The health professional in white pulls on a new pair of latex gloves. He scans a cart, immaculately organized, and finds what he needs to begin the procedure - a vial, a pump, tubing. Each item is encased in a plastic bag to prevent the possibility of contamination. Suction. Removal. He intently peers at the extracted sample before having it sent to the lab for analytical testing and diagnosis. Under his care and that of an entire team of operators and technicians, the patient is going to be all right. This Ingersoll Rand Centac air compressor will be just fine.
Oil sampling and other machinery lubrication tasks are done with surgical precision at Energizer's battery manufacturing plant in Maryville, Mo. Standard operating procedures - crafted through education, training, idea sharing and consensus building - combined with levels of cleanliness and organization that border on obsessive compulsive make this site best in class, the winner of the International Council for Machinery Lubrication's 2009 Augustus H. Gill Award for excellence in the application of oil analysis in machine and lubricant condition monitoring.
"We are very particular about what we do here. Nothing is done in a half-hearted manner," says Rick Staley, the predictive maintenance steward at this 500,000-square-foot plant, located 90 miles north of Kansas City. "We are very particular about cleanliness. We have a procedure, a standard, for most everything. You might think that what we do is over the top (the gloves, the Tyvek suits, the plastic bags), but that attention to detail has made a difference for us in Maryville and for the company. What you put in is what you get out."
The showpiece of this high-energy production facility may well be the lubricant storage room. (Can your plant - or any other plant - say the same thing?) It's so clean, you could eat off the floor. But don't try it. Not that you'd get sick. You'd just get yelled at for dropping crumbs in this pristine work area.
"We don't fix this area up to show visitors," says Staley. "It stays this way. At any time, any day of the week, I wouldn't be afraid to bring anyone back here."
Upon a silvery-steel drainage grate stands 10 oil barrels. A fresh desiccant breather is perched on each one. Stainless steel piping connects each barrel to its own filtration unit. A dedicated dispensing pump is attached to the unit. On the wall behind each barrel is a series of laminated signs: a name tag that fully identifies the product that is in the container, a vibrant 8-inch by 16-inch color bar that serves as the plant's code for that particular lubrication product (for example, orange equals Shell Omala oil with ISO viscosity grade 460), and a material safety data sheet (MSDS) that outlines the proper procedures for handling or working with that substance in a safe manner. The grate also is the holding spot for pails of grease, which are fully identified with wall signs.
The colorful back wall also includes a booklet of plasticized sheets, an information guide for all who come in contact with this area. The book features standard operating procedures (for changing out a barrel, for filling a portable lubricant transfer container, etc.), a master color-code translation sheet and "Single-Point Lessons", best-practice tips for tasks such as how to correctly mix vanishing oil and Turbo T-32 oil.
"This whole area was built on best practices and from what we learned attending Noria courses," says senior engineering specialist Steve Harris. "Our storage area used to be a source of contamination and machinery issues."
The old configuration had one pump to transfer oil into cube containers on a rack. A myriad of valves and hoses made it possible to pump the wrong type of oil into a container. Once the oil got into a cube, it sat there until it was dispensed.
"Our objective in building this was to keep the oil in the original container. There's always the risk of cross-contamination," says Staley. "From our Noria training, we realized that receiving a barrel doesn't guarantee that you have clean oil. So, we filter it down to 3 microns ... we continually filter. Each barrel has its own pump and filtration unit. Every barrel is grounded. We also went to stainless steel for our piping because we learned some additives react to copper. We make sure we are getting quality oil to the equipment."
Neat and tidy bulk storage is just the first step in getting clean, quality lubricant to the equipment. Preventive maintenance mechanics don white Tyvek jumpsuits and latex gloves to transfer oil from a color-coded bulk station to an identical color-coded and labeled transfer container. Transfer containers are then placed on a mobile cart that is taken to the floor for PM routes. On routes, the color-coded transfer containers match up with colored tags affixed next to lubrication ports on machinery components.
Mobile carts are a source of pride and friendly competition among PM mechanics. While these carts have common features (such as a book of picture-heavy standard work procedures and a one-page document titled "PM Cart Expectations"), mechanics aim to outdo others by staging and fine-tuning their cart to be the neatest, most organized and 5-S worthy (a thing for everything and everything in its place).
The most public competition is between Larry Redford and colleague Duane White. Ever hear trash-talking about lube carts?
"Larry's cart is an eyesore," needles White. "I wouldn't be seen with that."
"My cart is made for work," retorts Redford. "This is a real cart. 'Whitey's' cart is a 'classic car'. It's just for show; it's for display."
Pride and persnicketiness carry through to cabinets, shelves and drawers, both in the tool crib and out on the floor.
"We really want to take 5-S across the board," says maintenance manager Matt Kovar. "Traditionally in plants, stuff is all over the place in cabinets and drawers. You can't find what you need. You don't know what's in there. The parts in there may be obsolete. It wastes time and money. We started doing something about it, and everyone's really chipped in."
Pictures are attached to all lube carts, cabinets, shelves, drawers, etc., showing what the storage should look like. Staley audits each one on a quarterly basis.
"If there is a gap between the item and the standard, we get with the mechanic in charge of that storage and make sure he or she knows what the gap is," says Kovar.
PM mechanics Larry Redford (left) and Duane White have a friendly rivalry about who has the neatest, best organized and most useful mobile cart.
Standards are Set, FollowedWorkers (both salary and hourly) at Energizer's factory in Maryville really do take standards seriously. That's because those standards are based on facts (best practices that impact productivity, reliability, profitability, etc.) that have been agreed upon by a large group of cross-functional representatives who are knowledgeable about the task.
Input, exploration, consensus building and formalization led to the establishment of a standard for world-class oil sampling. The standard, based on Noria training materials and refined to Energizer's needs by the Maryville plant's predictive maintenance team, is detailed in a photo-laden instruction packet that can take a technician step by step through the process of obtaining a clean, representative sample.
The 20 steps are:
-
Select the correct sample bottle - one that is clean and contaminant free.
-
Select a correctly sized, sealable bag that will fit the sample bottle.
-
Insert the bottle into the bag and seal.
-
Label the bag with the proper machine name and number from which the sample will be taken.
-
Keep the vampire-type vacuum pump in a sealed bag until it's ready for use. The polyflow sampling tube also should be in a sealed bag.
-
Install an old bottle on the pump and insert a 3/4-inch polyflow line, tightening the locking nut.
-
Unscrew the lid from the sampling bottle in the sealed bag.
-
At this point, a small sample should be pulled from the machine in the old bottle to assure all contaminants are removed from the sampling port.
-
Remove the old bottle from the pump, remove the sampling tube and install the lid on the old bottle. You are now ready to collect a sample. Use a new, clean sampling tube for each sample taken.
-
Leaving the bottle in the bag, screw onto the pump.
-
Insert a clean sampling tube through the pump and bag and into the bottle. Tighten the locking nut.
-
Use the needed length of sampling tube to insert into a gearbox/reservoir, taking care not to contaminate the tube on the sides or bottom of the area to be sampled.
-
Pull the pump handle and fill the bottle to the desired level. The bottle is clearly marked for the proper fill. Unscrew the bottle from the pump, holding the bottle upright so as not to spill.
-
Carefully screw the lid on the bottle without removing from the plastic bag. Remove the sampling tube from the pump. Place the pump in a sealed plastic bag between samples.
-
Keep the sample in the bag until you are back in a clean environment. Remove from the bag and clean the bottle. Label the bottle cap to match the bag from which it was removed.
-
Place the correct label on the bottle, stating the equipment number, machine, date, hours since the last sample and the lubricant.
-
Place the sample in a clean plastic bag. Place the proper MSDS label in the bag and seal.
-
Place the sample in a box. As many samples as needed can be placed in a box. Assure each one is in a sealed plastic bag with a matching MSDS label.
-
Seal the box with tape and affix a mailing label. Send the sample to Energizer's internal lab in Westlake, Ohio.
-
Make sure to send a cover letter to the Westlake lab that informs it of the number of samples and the required analysis (or analyses) to be performed.
"If we took oil samples in a half-hearted manner, those are the kind of results we would get back," says Staley.
Communication and training are crucial to ensuring that standards are followed and that everyone understands the value that proactive maintenance brings to the plant and the company. The Maryville maintenance department does this about as well as any in the U.S.
An example is with what the site calls "training modules". These are mobile, hands-on instructional units that allow mechanics and operators the chance to increase skills and practice correct methods before using them on the floor. There are modules for lockout/tagout, fasteners ... and for effective lubrication.
The lubrication module was built 2.5 years ago by a seven-member team. Encompassing the two shelves of a wheeled cart and an attached pegboard, it lets users see, feel, touch and hear what constitutes good lubrication and bad lubrication.
It includes elements such as:
-
proper safety measures before initiating lube-related PM tasks;
-
10 bottles of oil, which display the proper color codes and safety markings, and the corresponding colored and stamped tags found on machinery;
-
sampling bottles showing the difference between clean oil and dirty oil;
-
samples of grease zerks and fittings, which are color-coded to greasing frequencies (white equals weekly, red equals every 350 hours, etc.)
-
examples of under-greased, over-greased and correctly greased bearings;
-
exercises to correctly fill and use a grease gun, to brush-lubricate roller chain, and to set and monitor airline lubricators; and,
-
appropriate sorbents and their usage.
The module is incorporated in a four-hour lubrication course given to maintenance personnel and a two-hour course given to operators as part of the plant's autonomous care program. (It also can be wheeled to the floor for focused or refresher instruction.) A staff-developed 72-page book accompanies the training and outlines the lubrication mission, strategies, definitions, lessons learned and task-based game plans.
Maintenance mechanic Mark DeMott documents the date of an oil change and rebuild with a paint pencil.
"Noria played a big part in what we did," says Harris. "Rick and I, as well as senior operations supervisor Tom Odendaal, each have taken several courses. We took all of that information, as well as information from additional sources, and developed the training courses."
The maintenance organization is big on taking information and spreading it to the masses.
Staley creates a monthly newsletter on the impact of lubrication excellence/oil analysis and other PdM tools (ultrasonics, infrared thermography and vibration analysis) on overall plant reliability. It includes the number of budding issues uncovered during the month for each technology, synopses of completed projects, a listing of cost savings or avoidances, notes on upcoming projects and other news. The September issue showcased 14 photos of key stakeholders holding the Gill Award.
The newsletter, as well a "PdM Tip of the Day", is e-mailed to plant and corporate leaders (vice president of global operations Joe Tisone is a fan) and posted on the huge PdM board located along a main hallway in the plant.
The board also displays a flowchart of PdM activities, cost savings goals and achievements, and a host of charts and graphs related to metrics such as PM completion (98 percent for the year) and planned maintenance as a percentage of overall work (62 percent).
"Trending is one of the big things that we have found to be important, not only for oil analysis and predictive maintenance, but for everything we do," says Harris. "You know where it was. You know what direction it is going. It makes it very easy to present the situation - the problem occurring or developing. The changes and improvements that we undertake are based on solid facts. There is no guesswork."
Adds Kovar: "Our goal from the start was to let the facts speak for themselves. Use the high-quality equipment and procedures that we have to produce reliable information from which we can then take prudent actions."
Liken it to a physician who uses office and laboratory tools along with corresponding data to determine the health status and treatment needs of a patient.
Facts and FiguresHere are some of the facts:
By covering 98 percent of plant equipment with lubrication improvements and 22 percent with oil analysis, the plant has reduced lubricant usage and saved the company money. Staley provides one of his favorite examples - air compressors.
"In the past, we changed the oil on an annual basis. Two years ago, we installed filtration systems. Now we let oil analysis tell us when to change the lubricant," he says. "We have eight air compressors. Each one has an identical filtration system on it. It pumps out of the reservoir bottom and back into the top. It filters the oil continually. If we need to change the filter, we turn it off, but the compressor still runs. We filter the oil down to 1 micron. We let our trends tell us when to change the oil. We don't do it unless it actually needs it according to the oil analysis. We're getting at least two years now on the life of the oil. In fact, we aren't sure how long it can go because it has been two years and we haven't changed the oil yet. It's as clean as the baseline that we take annually."
The air compressor filtration systems saved Energizer more than $10,000 in the first year alone.
Machinery is running better with fewer breakdowns, leading to increased productivity.
"Our plant is running better than ever," says Kovar. "With the economy the way it is, it has been tight, just like with any manufacturing company. We did a good job of managing our maintenance dollars. Even with that scenario, we're seeing fewer failures on the floor. Operators see that and remark, 'You know what? We're doing the right things from a maintenance standpoint, from a PM standpoint, from a lubrication standpoint.' Eyes are opened more and more because the results are out there. You can see it."
'Best in Class' Has a Ring to ItEnergizer is becoming synonymous with lubrication excellence. Employees at the Maryville, Mo., plant know it. Leaders at the corporate offices in St. Louis know it. ICML Gill Award selection committee members know it. And now, the rest of the industrial world knows.
"We've received some calls and questions from other facilities up to now about our lubrication practices," says Kovar. "I'm thinking that when this article hits, the phone is really going to be ringing."
Ohio Lab is Base of Energizer's Oil Analysis Work
Rick Staley, one of the maintenance professionals who helped Energizer's plant in Maryville, Mo., win ICML's Augustus H. Gill Award recently, is no stranger to competition and accolades.
"You have to give it all you have," he says. "You have to give heart, soul, everything. You have to focus. You have to train. The same way you train your beagles to be the best they can be is the same way I train to be the best I can be at lubrication. I wouldn't be satisfied saying that 'I do lubrication' unless I was qualified to say so. I have Noria training. I've had Oil Analysis Level I and II. I've also had Machinery Lubrication Level I training. I feel like I've earned it, the same way with my dogs.
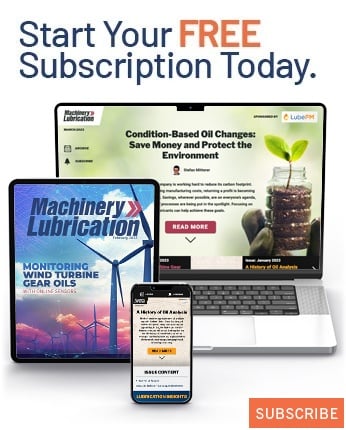