For some companies inadvertent or unintentional mixing of fluids and oils is a frequently encountered problem. Under these circumstances, mixing may be the result of improper markings on containers, similarity in product description titles, lack of information given to operators, or just carelessness of those performing the maintenance. Whatever the reason, corrective action should be taken to try to minimize, and if possible eliminate such occurrences.
Fluids and oils that are either designed to be mixed, or may be mixed with no harmful effects are often referred to as compatible. Those that cannot be mixed without potential problems are termed incompatible. The degree of incompatibility can vary from complete to slight incompatibility, depending on the seriousness of the incompatibility to fluid integrity and system performance requirements.
For example, mixing lubricants that have widely different base stocks such as a fire-resistant phosphate ester-type fluid with a petroleum-based fluid would represent both a system incompatibility as well as a fluid incompatibility and is serious cause for concern. On the other hand, oils that are designed for the same application, but when mixed result in some separation or reaction of the additive ingredients without significant deterioration of performance, would be considered only slightly incompatible.
Clearly, mixing a phosphate ester with a petroleum-based fluid would result in reduced fire resistance. If the application called for such a fluid, it may also result in severe damage to the machinery, because the lubricant is designed to be compatible not only with the internal machine metallurgy but also with other components such as seals, gaskets, etc.
The two products will also have significantly different physical and chemical properties and are unlikely to perform identically under operating conditions. The mixing of different fluids is clearly a cause for immediate concern.
In the second instance, where two products designed for the same application have been mixed, problems with incompatibility would develop over time. Several factors will influence the speed at which problems develop including:
1. The nature of the incompatibility itself (such as, additive incompatibility, base stock reaction, etc.).
2. The type of operation/service involved.
3. The presence of other contaminants that could aggravate the situation.
4. The relative proportions of the two fluids.
Very often, the mixing of different fluids results in a loss of solubility and/or the responsiveness of the additive ingredients used in either of the two formulations. This can result in a diminished effectiveness of the additives to perform as intended.
It was recently reported that although it is generally safe to mix lubricants of different types designed for the same application, the drawbacks of mixing are far greater for complex formulations.1 For example; an automotive engine oil may contain 20 percent additives or more whereas a hydraulic fluid may contain only a small percentage of rust and oxidation inhibitors. Given the more complex nature of the engine oils, there is a greater likelihood that problems can occur with mixing this type of lubricant.
The Military Experience
The U.S. Department of Defense maintains numerous types of vehicles, equipment and other systems that all require the use of fluids and lubricants. Not only is the wide range of mechanical systems difficult from an operational and maintenance standpoint, but the manner in which the Department of Defense procures its lubricants and fluids that are needed precludes the purchasing of specific products from the same source or sources, a strategy which would likely minimize the potential for any incompatibility problems.
To counter some of the problems mentioned above (other than the inadvertent mixing of improper fluids/oil for which there is no control other than proper training and procedures), individual military specifications (now referred to as performance or detailed specifications or commercial item descriptions) include requirements for assuring compatibility of like or similar fluids/oils.
Some of these requirements involve mixing different fluids and subjecting them to heating up to 275°F (135°C) for two or more hours, followed by cooling down to -65°F (-54°C) for an additional two or more hours. Visual separation to any degree is considered evidence of an incompatibility and ground for rejection of the fluid. These requirements can be found in military specifications for most fluids, including hydraulic fluids, general preservative oils, automotive engine and gear oils, and aviation engine and gear oils.
Available Procedures For Assessing Compatibility
Many of the procedures for determining fluid or lubricating oil compatibility are available and published in the Federal Standard 791C titled “Lubricants, Liquid Fuels, and Related Products; Methods of Testing.”2 Three such procedures in this Federal Standard are worthy of mention.
1. The first is Method 3470.1 titled “Homogeneity and Miscibility of Oils.” This test involves individually mixing a candidate oil or fluid with six other reference oils. These mixtures are then subjected to a series of heating and cooling cycles with most of the emphasis given to the cooling cycles because incompatibility becomes more pronounced at lower temperatures, as was evidenced in a recent SAE paper titled “Assessment of the Low-Temperature Incompatibility Risk of Commercial Engine Oils.”3 After repetitive heating and cooling cycles, any evidence of adverse reaction or separation such as a color change, the appearance of particles, individual layer formation, etc., constitutes an incompatibility.
2. The second is Method 3430.2 titled “Compatibility Characteristics of Universal Gear Lubricants.” This method also involves mixing candidate oils with reference oils. The test consists of heating the mixture to 250°F (121°C) for 20 minutes, storing for 30 days at room temperature, and then centrifuging to determine the percentage of separated material.
3. The third is Method 3440.1 titled “Storage Stability Characteristics of Universal Gear Lubricants” which, unlike the other two methods, does not involve mixing the candidate oil with any reference oils. The test assesses the compatibility of the lubricant with extreme temperature storage conditions. The candidate oil is heated to 248°F (120°C) for 20 minutes, then after cooling, the oil is stored in a dark area at room temperature for 30 days. After this period, the oil is centrifuged to see whether any separation occurred.
Adoption of Test Methods for General Industry Use
These test procedures have become widely used within industry and have since been incorporated into several industry standards. For instance, Method 3470.1, commonly referred to as the “H & M Test,” is required for automotive engine oils meeting the SAE J183 JUN99 Engine Oil Performance and Engine Service Classification (other than energy conserving) standard.4
Methods 3430.2 and 3440.1 are required for automotive gear oils meeting the SAE J308 JAN96 Axle and Manual Transmission Lubricants Information Report.4 More than likely, these procedures are used by many other industry and user organizations. Although they were primarily designed for automotive lubricating oils, they certainly could be adapted or modified for use with oils and fluids intended for other types of equipment and machinery systems.
Further Reading
Shugarman, A. (2001), “Managing the Risk of Mixing Lubricating Oils.” Machinery Lubrication magazine (www.machinerylubrication.com), September - October 2001.
References
1. Denis, J., Briant, J. and Hipeaux, J. (2000). “Lubricant Properties Analysis and Testing.” Editions Technip Paris, p. 281.
2. Lubricants, Liquid Fuels, and Related Products; Methods of Testing. Federal Standard 791 Revision C, Document Automation and Production Service. Philadelphia, PA. (1986).
3. Rhodes, R. (1994). “Assessment of the Low-temperature Incompatibility Risk of Commercial Engine Oils.” SAE Paper 941976, SAE International Fall Fuels and Lubricants Meeting.
4. SAE Fuels and Lubricants Standards Manual, 2001 Edition. SAE HS-23, Society of Automotive Engineers, Inc. Warrendale, PA.
5. Federal Test Methods, Document Automation and Production Service, Bldg 4/D, 700 Robins Avenue, Philadelphia, PA.
6. SAE, 400 Commenwealth Dr., Warrendale, PA.
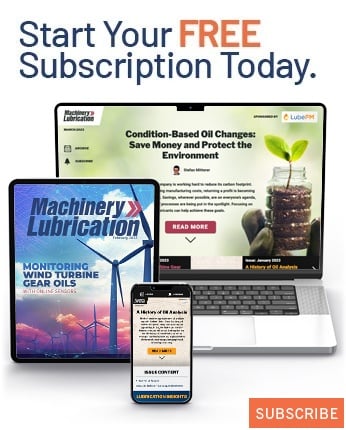