Brand consolidation does not ensure that the products used are right for the job. Lubrication is a fundamental design property, and the machine designer makes certain assumptions and design decisions based on the lubricant to be used. To ensure that lubrication is optimized, or that all equipment has the proper type and amount of lubricant specified, we must take the investigation to the equipment and component level.
Equipment Requirements
This involves a process of reviewing the population of lubricated equipment in the facility, including identifying make and model information (vendor specifications should be obtained if possible). As the list of lubricated machinery is compiled, it is helpful to key it into a database.
Use of a versatile program such as Microsoft® Access or Excel allows flexibility in the design and output of the database. Fields should be established for equipment ID, reservoir ID (for multiple sump equipment), manufacturer, model number and current lubricant. For equipment that is assembled from separate manufacturer components (such as a Roots blower driven by a Siemens motor) and provided with separate vendor manuals, treat them as separate database entries. Other fields in the database are used to identify the key physical/chemical properties and performance characteristics. Figure 1 shows how a database is assembled for compiling the equipment-specific lubrication data.
Not all facilities have effectively cataloged equipment vendor manuals, so extra work may be required to obtain the lubrication design data from the OEM. Using an outside service provider may be advantageous because it may already have a catalog of equipment lubrication design data from previous consolidation efforts. The technical consolidation can be achieved by using the tables to find an overlap between available products and equipment requirements.
Making the Blueprint - Generic Specifications
Purchasing Power
The most significant gains can be made once the lubrication requirements have been determined and reduced to generic lubricant purchase specifications. These specifications are helpful in creating purchasing power for the buyer, enabling him/her to negotiate the best deal for those products whose characteristics and performance meet or exceed the minimum standards outlined in the specs.
This also provides the flexibility of using multiple suppliers, or changing particular suppliers from time to time as product prices, quality or availability vary. Of course, one must be careful of compatibility issues when changing suppliers and products.
Mechanics of Generic Specifications
A list of lubricant application types can be developed using the tables or databases based on equipment lubricant requirements, operating conditions and environmental conditions. Examples include EP gear oil turbine oil, AW hydraulic oil, worm gear oil, and hi-temp grease. The viscosity grades can be identified within each of the applications to address the machine requirements.
The process generally proceeds by choosing a common product type from the group of required products and creating generic specifications for those types. Before creating new specifications, review the existing set of specs to see if any meet the requirements of the next machine. In those cases where the difference in requirements is minor, consider expanding an existing spec to include this next equipment as well, perhaps by going to a multipurpose lubricant or taking advantage of the properties of some superior performance product types (such as synthetics).
As generic specifications are assigned to the database, the components previously associated with that type of product will be matched up and dropped out of the population requiring specifications.
Wherever possible, reference published standards such as American Society of Testing and Materials (ASTM), American Gear Manufacturers Association (AGMA), American Petroleum Institute (API), and the International Standards Organization (ISO) when developing the chemical/physical and performance specifications. A simple, standard format presents the acceptable test result limits and a discussion of general application usage and lubricant properties. Figures 2 and 3 show the front and back of a typical generic lube spec.
The goal is to determine the minimum number of unique lube application types and establish ones that will address all equipment needs within the plant. The specification must be generic enough to drive competitive bids for products by product type. However, do not overlook any critical performance characteristics of the lubricants. There is such a thing as over-consolidation, where too much focus is placed on limiting the number of different products stocked, at the expense of compromised lubricant performance. In some cases, one lubricant-induced equipment failure event can wipe out all of the potential monetary savings from consolidation and generating bid specifications.
Using the Database for Continuous Improvement
Consolidation is not complete until procedures and processes are in place to control and update the inventory of lubricants and to assign lubes to specific equipment. The most efficient way to accomplish this is to produce a database to serve as a living document for lubricant inventory and application. The construction of the database is not a large amount of additional work because the information for brand and technical consolidations has already been generated.
The database can serve as an ultimate reference source for equipment lubricant requirements, and can even be integrated with an electronic lubrication manual to provide the single source for equipment-specific lubricant information for the facility.
Making the database accessible to the company intranet makes the utilization of lubricants at different sites more efficient. The start screen provides selections for each of the individual plants, to allow the user to narrow his information search to a particular facility. Also, reports can be generated that query from the larger database and allow information to be extracted from across the sites. Once the site has been selected, options include editing and recording data. The Add/Edit function can be limited to authorized personnel only, to minimize the occurrence of data corruption. Various reports can be generated, or customized queries can be made based on the information desired by the user.
Data entry mode screens allow the user to enter new or modify existing records to reflect changes (Figure 3). These changes could include the addition of new equipment, a replacement part from a different component that requires a different lubricant, or feedback from proactive maintenance investigations that result in design changes to the equipment lubrication.
This type of data manager resource tracks the development of the optimized lubrication configuration for the facility and provides a functional database which can be used to support a dynamic living program - incorporating feedback from operational and maintenance experiences and the changes in lubrication which they prompt. Facility improvements can also be expanded on a corporate-wide level. The single greatest pitfall to the successful implementation of a lubrication consolidation is a lack of program control after the original project is complete. Adopting a living program through the creation and maintenance of a database, and the development of policies and procedures that define responsibilities for program improvement, enable an environment of continued lubrication excellence.
Planning and Execution Generate Real Benefits
A carefully planned approach to lubricant consolidation can translate into big benefits. The keys to success are identifying all lubricants in use, using equipment lubricant requirements to create generic specifications, and adopting an environment of continuous improvement through the use of a current and updateable database. A multiphase approach allows a facility to see real benefits after a minimal investment, and allows sufficient support to be generated to sustain the effort. As the program grows, multiple facilities within a given company can be brought together to share data and leverage lubricant buying power.
While such programs can be successful while using services provided by a lubricant supplier or internal company resources, the greatest potential for accurate and efficient consolidation lies in partnering with an experienced and independent organization that can evaluate lubricants and lubrication requirements in an unbiased manner. Using existing database resources from commercial lubricant properties, equipment lubrication requirements, and lubricant equivalency tables facilitates a low cost, precision application and optimized lubrication program.
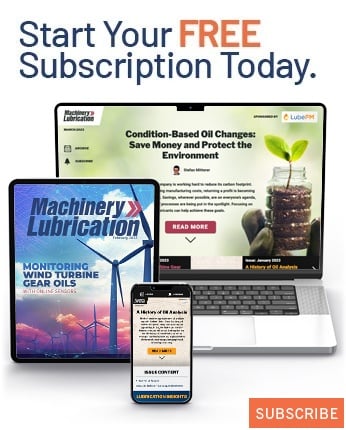