"Our company recently switched to a new lubricant supplier, and we are no longer able to buy lubricants from our previous supplier. All of our machines currently use lubricants from this previous supplier. Some of these machines are small oil compartments (gears, bearings, etc.) that need occasional top-ups and annual oil changes. Other machines are large circulating oil systems for which oil is changed 'on condition' based on oil analysis. Many motor and fan bearings are grease-lubricated. Our lube storage room has products from the previous supplier, but now products from the new lubricant supplier are beginning to arrive. What are the best ways to ensure this transition does not impact compatibility and reliability?"
Reliability should be the first thing considered when choosing a replacement lubricant supplier. Research your new supplier and talk with several of their current customers in your industry to learn of their experiences. If these customers are pleased with their lubricants' reliability, conduct some extended tests in a few pieces of equipment to ensure plant personnel are making the right decision to do business with the new supplier.
In order to address the issue of compatibility and the possibility of using the wrong oils, a full lube audit should be done to determine which of the previous supplier's lubricants are used and where they are in service. Then, a list of comparable lubricants from the new supplier should be compiled. A lube manual containing all lubricated equipment listed with the lubricant from the previous supplier as well as the compatible lubricant from the new supplier should be published and maintained.
All personnel responsible for handling lubricants (lube technicians, mechanics, electricians, etc.) should also attend some sort of transition-awareness meeting. If it isn't feasible to get all of these people together at one time, you should talk about the issues with each one of them face to face. They should be made aware of the lube manual and its location as well as how to use it.
Keep in mind that all of a particular type of lubricant from the previous supplier should be used first before introducing any of the compatible lubricant from the new supplier to the plant equipment. This means working with the plant warehouse to ensure that a lubricant from the new supplier is released only after all of the compatible lube from the previous supplier is depleted.
During a shutdown, entire trains of the smaller equipment could be drained of lubricant from the previous supplier and filled with lubes from the new supplier. For greased components, a thorough cleaning to remove all grease from the previous supplier should be performed before introducing grease from the new supplier.
Continue oil analysis on the large circulating systems and only perform an oil change when the need arises. Also, keep using lubes from the previous supplier in the large components as long as there is enough available onsite. Just because you're changing brands does not mean you should stop using good oil.
Throughout the process, it's imperative to continually update the lube manual to reflect changes in the equipment. Once the previous supplier’s lubricant has been removed from a component, remove it as an option in the lube manual. To make the process as painless as possible, you could label the machinery components with its current lubricant. Once a change is made to a particular piece of equipment, the corresponding label would be changed.
Feedback is essential to making the process go as smoothly as possible. Regularly update affected personnel on the progress of the transition. Let them know what has changed and what the next steps in the lubricant-changeover process are.
Following these suggestions will maximize the use of the remaining lubricants from the previous supplier while transitioning to lubes from the new supplier. Remember, you want this process to go off without a hitch while you squeeze every last dollar from all of your resources.
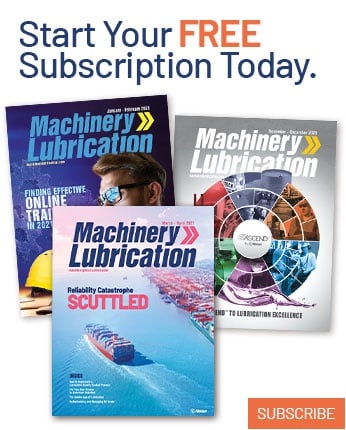