Don't Clean Those Failed Bearings
Rolling element bearings fail prematurely in service for a number of reasons. Most bearing manufacturers offer a free service to establish the reasons for failure of their products.
If a bearing is returned to a particular manufacturer, it is extremely important that the bearing not be washed or cleaned prior to removal and subsequent return.
Valuable evidence which may give a clue to the cause of failure may be destroyed, and perhaps render the analysis impossible. Contributed by Derek Peasley, FAG Bearings Europe
Lube Storage Tip
If your lubricant supplier is reusing drums, ask him to provide documentation showing that the drums have been reconditioned, including chemicals, method used and cleanliness rating. If the supplier cannot provide a reconditioning service, then consider specifying that all products be sent in new drums.
Hints for Grease Application
1. When converting from one grease to another, confirm compatibility among base oils, additives and thickeners. At the very least, conduct a Worked Penetration test to identify changes in consistency at various mixed concentrations.
2. Greases manufactured with severely hydroprocessed (Group II) and hydrocracked (Group III) base stocks may be a suitable alternative to synthetics, such as PAOs and esters, for hot applications. Some of these lubricants are capable of delivering very similar performance and life at a reduced cost per pound.
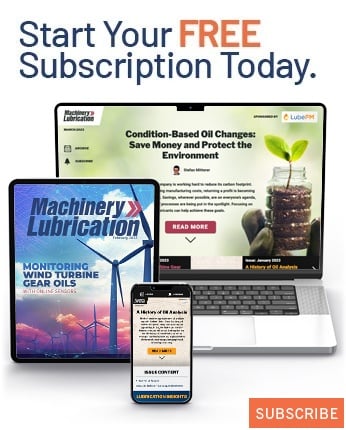