The International Organization for Standardization (ISO) has developed a cleanliness code used as the primary reviewed piece of data on most industrial oil analysis reports. The value of this code can help determine the overall cleanliness of the monitored system. Often, an end-user will establish a target value to achieve, offering a level of confidence so long as the used oil sample meets this established target. Achieving your cleanliness targets oil is not an overnight process, but it can lead to major extensions in machine life and oil service life. You may also consider a service partner who can help you maintain highly clean oil through oil regeneration or similar technologies.
The ISO code is a fantastic tool for setting target alarms and establishing a goal to achieve and maintain as it relates to system cleanliness. It is also the perfect value to use for key performance indicator (KPI) tracking, charting and posting. However, in the lubrication and analysis world, too much value is placed on the ISO cleanliness code; some laboratories have begun to report only the ISO code value, and there is a heavy reliance on this value by the end-user analyst. The ISO code should play only a secondary role when it comes to evaluating used oil sample data.
73% | of machinerylubrication.com visitors have used the ISO cleanliness code to set target alarms for system cleanliness levels |
How the ISO Cleanliness Code is Determined
When oil analysis samples are submitted to particle counting, automatic particle counting (APC) is typically used — the current calibration standard for APC is ISO 11171. In APC, particles are counted through either laser or pore blockage methods. Different laboratories may report different particle count micron levels. As an example, a lab report may include levels greater than 4, 6, 10, 14, 21, 38, 70 and 100 microns.
ISO 4406:99 is the reporting standard for fluid cleanliness. According to this standard, a code number is assigned to particle count values derived at three different micron levels: greater than 4 microns, greater than 6 microns and greater than 14 microns. The ISO code is assigned based upon Table 1. This can be seen in the example on the left.
However, without seeing the raw data, the only thing the ISO code can positively identify is whether a sample has achieved the desired target value. The ISO code does nothing to help determine any real trend information unless the value of the raw data at the given micron levels changes enough to raise or lower the ISO code.
What the ISO Code Can Tell You
It’s easy to look at the ISO table and notice a pattern. At each row, the upper limit for each code is approximately double that of the lower limit for the same code. Likewise, the upper and lower limits are double that of the upper and lower limits of the next lower code — this is known as a Renard’s series table.
The unit of measure for particle count data is “particles per milliliter of sample.” The particle counters used in laboratories incorporate much more than a milliliter of sample: approximately 100 milliliters of a sample are taken into the instrument during the testing process. The numbers of particles are counted based on this value. The total number of particles is then compared to the number of times that two will go into that total count exponentially.
Staying Clean
Why is cleanliness so important? The answer is simple: competition. In such a globally competitive market, where products can potentially be manufactured and shipped from overseas at a lower cost, maintaining a precise level of reliability and uptime is necessary to keep costs manageable. Contaminant-free lubricants and components will extend the lifetime of both, and in turn, increase the overall reliability of the equipment. Solutions like SKF RecondOil’s Oil as a Service can be an ally in the battle against contamination, simplifying the process of reaching your ISO cleanliness targets.
Using the previous example (20/17/13), this means that at the greater than 4-micron level, the number of particles measured was at the most 2^20 and above 2^19. Since particle count data is reported in particles per mL of sample, the raw data must be divided by 100.
While the general rule is that for every increase in the ISO cleanliness code, the number of particles has doubled, this certainly is not the case in every situation. Because the number of allowable particles doubles within each code number, it is possible for the number of particles to increase by a factor of four and only increase a single ISO code.
This becomes a significant problem when you have a target cleanliness level of 19/17/14, your previous sample was 18/16/13, and your most current sample is 19/17/14. For all reporting purposes, you have achieved and maintained the target cleanliness level of 19/17/14 — this suggests that your component should be in a “normal” status. Given the information presented previously, it is easy to see how you could have two to four times the amount of particle ingress and only increase by a single ISO code or have no increase at all.
Typical ISO Cleanliness Levels
The ISO cleanliness code should be used as a target — it is a value that is easily tracked for KPI reporting and a value that most people can easily understand. However, using the ISO cleanliness code for true machine condition support is limited in its effectiveness. The raw data from particle count testing allows the end-user to confirm data from other tests such as elemental analysis and ferrous index. The ISO cleanliness code does not allow this cross-confirmation to occur. Reviewing the raw data of the particle counter at all reported levels is vital in performing quality data analysis on oil sample data.
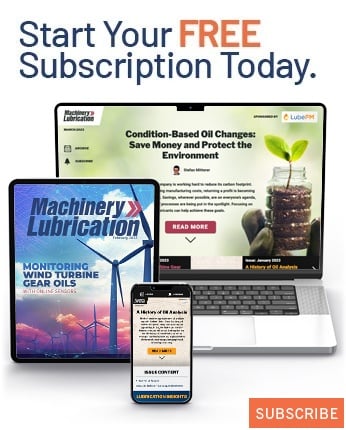