"We have had numerous questions lately about hot service and how we size reclassifiers for temperature of the pumpage. We never really considered temperature before, and now the 'high temperature' seems to be getting ever lower.
"Several specifications, including two of the six largest oil refiners in the world, limit oil mist to 450 degrees F, and now I have one that indicates a limit of 300 degrees F. Many specifications call for heavy service factor reclassifiers on pumps in hot service, but what is hot service? To me, it's like saying, 'It is hot today.' Was temperature ever a concern with the highly successful oil-mist systems 20 and 30 years ago?"
The answer to this question has never been a secret and can be found in many texts. On numerous occasions in the 1960s and 1970s, oil mist was first applied with great success to all types of API pumps. Pure oil-mist application was chosen in the 1970s for every conceivable type and style of process pump. These included dozens of pipestill bottom pumps with pumping temperatures of 740 degrees F (393 degrees C) in the world’s three largest oil refineries. (The hottest pumpage at several world-scale steam crackers was perhaps more in the range of 600 to 640 degrees F).
For those asking questions about hot service and how reclassifiers are sized, have them look at an API 610 style pump. Encourage them to view these pumps either in the field or on one of the numerous pump manufacturers’ websites. They might then realize that a high-temperature mechanical seal and some ambient air space are located between the pumpage and the bearings. Therefore, much heat gets radiated into the surrounding air. Barrier seals often assist in heat removal.
Obviously, there is a significant heat loss between the pumpage in the pump casing and the lightly loaded and thinly oil-coated radial bearing in API process pumps. Additional heat will be lost as it travels from the radial bearing to the more highly loaded thrust bearing set. Still, bearing housing temperatures have never exceeded 240 degrees F (116 degrees C) in pumps at major oil refineries. Of course, operation at these temperatures would require installing a personnel-protection shield on bearing housings.
In the 1980s, if an owner/operator insisted on using mineral-oil-based oil mist in open systems, he or she would be advised to select an ISO viscosity grade 100. There were then (nor are there today) neither oil rings (slinger rings) nor constant-level lubricators in pumps lubricated with pure oil mist. Generally, though, a smart user would use a synthetic ISO VG68 in pure oil-mist systems serving process units with pumps whose pumping temperatures are in the range of 600 to 740 degrees F.
So for the past 40 years, reclassifier selection has never had to take into account the temperature of the pumpage in API pumps. Temperature simply does not enter the picture, especially not when you apply the oil mist per modern API rules. These rules ask you to apply mist from the space nearest a bearing housing protector seal in a through-flow mode toward the center of the bearing housing. Incidentally, through-flow mode was routinely done as of 1977.
Oil-mist lubrication is applied to a pump bearing housing in accordance with API-610, 10th Edition. Note the dual mist-injection points and use of face-type bearing protector seals to prevent mist from escaping to the atmosphere.
If an occasional user purchases a close-coupled non-API pump for hydrocarbon service at 740 degrees F, he should be severely criticized for making a very risky choice. Hopefully, his risky conduct will come to someone’s attention before he ends up transferring his death wish to the process operators.
It has been said that you cannot change the safety and reliability culture without first changing the system. The system is your organization. If you allow specifications to be written or amended by people who make no effort to be informed, your company or employer will soon lag behind. Becoming knowledgeable in a subject must be a prerequisite for the person issuing a lube-related specification. Without such knowledge, and as others continue to make progress, your employer will lose more and more ground to the competition.
Sometimes a specification change will make sense and will actually have a beneficial effect on safety and reliability. At other times, and when an unduly tight specification is issued, the exact opposite may result.
Look at the whole picture and always make informed choices. Limiting oil-mist applications to pumping services not exceeding 300 or 450 degrees F begs the question: What lube-application method will these users choose for their pumps at 600 and 740 degrees F? Other than the well-proven oil mist, only liquid oil sprayed directly into a rolling-element bearing's cages is a suitable option for these reliability-focused individuals. Reverting back to oil rings and constant-level lubricators is a quantum step backward.
As of 2013, well more than 100,000 process pumps are successfully lubricated by plant-wide oil-mist systems. However, only 26,000 electric motors use oil mist on their bearings. Some of these have been on oil mist for 35 years without ever having a bearing replaced or changed. Extending an oil-mist system to also service electric motor drivers makes much sense and yields rapid payback.
An uninformed owner/operator contemplating reverting to grease-filled single-point automatic lubricators will be faced with many important decisions. Premium-grade motor greases separate into soap and oil when pressurized. Lesser greases may not separate as easily under pressure but neither will they provide superior protection. Plant-wide oil mist gets around all of these concerns.
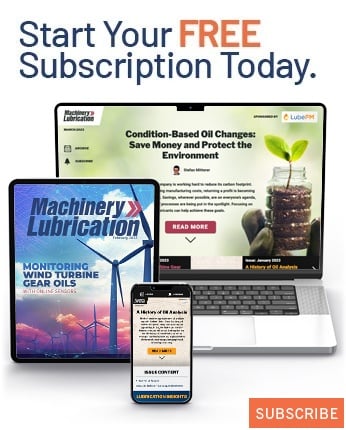