In all the plants I have visited, the lubrication systems that seem to save the most time and labor for their maintenance personnel are machines that are hard-piped to either a large bulk oil tank or a large oil tote.
While piping machines into a lube source isn’t a new concept, it is one that is rarely seen in practice. Usually you find these types of systems employed at places like power plants with large turbine systems that hold thousands of gallons of oil, but they can be used for countless other applications as well.
Piping supply lines to machines makes sense in several situations. For instance, in many refineries there are countless rows of pumps all using the same lubricant. Since these pumps are stationary and typically operated 24 hours a day, they would be good candidates to be hard-piped together to a large oil tank.
Piping to a common lube oil tank greatly reduces the amount of labor required for an oil change and can save as much as 90 percent of the labor costs when compared to the storage and handling of oil drums.
Another situation in which piping a machine to a lube oil tank could be advantageous is when a machine or component has a high oil consumption rate. I have seen some machines leak as much as 300 gallons of oil per week. All of this oil is reclaimed, the machine is taken out of commission, and then new oil is added until it is cleared to be returned to service.
In these types of scenarios, having a direct line to a bulk oil tank not only would reduce the labor costs associated with handling drums but would also greatly decrease the amount of time the machine is out of service.
When looking at the cost of an oil change, the oil usually accounts for only a small percentage of the total cost, while the cost of downtime or lost production due to the machine being out of service accounts for a much higher percentage. So you are saving money from the labor needed to handle the oil as well as by returning machines into service much quicker.
Hard-piping machines to a fixed oil supply is one way
to address a lack of available labor to handle oils.
One other factor in determining whether this type of system is appropriate for your facility is if there is enough manpower onsite to handle lubricants. If the plant is understaffed, oil changes are generally done haphazardly and only when something breaks down.
This leads to the plant’s overall machinery reliability being very low. Piping machines to a fixed oil supply is one way to address the lack of available labor to handle oils. Since this reduces the amount of hours it takes to perform an oil change, the plant can run more efficiently with the staff it already employs.
Understanding when to hard-pipe a system to oil supplies is only part of the issue. You must also weigh the risks vs. the rewards to ensure that it will be worth the initial investment. With that said, one of the largest drawbacks to these systems is the up-front costs, as some of the components can be very expensive.
Not only must you purchase the piping material and fittings, but there are also pumps, valves, flow meters and the tank from which the oil will be pumped.
The material cost is one side of the equation; the other side is the labor cost to install all of the hardware and components. This is a labor-intensive project, especially if a storage tank must be erected to house the lubricant.
When completed, the system will begin to recoup some of the costs associated with the installation, but the payback period will vary based on the amount of labor saved and downtime reduced.
Advantages of Hard-Piping
- Low cost of labor to store and handle lubricants
- Online filtration and fluid conditioning
- Low new-oil waste
- Online oil analysis
- Lower cost of bulk oil
- No drum deposits
- Low risk of the wrong oil use
Disadvantages of Hard-Piping
- High cost to install pumps, valves, piping, volume meters, storage containers, etc.
- Risk of high-volume leakage
- Lines running outdoors exposed to temperature extremes
- Defective new lubricant exposed to all machines
Another disadvantage of hard-piping systems is the risk of a high-volume leak. Since more oil is stored in a much larger volume, any leak is amplified by the amount of oil volume the system can hold. Proper monitoring and installation will mitigate leaks, but periodic inspections of all fittings and tanks are paramount to ensure any leakage or environmental impact is kept to a minimum.
The advantage of storing large amounts of oil onsite is the cost savings associated with purchasing oil in bulk volumes as opposed to drums. Generally, the larger volumes of oil you buy, the greater the discount you receive. In addition, there will be less drum inventory to be kept on hand. Of course, not all facilities utilize enough oil for piped lubricant systems to be cost-effective.
60% | of plants have machines that are hard-piped to a large bulk oil tank or a large oil tote, based on a recent poll at machinerylubrication.com |
Beware of buying tanker trucks full of oil. If the truck is filled with the wrong oil or a bad batch of oil, all of the machines piped to the storage tank will be at risk of receiving this bad oil. The only way to ensure the oil quality coming in is to sample each compartment of the truck before it is loaded into the storage tank.
A bulk storage system complete with piping offers many great sampling opportunities so you can be confident that the machines attached to it are receiving oil that is clean, cool and dry. If you are able to deliver lubricant to your machines with those three qualities, no matter how it gets there, the machines will have a longer life and run more efficiently.
.
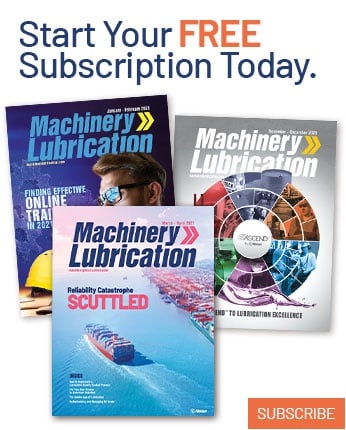