Keith Swearingen, our second "Get to Know ..." subject, is the lubrication coordinator at Exelon Corporation's Braidwood Generating Station, a nuclear power plant located in Braceville, Ill., 60 miles southwest of Chicago. He has been an Exelon employee for 33 years, including the past 14 on the nuclear side.
What has been your range of roles with Exelon?: My career began in fossil plants in the technical/engineering staff. We were responsible for efficiency testing of major electrical generating equipment. This position was discontinued in the fossil division after 19 years and I transferred to the results section of system engineering for the Braidwood nuclear facility 14 years ago. Coincidently, the results section also performs efficiency testing of major in-plant electrical generating equipment. One of the results section responsibilities is lubrication analysis for equipment condition assessment. I've been involved with lubrication analysis for more than 10 years now.
How did you get your start in machinery lubrication?: I first started in the lubrication analysis area in 1999. The regular lubrication coordinator was leaving the group and his duties were assigned to me. Back then, there was no lubrication program to identify, no lubricant result trends, no documented sample points or actions. The program had to be defined and created.
Keith Swearingen is the lubrication coordinator at Exelon Corporation's nuclear power plant in Braceville, Ill.
What training did you take to prepare you for your lubrication roles at Exelon?: I attended Noria's Oil Analysis Level I and II classes with Jim Fitch. As a result, I currently hold ICML's Machine Lubricant Analyst Level I and Level II certifications. What's a normal work day like for you?: I have other responsibilities and certifications other than lubrication analysis, so my day is a mixture of different predictive maintenance technology analyses and various reports that must be updated and presented to upper management. Conservatively, I spend about 20 percent of my day dealing with lubrication issues. These issues can be equipment assessment, contract management (for lube services or lubricant supply) and consultation of lubrication issues from other nuclear facilities.
What is the amount and range of equipment that you service?: Braidwood has approximately 300 lubrication sample points from various equipment around the plant. The equipment contained within the lubrication program can be as small as 10-horsepower motors, all the way up to 12,000-horsepower motors. Some lubrication reservoirs may contain 8 ounces of lubricant or up to several thousand gallons of lubricant. My duties also include analysis of diesel fuel oil and transformer oils. What lube projects are you currently working on?: I'm updating the plant's sampling methods to quick-disconnects for quicker, more accurate lube oil samples; reducing oil inventory; assessing replacement lubricants; and maintaining lube storage cleanliness.
What have been some of the biggest lubrication project successes for which you have played a part?: My program has caught many instances of degraded equipment before the instance became a catastrophe. For instance, about four years ago, the program identified a bearing problem on a large, 1,000-plus-horsepower motor. Increased lube oil monitoring predicted when the motor needed to be repaired before it became a complete motor failure. Such a failure would have required much more money to repair.
How does your company view machinery lubrication and/or oil analysis in terms of importance, strategy, etc.?: I believe Exelon regards oil analysis as one of the three most important equipment assessment technologies - the other two being thermography and vibration analysis. Oil analysis is seen as being just as important as vibration analysis in assessing equipment condition.
What do you see as some of the more important trends taking place in the lubrication field?: I see an increased awareness in the importance of reliable, accurate oil analysis in the overall assessment of critical, revenue-generating equipment.
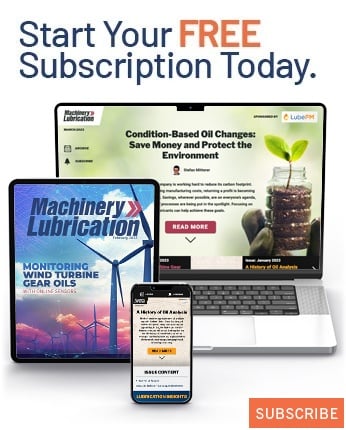