Since the discovery of their excellent anti-wear and fire resistance properties in the 1940s, the use of phosphate esters by industry has steadily increased.
Phosphate esters are used primarily as fire-resistant basestocks in several applications including hydraulic systems, turbines and compressors. The first commercial products were synthesized from coal-tar derivatives and were consequently composed of a mixture of various isomeric aryl phosphates, including the neurotoxic orthotolyl phosphate.

Phosphate Ester Characteristics
Today, other raw materials are used for the synthesis of phosphate esters. Modern technology affects better control of the manufacturing process, and the toxicity of the final product is normally low.
Fire-Resistant Fluid
Phosphate esters are the most fire resistant of the non-aqueous synthetic basestocks in common use. Their high ignition temperatures, excellent oxidation stability and very low vapor pressures make them difficult to burn, while their low heats of combustion result in self-extinguishing fluids.
Numerous organic phosphorus compounds including phosphites, phosphonates and phosphates have found application as additives in a variety of lubricant formulations as stabilizers, anti-wear additives, antioxidants, metal passivators and extreme-pressure additives.
Of these, zinc dialkyl dithiophosphates (ZDDP), found in virtually all automotive engine lubricants, are the most widely used. Only one group of phosphates, the tri-substituted natural esters of H3PO4, has found significant use as a synthetic basestock.
The use of phosphate ester-based products in hydraulic applications is still principally dictated by fire-risk considerations. Although inhibited phosphate esters possess excellent oxidation stability and inherently good anti-wear properties under critical loading conditions, they suffer from somewhat inferior hydrolytic stability, low viscosity index and extreme chemical aggressiveness toward many conventional seal and coating materials. These weaknesses limit the use of phosphate ester to specialized applications where a high degree of fire resistance is required.
Maintenance of a Phosphate Ester System
The user of fire-resistant fluids must accept the need for greater vigilance with respect to fluid maintenance than is normal for conventional mineral fluids. No longer is it sufficient to periodically change filters, repair the occasional leak and top off the reservoir. On average, phosphate esters cost five times more than their mineral counterparts.
The majority of fire-resistant fluids display a considerably greater degree of detergency than mineral fluids. Consequently, dirt particles or wear debris do not settle out in the sump as readily. This tendency promotes abrasive wear of pumps and other components along with affecting valve function.
Strengths
- Excellent fire resistance
- Good thermal stability
- Pour point ranges from -25 to -5 °C (-13° to -137.2 °F)
- Excellent boundary lubrication properties
Weaknesses
- Very low viscosity index ranging from 60 to -30
- Degradation products are phosphate soaps; black sludge-like consistency
- Risk of hydrolysis
Applications
- Fire-resistant industrial hydraulic fluids
- Aviation hydraulic fluids (trialkyl or tributyl) (synthetic)
- Electrohydraulic control fluids for steam turbines (EHC) - triaryl phosphate (natural)
References
Rudnick, L.R. "Synthetics, Mineral Oils and Bio-Based Lubricants: Chemistry and Technology", Taylor & Francis Group, New York, 2006
Hodges, P. "Hydraulic Fluids", Arnold, London, 1996
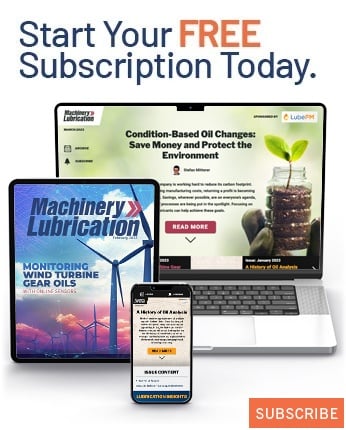