"What is the best equipment for testing transformer oil?"
Several variables must be considered in order to answer this question, including your budget, the volume of samples to be tested and the need for real-time continuous monitoring.
Cost is generally the first consideration. Like most business decisions, a cost/benefit analysis should be conducted to determine whether testing is a valid expense. Sadly, in many cases, once the cost of testing or testing equipment is calculated, the answer typically is, “We can’t afford that now.” The idea often is then put on the back burner where it eventually withers and dies.
However, if you compare the cost of testing or testing equipment to the cost of a replacement transformer, labor to remove and reinstall, and most importantly the cost of downtime, how can you afford not to perform testing?
The next consideration should be whether the volume of samples is sufficient to justify the cost of onsite testing equipment and personnel. In most cases, the sample volume is not enough to warrant this expense. In these cases, a third-party lab must be selected that can perform the following tests for in-service transformer oils: interfacial tension (ASTM D971), acid number (ASTM D664), dielectric breakdown voltage (ASTM D877 or D1816), Karl Fischer water (ASTM D1533), oxidation inhibitor (ASTM D4768 or D2668) and dissolved gas analysis (ASTM D3612).
In addition, the following tests should be conducted upon receipt: liquid power factor (ASTM D924), specific resistance (ASTM D1169), corrosive sulfur (ASTM D1275), gassing tendency (ASTM D2300), oxidation stability (ASTM D2440) and particle count (ASTM D6786).
If the decision is made to perform testing in-house, many of the necessary tests may be outside the standard capabilities of the "lab-in-a-box" equipment currently on the market. This will require purchasing multiple pieces of equipment, which can be several thousands of dollars per piece. Unless the volume of samples is significant, there is no initial cost savings to purchasing onsite equipment. Nevertheless, the benefit of having instant test results allowing for the identification and correction of an impending equipment failure could well justify the cost as indicated above in the form of repair work and downtime.
In regard to real-time condition monitoring, as technology advances and test equipment becomes less expensive, it may be well worth the investment. Several companies now offer monitoring equipment for continuous dissolved gas analysis as well as instruments to measure electrical conductivity, dielectric constant, oil temperature, etc. Many of these have the option of transmitting data to a central location via Wi-Fi, adding the convenience of monitoring a transformer’s condition from the control station. This could potentially reduce or eliminate the need to periodically sample and test the oil, as you would allow the system to monitor the oil and test only when an exception condition was indicated.
Keep in mind that there is no "one-size-fits-all" approach. The best equipment will be whatever provides the most accurate results, is most affordable and, most importantly, will actually be used. When making these decisions, be sure to take into account the cost of the downtime to be incurred if you suffer a catastrophic failure.
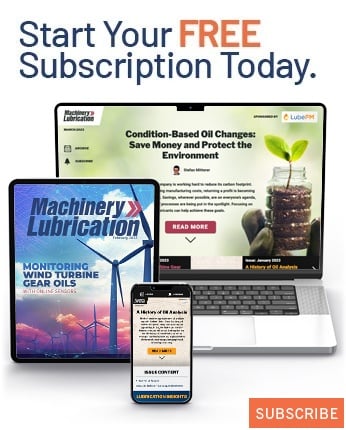