"Could using the wrong grade of lubricant instead of the manufacturer's recommended grade cause a bearing failure?"
Disregarding the manufacturer's recommendations for any piece of equipment or component could potentially lead to failure of the equipment or voiding the machine's warranty. Of course, there are exceptions to this, particularly as it relates to the environmental conditions, speed, load and temperature.
Whenever a new machine or component is installed, one of the first things to be addressed is the type of lubricant to use. Typically, the equipment will come with a recommendation from the manufacturer. While this recommendation may be somewhat vague, it can provide crucial viscosity information.
Base oil viscosity is one of the most important properties manufacturers consider when making a lubricant recommendation. It should take into account the speed, load and ambient temperatures. While this is a great start when choosing a lubricant, keep in mind that the working environment of the component or machine could be outside the manufacturer's tested parameters.
The base oil type is also a key factor. Group I base oils are some of the cheapest base oils on the market and are solvent-refined through a simpler refining process. Group II base oils are often manufactured by hydrocracking and are becoming more prevalent in today's market. They have a clearer color and better antioxidation properties. Group III base oils generally are severely hydrocracked. They are sometimes described as synthesized hydrocarbons and are designed to achieve a purer base oil. Group IV base oils are polyalphaolefins (PAOs). Synthesizing is the process used to produce these synthetic base oils, which are ideal for a wide range of temperatures. Group V base oils include all other base oils, such as polyalkylene glycols (PAGs), phosphate esters, etc. These oils are sometimes mixed with other base stocks to enhance oil properties.
Another consideration is the additive package. Additives have three basic roles: to enhance your base oil with antioxidants, corrosion inhibitors, foam agents, etc.; to suppress your base oil properties with pour-point depressants and viscosity index improvers; and to give new properties to the base oil with extreme-pressure additives, detergents, metal deactivators and tackiness agents. Remember, once your additives are depleted, they are gone, so it is vital to check your additive package.
Using the appropriate grade and type of lubricant is essential for proper bearing performance. It is usually best to adhere to the original equipment manufacturer's recommendations when making your lubricant selections. Failure to do so can lead to shortened bearing life. However, if you decide not to follow the manufacturer's recommendations, be sure to allow for the temperature, application and conditions.
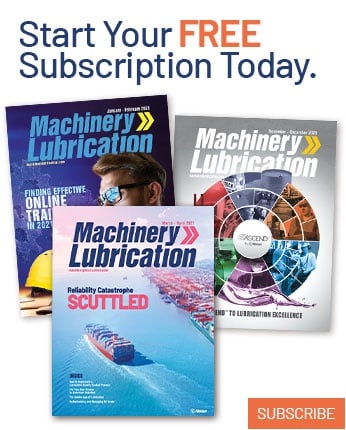