"This winter we sent a sample of a 220-centistoke extreme-pressure gear oil to our lab for routine analysis. The oil was used in an outdoor gearbox for about two years in Canada. Most of the analysis results appear normal (viscosity is 217 centistokes at 40 degrees C, only 100 parts per million water and the acid number is 0.65). However, the flash point is 76 degrees C, which is well below the new oil level of 190 degrees C.
A second sample sent to the lab confirms the results of the first test. What could have caused the flash point to drop so dramatically while the viscosity and acid number are at near normal levels? What inspections of the gearbox could have confirmed our suspicion? What risks could this condition present? How could the root cause be corrected?"
For a definitive answer, many elements relating to oil analysis and machinery maintenance must be known. For instance, was the new oil analyzed and what was its viscosity? Is there a baseline for comparison? Also, was the oil sample collected in the right manner? What are your maintenance practices? Are top-up containers and machines properly labeled so the correct lubricant is used with the correct machine? What training do technicians have? These are some of the key factors that can affect the health of the lubricant and the oil analysis results.
A flash point that drops suddenly could potentially cause an explosive situation. Any source of ignition could spark a reaction. Remember, flash point is the lowest temperature at which an ignition source causes the vapors of the lubricant to ignite under specified conditions. Machinery seals can also be affected, resulting in unforeseen leaks, equipment damage or further contamination of your oils.
Base oil cracking is just one example of what can happen if the flash point drops. This can occur if machines and components are placed in proximity to steam or furnaces. Regardless of the machine, location or heat source, if the lubricant temperature exceeds 550 degrees C, there is a risk of cracking.
Several things can help guard against this, such as having a proper baseline for the new oils in order to have a true comparison when oil analysis tests are conducted. Performing Fourier transform infrared (FTIR) spectroscopy can help you discover what contaminants could be in the lubricants that may not show up in other test slates.
Also, ensure technicians are trained in proper sampling techniques to prevent false-positive readings due to contamination. World-class lubrication storage and handling procedures should be practiced to prevent lubricants from being contaminated.
It is likely that a chemical has contaminated your lubricant. This may have occurred in the sampling process or because of poor handling or machine maintenance practices. In this scenario, more data is needed. Any type of historical baseline data would be helpful, such as FTIR, water, viscosity and elemental testing.
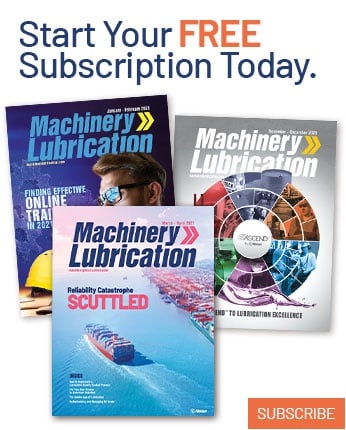