"A few of the machines at our plant have been having problems with what is suspected as polishing wear. Can you explain what this is as well as some of the best ways to help prevent it?"
The term polishing wear is typically used to describe interactions between two solids that remove material from the surface of at least one of the solids while at the same time producing a polished finish on the surface. The result is a surface that reflects light brightly like a mirror.
Polishing wear may also be generated as a result of a chemical-mechanical interaction between the surfaces. For instance, it is possible to find polishing wear when there is a high concentration of soot in an engine oil. Soot is formed during the combustion process and enters the crankcase with combustion gas blow-by. Soot has an original size of 0.01 to 0.05 microns but tends to agglomerate to form larger particles in the crankcase. An oil’s ability to disperse soot is critical to preventing soot-polishing wear caused by the effects of soot on the oil’s anti-wear additives.
In high-pressure hydraulic systems, the hydraulic oil tends to accumulate silt. This silt may lead to valve sticking and polishing wear.
Another example may be found in gearboxes where the oil carries debris from micropitting, which can be as small as 1 micron. These particles act as polishing agents. The polishing wear is often found on gear teeth with micropitting, both in areas between the micropits and in areas without micropitting.
Keep in mind that these chemical-mechanical interactions involve both chemical and mechanical elements. In this case, an additive (such as an extreme-pressure or anti-wear additive) or a protective film that covers a metal surface is removed by contact with the other rubbing surface. The protective layer is then reformed, consuming a thin layer of the metallic surfaces under interaction.
Sulfur-phosphorus additives normally produce minor wear due to the chemical-mechanical interaction. In certain cases, the sulfur-phosphorus types can be too chemically reactive, resulting in polishing wear. This type of wear is undesirable because it reduces gear accuracy by wearing away the tooth profiles.
In some circumstances, the extreme-pressure additives can be detrimental to slow-speed gear applications (less than 10 feet per minute), causing high rates of wear known as polishing. Potassium-borate additives can be used to deposit extreme-pressure films without a chemical reaction with the metal.
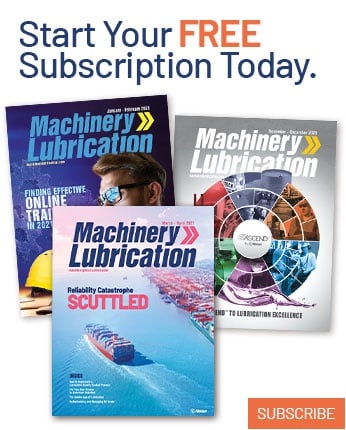