from a machine for analysis. However, as an industry, we don’t seem to get it right.
The same rules for oil sampling still apply, just like they always did. Here is the most recent do and do-not-do list for oil sampling from my perspective.
1. DO sample from running machines. DO NOT sample “cold” systems. This rule goes beyond simply starting the machine to take the sample. The ideology behind oil analysis is to capture a “snapshot” of the system at the time of sampling. The timing of the sampling should be when the system is under the greatest amount of stress.
Typically, the best time to sample a system is when the system is under normal working load and normal conditions. This can be a tricky task when sampling from a system that continuously cycles during normal production, such as the hydraulic system on an injection molding machine. It’s under these conditions that we’ll capture a sample that best represents the machine conditions most likely to cause accelerated wear.
2. DO sample upstream of filters and downstream of machine components. Filters are designed to pull out wear debris and contaminants, so sampling downstream of these data-strippers provides no value. However, taking a sample before and after a filter for a simple particle count will allow you to see how well the filter is currently operating. Obviously, we expect the particle count before the filter to be higher than after the filter. If it’s not, it’s time to change the filter. Condition-based filter changes can be very important for sensitive systems and expensive filters.
3. DO create specific written procedures for each system sampled. DO NOT change sampling methods or locations. Everything we do in oil analysis and machinery lubrication should have a detailed procedure to back up the task. Each maintenance point in the plant should have specific and unique procedures detailing who, what, where, when and how.
Oil sampling procedures are no different. We need to identify the sample location, the amount of flush volume, the frequency of sampling, the timing within a cycle to sample, and indicate what tools and accessories to use on that specific sample point based on lubricant type, pressure and amount of fluid required.
4. DO ensure that sampling valves and sampling devices are thoroughly flushed prior to taking the sample. DO NOT use dirty sampling equipment or reuse sample tubing. Cross-contamination has always been a problem in oil sampling. The truth of the matter is that flushing is an important task that is often overlooked. Failure to flush the sample location properly will produce a sample with a high degree of noise.
Flushing prior to sampling needs to account for the amount of dead space between the sample valve and the active system multiplied by a factor of 10. If there is a run of pipe 12 inches long between the sample valve and the active system that holds one fluid ounce of oil, you need to flush a minimum of 10 fluid ounces before taking the sample for analysis. Flushing the dead space also will flush your other accessories such as your sample valve adapter and new tubing.
5. DO ensure that samples are taken at proper frequencies. DO NOT sample “as time permits.” Many of those responsible for taking oil samples rarely see the results of the analysis. One of the most powerful aspects of oil analysis is identifying a change in the baseline of a sample and understanding the rate at which the change has occurred.
For example, a sample of new oil should have zero parts per million (ppm) of iron when tested as the baseline. As regular sampling and analysis continues, we may see the iron level increase. An increase of 10 or 12 ppm per sample may be considered critical; however, if the frequency is not consistent, what is considered normal becomes very subjective.
If our frequency of sampling is 12 months, a rise in iron of 12 ppm isn’t a major cause of concern. If our frequency is weekly, a rise in iron of 12 ppm is very concerning. Setting up the appropriate sampling frequency and adhering to it will allow for precise analysis and sound maintenance decisions.
6. DO forward samples immediately to the oil analysis lab after sampling. DO NOT wait more than 24 hours to send samples out. As mentioned earlier, oil sampling is much like taking a snapshot of your system at a point in time. The health of a lubricated system can change dramatically in a very short period of time.
If a problem is detected in a system, the earlier it is detected, the less catastrophic potential it may have. Jumping on a problem early will not only allow you time to plan for a repair, but the repair will potentially be less significant.
Apply Them Today
This do’s and don’ts list for oil sampling could go on and on. Each and every system will have unique and specific considerations for what to do and not do when sampling. The tips in this article will provide big bang for your buck and can be applied to most systems in your sampling program.
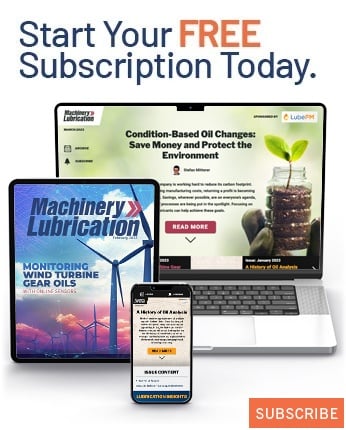