The combination of oil analysis and effectively deployed lubrication management and machine maintenance has enabled the reliability team at Northampton Generating to deliver real benefit to the organization. By identifying problem areas and dealing directly with the issues, machine reliability is on the rise and maintenance costs are reduced.
The Northampton Generating Plant, located in northern Pennsylvania, is a 110-megawatt co-generation facility that has been providing electricity to GPU Energy since August 1995. In addition to providing enough electricity for 110,000 homes, the plant processes steam for use in Ponderosa Fibres of America’s recycled liner-board mill. The Northampton Generating Plant fires “culm”, the waste by-product of mining anthracite coal. Approximately 545,000 tons of culm are burned each year in circulating fluidized-bed boilers, an advanced technology for burning waste coal cleanly. With cost-control pressures of deregulation looming, co-generation stations like Northampton place a premium on machine reliability to maintain high plant availability. This maximizes the revenue from the sale of electricity while also providing a dependable process steam source for Ponderosa Fibres.
Figure 1. Annual Costs to Lubricate Machinery, Mineral Oils vs. Synthetic Oils
When the generating plant came online, all of the equipment initially was filled with mineral-based lubricants. As a proactive measure, all mineral products were replaced with synthetic products at the first scheduled change interval. The decision to use synthetics was driven by management’s desire to ensure equipment reliability and to reduce lubrication manpower requirements. Given the plant’s northern location and the fact that most of the equipment is located outdoors, mineral oil requires seasonal changes to adjust for viscosity requirements. Due to improved cold-weather performance and high viscosity index, synthetic oils need not be changed seasonally, thus reducing lubricant consumption and labor simultaneously. To further reduce costs and ensure reliability, oil analysis was employed to guide oil change decisions and to alert the team of any abnormal lubricant or machine conditions.
Initially, the use of synthetic lubricants and the elimination of scheduled and seasonal oil changes met with some skepticism. Through a series of educational meetings, the decision to use synthetic lubricants was accepted, but with a “we’ll see” attitude. From the start, Northampton’s maintenance philosophy emphasized predictive and proactive efforts over reactive methods. The use of synthetic lubricants combined with oil analysis fit well with this philosophy.
Cost justification for the change to synthetics and condition-based changes came quickly. The increased cost of both synthetic lubricants and oil analysis were offset by reduced labor associated with scheduled and seasonal changes and the reduction in inventory required to stock warm- and cold-weather lubricants. Figure 1 details the annual costs to lubricate the machinery with conventional mineral oils vs. synthetic products. The plant-wide annual savings totaled $20,668 in avoided lubrication costs alone. Moreover, management’s objective of maximized machine availability was accomplished due to the success of the oil analysis program. And, condition-based oil changes and extended intervals align well with Northampton’s desire to minimize environmental impact.
Contamination Control Was a Major Focus
Northampton’s contamination control efforts have been aggressive. Recognizing contamination as a primary root cause of machine failure, the gearbox vents were refit with breathers that restrict the ingestion of airborne dirt and debris. In the highly contaminated coal processing plant, gearboxes average ISO 19/14 after the change, compared to a more typical 23/20 level for these systems. The reduced strain on the bearings in these gearboxes due to this cleanliness improvement reduces wear by an estimated 50 percent, according to research. That life extension puts money on the bottom line in the form of avoided maintenance costs and increased reliability and availability.
Efforts to control contamination also have been expanded to lubricant storage. Lubricants are inventoried in a clean, controlled environment. All drums and containers are clearly marked, and a readily available log identifies precisely what machines receive what products. These combined efforts have yielded very low ISO codes and correspondingly low levels of elemental silicon when new oils are tested for quality.
With reliability goals dependent on oil analysis and oil cleanliness, sample quality was critical. To ensure sample quality and consistency, sample ports were installed and specific sampling procedures have been implemented to ensure consistency. The sampling ports were installed at a central location, between the drain and fill plug. When sampling, pathways were aggressively flushed, disposable sampling supplies were used only once, and precautions were taken to not introduce airborne particles and debris into the sample container as it was being drawn. In every case, the sample was taken when the equipment was running.
Oil analysis has proved to be a very effective tool for assuring the reliability of equipment at Northampton. The plant implemented vibration analysis and oil analysis simultaneously. They have proved to be an effective combination in the pursuit of management’s reliability goals. For gearboxes, oil analysis has been deemed the best early indicator of problems. Presently, vibration analysis is used only on exception to aid in diagnostics. Oil analysis also has assured effective lubrication of critical systems.
Figure 2. Northampton’s efforts to control contamination carried over to lubrication storage and dispensing.
Oil Analysis Used to Find Issue with Cooling Tower Gearboxes
One particular situation where oil analysis proved vital is the cooling tower gearboxes. These gearboxes are critical to the operation. The loss of just one leads to production losses. Moreover, they are inaccessible between annual outages. At the early stages of the new high-quality oil analysis program, it became apparent that the gearboxes had been ailing, as evidenced by high acid numbers (ANs) and rising iron levels. Accordingly, the oil was quickly changed back to a mineral product. The result of this action was disappointing. AN and iron levels began to rise even faster than before. The team had failed to find and address the problem’s root.
Abandoning casual reactions, the team addressed the situation systematically to uncover the following facts:
-
The gearboxes run in a tough environment rich with moisture, heat, air and catalytic iron – all of which promote oxidation.
-
The drain intervals had been extended.
-
The employment of high-quality oil analysis was just under way. It is common to discover “new” problems that had merely not been uncovered previously.
-
The oil change was performed without a flush, leaving residual oxidized oil that acts like a “cancer”, quickly depleting oxidation inhibitors and eventually attacking healthy base oil molecules.
-
The gearbox was drained.
-
The system was flushed to remove the residual oxidized oil.
-
A refill with synthetic oil was implemented.
-
Oil analysis was standardized to ensure the reliability of these critical systems.
With these facts in hand, the lubrication management team took the following steps to rectify the situation:
-
The gearbox was drained.
-
The system was flushed to remove the residual oxidized oil.
-
A refill with synthetic oil was implemented.
-
Oil analysis was standardized to ensure the reliability of these critical systems.
Since taking these measures, AN and iron levels have returned to normal. However, the lube team knows that when a machine is critical and operates in a challenging environment, you can’t get too comfortable and rest in the light of past successes. Instead, oil analysis must be used in an ongoing manner to ensure that the cooling tower gearboxes remain well lubricated and in fit condition.
A proactive approach from the start has proved very beneficial at Northampton. By combining advanced maintenance practices, including oil analysis, along with the employment of synthetics and proper lubricant handling and management, Northampton Generating is realizing management’s reliability and availability goals. The successful program has been expanded to the fuel site, where improved reliability was seen in the program’s first six months.
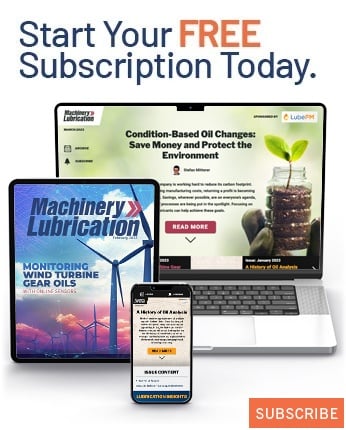