“We have a quarterly oil sampling program at our mill on many of our critical systems. We have installed sampling ports on our hydraulic and oil circulation systems but rarely see an advance warning of equipment problems. Consequently, we have unexpected failures on sampled systems. What can we do to improve our results?”
There are many factors that can influence the effectiveness of an oil analysis program, including test slate selection, alarm levels, laboratory quality, sample frequency, sample location and equipment operational factors, to name a few. Two common problems that programs encounter include poor test selection and poorly selected sample port locations.
While both of these can confuse the outcome and minimize the effectiveness of analysis, a properly selected sample location is vital for trending changing equipment condition. It is possible to assess lubricant and contamination conditions with samples taken from many locations in most reservoirs. However, sampling for evidence of mechanical problems requires a sample to be collected from a location that contains the highest concentration of “evidence” of a problem. The evidence, of course, is the wear metals.
Often samples are collected from a pressure line after a filter or from a drain line toward the bottom of a reservoir. This is generally because these locations allow for low-cost installation, easy access and low-cost sample collection. However, these common locations are far from ideal because the “evidence” may be filtered or settled out of the lubricant, leaving the program with little more than fluid properties information. Sample ports must be configured to enable collection of lubricant in close proximity to the mechanical components in question.
Everyone has heard how the top three factors influencing real-estate transactions are location, location and location. The same concept applies to oil analysis-based equipment condition-monitoring programs.
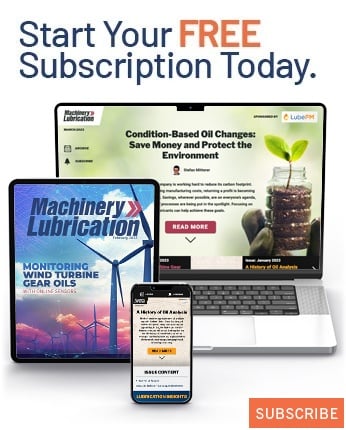