“What is the difference between total sulfur and active sulfur contents in extreme pressure additives? How does sulfur (both forms) increase extreme pressure (EP) characteristics?”
Sulfur is used in many EP oils and metal-working fluids as an EP additive. The basic way this works is for the sulfur to react at elevated temperatures, such as those experienced by meshing gears to form a sulfide layer.
For example, for steel gears, an iron sulfide layer forms on the gear tooth surface. This ductile layer improves sliding contact, preventing scuffing or galling.
There are two types of sulfur compounds used — active and inactive sulfur. The main difference is that for active additives, the sulfur-containing additive reacts with the surface at much lower temperatures, whereas inactive compounds react only at much higher temperatures.
While active additives have advantages of greater reactivity and hence may offer better anti-scuff protection, especially at lower temperatures, they are also mildly corrosive, particularly to yellow metals (brass, bronze, etc.), and should be avoided where these alloys are present.
The amount of active sulfur additive can be measured by first determining the total sulfur content using an appropriate ASTM test method, then reacting the active sulfur with copper powder and removing the copper sulfate by filtration, and again measuring the remaining total sulfur.
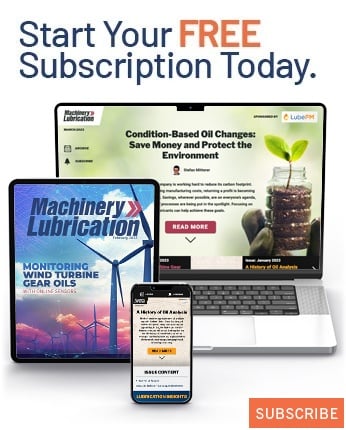