When you throw a rock in a lake, it goes down - fast. Wear particles are heavier than rocks of the same size, often four to five times heavier. Of course, the heavier the object, the faster it falls. Oil is viscous, and this resistance can slow down the rate objects fall, but it doesn’t come close to stopping them.
The rate at which objects fall in viscous fluids is described by Stokes’ law. In sum, (1) the larger the object, (2) the heavier the object (density), (3) the thinner the fluid (lower viscosity), (4) the lower the density of the fluid (oil has extremely low density), the faster the object falls. Conversely, small, low-density objects in highly viscous fluids settle more slowly.
In oil analysis, this is critical because you want to know about the particles in your oil - all of the particles, including those that can damage machines and those that reveal damage has already occurred and is continuing to occur. Not much in oil analysis is more important than this.
This article will address two common oil analysis-related problems that sadly are often dismissed by both users and laboratories. These problems are sampling oil from machines at rest (oil not circulating) and failing to properly resuspend particles just prior to analysis.
Figure 1
Analyzing the Data
In reviewing research on particle sedimentation, I discovered that all of the data points to the same general conclusion: particles are very instable in lubricating oils, even those that are completely invisible to the naked eye.
Figure 2
In Figures 1-4, you can see how Stokes’ law governs the speed of particle descent. Figure 1 reveals that 30-micron iron particles can descend at a rate of 2 centimeters per minute. The viscosity is rather low, but then again this is not uncommon for very warm oils and oils that have been diluted by solvents prior to lab analysis.
Figure 2 shows that iron particles settle at a rate roughly five times the speed of dirt particles (silica). In Figure 3, the data indicates that barely visible 100-micron steel particles can fall 4 inches in viscous 15W40 motor oil in less than one minute. Finally, in Figure 4, you see that extremely small 20-micron Babbitt particles (say, from journal bearings) settle ½ inch in just four minutes in ISO VG 32 turbine oil.
Figure 3
Figure 4
Dormant Fluid Causes Unrepresentative Oil Samples
Too often oil samples are taken when machines are at rest (not when they are running). Sometimes this is avoidable, but sometimes it is not. Live oil samples are always best. Circulation keeps the fluid homogenous at the time the sample is taken. Lack of fluid circulation causes particle settling and sedimentation (see Figures 1-4). The longer the delay between when a machine is turned off (stopping oil movement) and when the oil is sampled, the greater the number of particles not received in the sample bottle.
Particles are like data. This data provides important information that can prescribe a needed corrective action. When particles settle out of the oil, you lose data. This lost data may prevent you from being aware of an abnormally high particle count or advanced machine wear condition. This would produce a false negative in the oil analysis results. This means the oil’s condition may be falsely reported to be better than reality.
Evidence of particle sedimentation shows up in oil sumps and reservoir bottoms. Sampling the bottom of the sump or reservoir provides little help since the sludge and sediment that accumulate there are a repository of data spanning weeks, months or even years.
This is not representative of the current conditions, including the health of the oil, the contaminant level of the oil and the active rate of machine wear.
The obvious solution is to use the live-zone sampling technique. If this is not possible, the sample documentation or label must disclose that the bottle contains a cold or dormant fluid sample. This will be taken into account by the analyst when the data is interpreted.
Not all tests are influenced by dormant fluid samples. Figure 5 shows the properties of highest and lowest risk.
Figure 5
Particle Settling in Bottles and Glassware
I’ve toured a large number of oil analysis labs in my career, including several in the last couple of years. From my observations, the vast majority of these labs seem to downplay the importance of proper sample agitation or have the misconception that their in-house method is adequate.
In fact, proper agitation is seen, but it is rare. Standards such as ASTM D7647 and ISO 11500, which provide guidance on the proper use of particle counters, clearly emphasize the importance of agitation. For example, the following is from ASTM D7647:
“Homogenize the incoming sample by shaking the sample container and its contents in the mechanical shaker. For samples 200 mL or less, shake for one minute. For samples 200 mL or larger, shake for three minutes.”
Several years ago I supervised a very basic study on sample agitation. Four identical samples were prepared using a standardized test dust (mostly silica) as the contaminant. To obtain a baseline, one of the four samples was analyzed using a freshly calibrated particle counter (control sample).
The results showed 1,658 particles greater than 10 microns per milliliter (see Figure 6). The remaining three samples were then allowed to rest overnight.
Figure 6
The following day, Sample 1 was analyzed without agitation. The results showed 29 particles or less than 2 percent of the particle count found in the control sample. Sample 2 was analyzed after five minutes of vigorous hand agitation.
This produced 1,287 particles or 78 percent of the control sample. Finally, Sample 3 was analyzed after five minutes in a paint shaker. The results were nearly identical to the control sample.
The importance of agitation was stressed in a National Fluid Power Association report jointly authored by Caterpillar Inc., Hiac/Royco and Butler Machinery. The report stated that “the sample extracted from the sample bottle for analysis must be representative of the whole bottle ... Since settling and aggregation can drastically affect the measured particle count, the samples are shaken vigorously before analysis for three to five minutes on a paint shaker ... This breaks up aggregates and disperses the particles uniformly.”
Influence of Aged Samples
Samples that have been left undisturbed for prolonged periods of time (e.g., more than one week) drop out insoluble impurities and suspended particles. These include dirt, wear debris, water, sludge, oxide insolubles, glycol, dead additives, carbon insolubles, friction polymers and certain additives.
After aging, particles and impurities exhibit coherent forces that result in agglomerations in the form of sludge or microscopy clusters. Particles also are known to stick tightly to bottle and container surfaces.
The longer they stay undisturbed, the tighter they adhere (by Van der Waals forces and electrostatic forces). These agglomerations and adherent forces vary inversely with particle size; that is, smaller particles are more difficult to redisperse than larger particles.
Oil Sample Preparation Pointer
Some oil samples and laboratory tests have higher risks than others. These would include low viscosity fluids (e.g., ISO VG 46 and below), large particles (greater than 20 microns), oils with high varnish potential, heavy particles, aged samples, ferrous density tests, particle counting and wear particle analysis. The best ways to mitigate these risks are delineated in the list of laboratory do’s and don’ts that follows:
Laboratory Do’s
- Place samples in an ultrasonic bath prior to mechanical agitation for at least 30 seconds (especially with aged samples).
- Agitate samples vigorously in a mechanical shaker for no less than three minutes (bottle ullage no less than 25 percent).
- Degas the sample (ultrasonic followed by vacuum works best) immediately after agitation. (Degas procedure required only for particle counting.)
- Analyze samples immediately after degas.
Laboratory Don’ts
- Use hand agitation.
- Utilize a laboratory rocker, orbital oscillator or roll device (e.g., hot dog roller) for agitation (except to keep a previously mechanically agitated sample fresh).
- Attempt to mechanically agitate completely full bottles.
- Dilute samples with thin solvents. If dilution is required, use ultraclean oil instead. Low viscosity solvents accelerate particle drop-out.
- Wait several minutes while the sample sits motionless before analysis.
- Assume no one cares about agitation.
A study on the need for sample agitation was sponsored by the Naval Air Engineering Center using analytical ferrography. The researchers found that even large iron and steel particles did not resuspend completely with aged samples when agitated by hand.
In their study, when samples were agitated by a paint shaker for two minutes, approximately 47 percent more particles appeared in the 55-millimeter entry region of ferrogram slides compared to samples agitated vigorously by hand for 30 seconds. Likewise, 59 percent more particles appeared at the 10-millimeter region on ferrogram slides (representing smaller particles).
The best way to break up these agglomerates and dislodge particles from container walls with aged samples is to use an ultrasonic bath followed by vigorous mechanical agitation (e.g., a paint shaker) for three minutes. Some procedures call for use of an ultrasonic bath after mechanical agitation to aid in the coalescence of air bubbles before vacuum degas. Perhaps the best method is to sonicate both before and after mechanical agitation.
While it may be wishful thinking on my part to expect samples to be properly collected in the plant and properly agitated in the lab, I am hopeful. I also realize that proper agitation comes at a cost. However, there is also a cost to bad oil analysis data. Remember, the very oil analysis tests that need agitation the most are the ones the labs charge the most for and the ones that provide critical information on machine health.
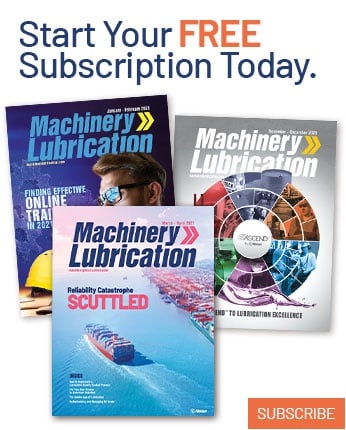