"I am wondering about our lubricator's practice of pumping oil into oven roll bearings periodically to refresh the grease? Is this a good practice?"
This is a rather uncommon practice, but it is a good question. The short answer is that this is not a good idea. As you probably know, grease is a product of dispersion of a thickening agent in a liquid lubricant. Over time while in service, grease separates or dries out. The oil eventually goes away, and the thickener is left behind.
Assuming your technicians are trying to replace the oil that has separated, this might be possible under certain conditions. However, you should replenish the grease rather than the oil.
There are two problems with this practice. The first problem is that it is not that easy to mix grease. You cannot simply pour oil onto the thickening agent to get grease. Most greases are formed by dissolving the thickener reagents in oil where they react to create the thickener plus byproducts in solution under controlled conditions (temperature and pressure).
Next, the byproducts are removed, and other additives and oil are added to give the desired consistency. Then the mixture is homogenized to provide consistent properties throughout the batch. As you can see, by just adding some "light" oil, you are probably just washing out some old grease.
The other problem could come from successfully mixing the oil with the grease. If the new oil did mix with the old grease, you could significantly alter the properties of the grease or even introduce incompatible components that could lead to a number of problems. You could change the consistency of the grease, affect the viscosity of the base oil, dilute additive concentration or create a number of chemical reactions between incompatible components, which can lead to additive neutralization, changes in lubricant chemistry and certainly impaired performance properties.
What you should do is make sure you are using the right grease for the application, use appropriate methods to determine the right amount of grease for replenishment and select the best relubrication frequency. These values will rely on the type of bearing, speed, bearing geometry and operating conditions (temperature, moisture, particle contamination, seal type, etc.). The only other consideration is manual application vs. continuous (automatic) application. Once you have made these determinations correctly, there should be no need to refresh the grease.
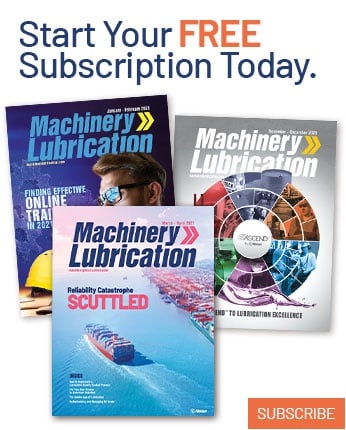