"Can you suggest the best method for detecting varnish in turbine oils (both gas and steam turbines), as well as the symptoms and best proactive early action to take?"
Varnish in turbine systems causes very serious problems. If not controlled, it can occur in even the best maintained machines. However, with proper monitoring and varnish-removal techniques, you can reduce the risk of machine failure and loss of production.
When applied to lubrication, varnish produces a thick, film-like deposit on interior parts, which can cause sticking and machine breakdown. Over time, these deposits can thermally cure to a tough enamel-like coating and increase the risk of failure by restricting the flow of oil and the machine’s moving parts, clogging filters and reducing heat transfer. Some factors that contribute to varnish include heat, air, moisture and contaminants.
The following are examples where varnish might occur in both gas and steam turbine systems:
- Black, crusty deposits on mechanical seals
- Gold adherent films on valves
- Charcoal-like deposits on Babbitt sleeve bearings
- Gooey-brown accumulations on filters
- Black, scabby deposits on mechanical seal surfaces and thrust-bearing pads
- Carbonaceous residue on mechanical surfaces
Varnish can be very difficult to detect. Even a standard oil analysis test may show no signs of varnish when it is present. The best method for detecting varnish is via precision oil analysis with uninterrupted intervals of consistent and representative samples taken with the appropriate test slate. Deploying this strategy will aid in the early detection of varnish before it can cause total machine failure.
Once varnish is found in the system, there are two proactive strategies that can be taken. The first and most popular is continuous electrostatic oil cleaning. This method removes charged contaminants, which are naturally polar, creating positive and negatively charged poles. This will clean the fluid system until varnish is no longer present.
The second method, which is used for excessive varnish within a system, is off-line or chemical cleaning. This method can be costly because it often requires the system to be shut down. Chemicals are flushed throughout the system, softening contaminants and flushing them through fine filters. This process can take several hours or up to several days, depending on the amount of varnish. The system must then be flushed again until all contaminants are removed so the new oil will not be contaminated.
While several different methods and tests can be deployed in your fight against varnish, being proactive is key. Remember, good operating practices and constant monitoring will be your best defense.
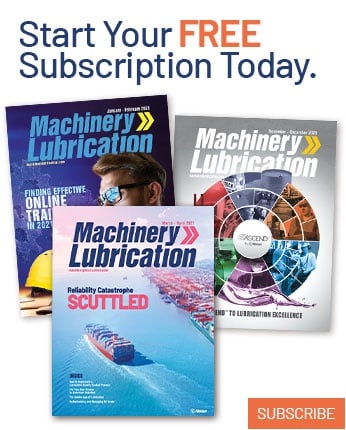