
For a complete and proper lubrication program to work effectively and provide the most return on investment, the entire gamut of lubrication must be considered, ranging from receiving to application.
Through this gamut there are missed opportunities to increase equipment productivity and reliability and to maximize the returns of investing in a professionally designed lubrication program. One of the biggest and most costly missed opportunities is proper lubricant storage and handling.
Many facilities are unaware of the danger improper lubricant storage and handling practices create and what inevitable fate it can lead to in terms of equipment reliability and lifecycles. Proper lubrication is not only about the right amount-at the right time-at the right place, it is also about keeping lubricants clean, cool and properly identified.
Here are some tips to help outline the best practices for proper lubrication storage and handling:
1. Lube Room Design and Requirements
A properly designed lube room must be functional, safe and expandable, and provide all necessary storage and handling requirements for the facility. Lube room designs should allow the maximum storage capacity without allowing for too much bulk oil and grease storage. Limiting the amount of bulk oil and grease storage will allow the oils that are stored to be used in a timely manner.
Some key features to consider are a limited access door, which will allow for logging of who and when a lube technician enters and leaves the room; visible landing area for new lubricants; log all new lubricant deliveries; make filtration of stored lubricants easy; provide proper safety devices; designate enough floor space for fire proof storage cabinets to store top-up containers, grease guns, etc.; and include a desk and computer to track inventory, sampling, filtration, receiving, etc. It also is a smart idea to have a separate storage area to store bulk totes, drums, buckets, etc.
2. Bulk Oil Storage
The first area of a lubricant storage and handling system that requires attention is bulk storage. Whether storing lubricants in a 10,000-gallon tank or 55-gallon drums, it is very important to ensure the lubricants’ quality is not tainted by contamination or additive settling. To help ensure lubricants stay in an optimal condition, one must determine how much lubricant should be stored at one time.
To aid in this process, certain steps can be employed, such as:
-
Determine lubricant consumption rate. Consumption will vary greatly depending on industry and equipment type. To ensure the right quantities of lubricants are being stored at a facility, the consumption rate must be determined. There are many factors that contribute to consumption, ranging from leaks to excessive drain and fills.
-
Determine lubricant storage capacity. The required lubricant storage capacity depends on consumption, but often there are too little or too many lubricants stored at one time. The proper storage capacity should maximize shelf life but allow for a certain percent excess of critical lubricants to be stored for emergency situations.
-
Determine lubricant supplier turnaround time. A lubricant supplier’s turnaround time should be a metric used to aid in determining the quantity of lubricants stored. If there is a short time interval between deliveries, fewer lubricants can be stored onsite, but if there is a lengthy time interval between deliveries, the quantity of lubricants stored onsite should account for this.
Once the consumption rate and storage capacity have been determined, one should decide what type of storage containers will be used. The correct size storage container is a direct reflection of the consumption rate and storage capacity. If a large consumption rate is determined, a large bulk storage tank may yield the best results, but if a low consumption rate is determined, a rack mounted storage system or 55-gallon drums may yield the best results.
For smaller facilities that have a small consumption rate, the use of drum storage may be the best option.
3. New Oil Receiving
Oftentimes, improper receiving techniques do nothing but promote higher risks of contamination ingression, mixing of lubricants, etc. Proper written receiving procedures should be in place to ensure the highest level of consistency and cleanliness is maintained.
Proper receiving techniques should include filtration of incoming oils. Many times new oils may be dirtier than your defined particle target cleanliness level. Meaning, if you define your particle target cleanliness level and spend time, money, manpower, etc., to achieve these levels of in-service lubricant cleanliness, the last thing you want to do is contaminate it with “dirty” new oils.
4. Quality Control
Quality control of lubricants delivered from lube suppliers must be verified to ensure the correct product is being delivered and that the cleanliness of the delivered lubricant are up to current target particle and moisture cleanliness levels.
To help ensure your lubricants are meeting their standards, the use of oil analysis is a powerful tool and will reveal the following:
- Quality of base stocks
- Additive quality and concentration
- Lubricant performance properties
- Thickener performance properties (grease)
Take a look at Why and How to Test New Oil Deliveries for more information.
Common ways oil can become contaminated
5. Presence of Mixed or Contaminated Lubricants
Oil analysis results and other quality assurance variables, such as damaged containers, rusted containers and any other quality issue, should be well documented and cataloged.
Items to note in the documentation phase are:
- Delivery date and date of oil sample taken
- Inspection results of storage containers
- Labels depicting results of oil analysis test
- Itemized checklist for sampling test
- Periodic decontamination with filtration
Whichever storage container is chosen, it is best to filter the new oil while filling the storage container. Doing so will reduce the amount of contamination that is delivered with the new oil, but periodic filtration and agitation should be performed to maintain certain ISO cleanliness levels and prevent additive settling.
Periodic filtration is a good practice to ensure clean, fresh oil will be used to perform top-ups and drain and fills. There are two primary methods for filtration of bulk stored oils: hard plumbed filtration system or filter cart. The hard plumbed filtration system works best in conjunction with a rack mounted system.
Each container should be fitted with a breather, sight glass, filter, lubricant label, quick connect fittings and dedicated dispensing line. This system will help ensure the lubricants are at optimal condition when they are needed and the right product for the application is dispensed.
Periodic filtration for drum storage also is easy with the use of a filter cart once the drums are equipped with quick couplers. No matter how large or small the storage container, periodic decontamination should be a priority to maintain the quality of the stored lubricant.
6. Dispensing Options for Stored Oils
When stored oil is transferred from the bulk storage system to the top-up container, it is best to filter the dispensing oil. This can be made very easy with the use of a hard plumbed filtration system and a rack mounted storage system fitted with dedicated dispensing nozzles. If using 55-gallon drums, they can be fitted with quick connect fittings, a hand pump, an inline filter manifold breather and sight glass to achieve the same goal.
Improper dispensing of new oils into top-up containers is a primary cause of self-induced contamination. Proper techniques and tools must be used to ensure your new, filtered oil is transferred to the top-up container with minimal exposure to atmospheric conditions. Not using proper techniques here could be a waste of time to the filtration efforts, storage and in-service lubrication cleanliness.
7. Precision Top-Ups and Drain and Fills
Once the bulk storage system is properly set up, one should consider the method for transporting oil and filling machines. The best top-up method utilizes a proper top-up container, one that is sealed from the environment, has a built in spout, hand pump, etc.
OilSafe Color-Coded Transfer Containers
If short cuts are taken at this stage, all of the time and effort spent building and designing the bulk storage system and ensuring the quality of the bulk oil with filtration will have been wasted. Too many times oil is highly contaminated from the time it is dispensed into the top-up container to the time it is added to the machine.
Using washable and re-usable top-up containers allow for easy cleaning and maintenance. Typically, non-sealable top-up containers that are re-used introduce large amounts of containments to the system, which could counteract any effort of removing or excluding contaminants, and also can have a slight lubricant cross-contamination effect.
For top-ups of larger sump volumes, such as large gearboxes, circulating system reservoirs, etc., the use of filter carts is the preferred method for transferring the new oil from the storage container to the machine.
8. Proper Top-Up Container and Grease Gun Storage
Storage for top-up containers, grease guns, rags, etc., is another important step to ensure contaminants are not introduced to the lubricants as a result of poor housekeeping. These tools should have their own dedicated fire-proof storage cabinets for easy access and organization.
Grease storage is simpler than oil storage but also must not go overlooked. Open grease tubes and drums are magnets for attracting airborne contaminants such as lint and dust. Securing used grease tubes that will be re-used in sealable washable containers is considered the best practice. The containers will hold one tube of grease and allow for great contaminant exclusion. Used drums of grease are at an even higher risk of contamination.
These drums are often opened and used over a greater period of time, leading to more and more opportunities for contaminants to enter. If not using a sealed air style grease dispensing unit for drums of grease to fill grease guns, some of the best methods for contaminant exclusion are to use Velcro style covers or snap-on caps. Using these types of contaminant exclusion devices will keep the grease cleaner and prolong its life.
Grease guns should be stored in a clean, dry and controlled environment. They are precision tools that must be taken care of in order for them to provide the maximum degree of accuracy and reliability. Grease guns should be regularly cleaned and inspected for proper function and an annual calibration should be performed.
This calibration will ensure the same volume of grease is still being dispensed with one shot as when the gun was new. The best method for grease gun calibration is to use a postal scale to measure how much grease is dispensed with one pump.
9. Lifecycles and Lubricant Shelf Life
For both oil and grease, one should be aware of their respective shelf life. Exceeding their OEM shelf life may render the product useless or severely hamper its performance. For this reason it is best to use the First-In, First-Out (FIFO) method.
This method simply requires the maintenance professional to use the oldest lubricants that were put into the storage system first and the newest lubricants put into the storage system last. This will help ensure lubricants do not accidentally exceed their recommended shelf life.
As previously mentioned, OEM storage limits should be considered when storing greases and oils. Table 1 outlines maximum storage limits for different grease types and oils.
NLGI recommends the following steps for best practice of grease storage:
-
Store the grease in a cool, dry indoor area where airborne debris is at a minimum
-
Use the oldest container first
-
Keep containers tightly covered
-
Wipe off the edges of a container before opening it to avoid intrusion of dirt
-
Where necessary, grease should be brought to a satisfactory dispensing temperature just before being put into service
-
Clean grease-handling tools (such as spatulas, drum pumps, etc.)
-
When a container has been partially emptied and the remainder will not be immediately used, all void spaces within the remaining grease should be filled with grease, and the surface leveled and smoothed
-
Store grease cartridges (tubes) vertically with the removable cap up (ref. NLGI)
Table 1. Maximum Storage Limits
10. Labeling and Identification
Lubricant labeling is one aspect of storage and handling that is often overlooked. Labeling is just as critical as periodic filtration and without proper labeling it is very easy for lubricant cross contamination to occur. Lubricant cross contamination is a result of mixing two lubricants together and can yield a devastating result. This happens more often in the dispensing equipment rather than the bulk storage equipment.
OilSafe Labels enable identification of container contents through color-coding and the addition of extra information as required.
A labeling system can be a simple concept but could prove to be difficult to implement and maintain. Decide how to label each corresponding lubricant from bulk storage to the equipment it will be used in. It can be a color coded system, an alphanumeric code system that depicts important performance data about the lubricant, or a combination of both.
Any labeling system can efficiently ensure the right lubricant is used at the right location and prevent cross contamination, but in order to do this, the labeling system must be kept consistent and up to date with current lubricants that are in use and being stored.
For example, Noria’s LIS system is a technical recommendation that denotes a lubricant’s key performance properties and compiles them into an alpha-numeric code. Each performance property gets its own section of the alpha-numeric code. Once these alpha-numeric codes are determined, they can then be easily printed and incorporated in a labeling scheme. There are hundreds of possibilities for the alpha-numeric codes, so a system that is easy to read and maintain is preferred.
Matching stored lubricants to the machines in which they are used should be a primary focus of your labeling system. We must be able to correctly identify lubricants in storage and also correctly identify their applications in the field. Applying the labels to top-up containers, grease storage containers, totes, drums, etc., is the only way to ensure correct product delivery to application.
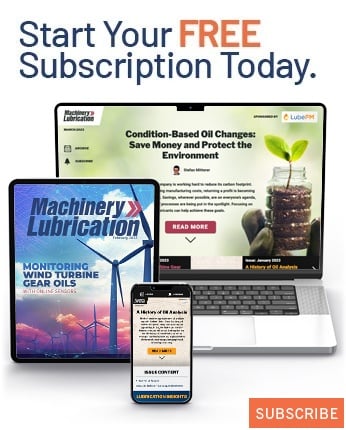