Wear particle identification is a critical aspect of oil analysis. A variety of options are available for analyzing wear debris, but one powerful technique that frequently gets ignored is analytical ferrography. However, before conducting this type of oil analysis test, there are essential steps that must be taken first. For instance, it’s not uncommon for a plant to perform oil sampling or use onsite oil analysis for screening or even an offsite laboratory for routine testing.
These steps are part of a predictive maintenance strategy, with the primary goal of detecting machine wear at an early stage and finding solutions for remediating the problem effectively. This goal can be broken into two substages: fault detection and exploratory analysis.
Fault Detection
The technologies and practices employed at this stage should all be routine in nature. They will include particle counting, vibration analysis, thermography, filter debris inspection, magnetic plug inspection, online debris monitoring and any other technology or practice that has the objective of picking up on clues of a potential fault.
These techniques are performed onsite and practiced individually but are also connected systematically to match rising trends with a dynamic interpretation. Any one of these fault detection strategies can independently trigger an investigation into a problem, particularly when a critical alarm is exceeded. Nevertheless, if several cautionary alarms are reached across several screening strategies, then an investigation into the rising concerns should be explored.
In addition to these onsite screening methods, routine laboratory testing should be established as well. In terms of wear debris detection ability, these tests will likely include elemental analysis or ferrous density. However, none of these technologies will likely be able to provide precision data, such as where the wear particles originated and how they came to be generated.
This is the limitation of fault detection technologies and why an in-depth exploration is needed with proven diagnostic or prognostic capabilities. The exploratory actions to be taken once a fault has been detected should also be specified and understood. Otherwise, the ability to remedy the problem effectively will be severely diminished. Unfortunately, this is a missed opportunity for many facilities today that have failed to include wear particle characterization in their oil analysis program.
Exploratory Analysis
At this stage, an investigation into the potential tribological issue is essentially underway. Those in charge of this investigation are like detectives, and good detectives will use all available resources to develop and support their conclusions. These resources include all data from the fault detection technologies in addition to any new approaches, e.g., further laboratory oil analysis testing.
This is where value is gained from studying an oil sample under a microscope using methods such as analytical ferrography (with preparation of a ferrogram), patch ferrography (with preparation of a filtergram), optical imaging methods and scanning electron microscopy (SEM).
While determining the existence and amount of wear particles in an oil sample is essential, understanding the particles’ size, shape and composition is equally important if the goal is to identify where and how those particles were produced. Standard particle counters can provide an average number of particles by size groups, but those results do not distinguish between environmental contaminants and generated wear particles.
Elemental spectroscopy can offer details about certain metallic elements increasing in concentration, but these results will be skewed in cases with rising large particle counts, since large particles are not generally measured by this method.
This is a key diagnostic limitation, because the population density of larger wear particles is directly related to severe wear modes such as adhesion, surface fatigue and abrasive wear. This limitation is what opens the door to technologies like analytical ferrography and other microscopic wear particle characterization methods.
Analytical Ferrography
When a ferrogram is prepared and analyzed under a microscope using polarized bi-chromatic techniques, it helps the analyst differentiate between wear particles and those of organic and translucent materials, as well as helps identify particle composition. Heat-treating techniques also improve the analyst’s ability to extricate particle composition details.
68% | of oil analysis programs employ analytical ferrography to analyze wear debris, according to a recent poll at MachineryLubrication.com |
The categories of particle composition and how they appear on a ferrogram have been defined as white nonferrous particles, copper particles, Babbitt particles, contaminants (usually dirt or silica), fibers and ferrous particles, including high-alloy steel, low-alloy steel, dark metallic oxides, cast iron and red oxides (rust). Refer to the related ASTM standard for a structured reporting and databasing technique for interpreting particles presented on a ferrogram or filtergram.
Besides the particle size and composition, the analysis of a ferrogram under a microscope can provide further benefits when the particle’s shape is taken into consideration. Whether the particle’s shape is spherical, spiral or laminar, or if the surface looks rough, smooth or has clear striations will all indicate a unique wear mode. In fact, there are several books dedicated to the study and characterization of wear particle shapes and how they point to specific wear modes.
Using a Ferrogram
The oil sample (presumed to contain wear debris) is initially diluted for improved particle precipitation and adhesion. The diluted sample flows down a specially designed glass slide called a ferrogram. The ferrogram rests on a magnetic cylinder, which pulls ferrous particles out of the oil and pins them to the glass slide.
Due to the magnetic field, the ferrous particles align themselves in chains along the length of the slide, with the largest particles being deposited at the entry point. Nonferrous particles and contaminants, which are unaffected by the magnetic field, travel downstream and are randomly deposited across the length of the slide. The deposited ferrous particles serve as a barricade in the removal of nonferrous particles, which otherwise would tumble off the end of the slide.
Once the initial fault detection triggers an investigation, the analytical approach requires using all available clues in order to make a sound conclusion and determine if corrective action is necessary. The results from particle counting, vibration analysis and thermography can be used in conjunction with ferrous density testing and elemental analysis to consider all possible causes and effects of the initial trigger.
When the type of information provided by these strategies is not precise enough to point to a particle root cause and location within a machine, more detailed analysis must be employed. After all, the end game is to isolate the root cause, and analytical ferrography is a proven method to bring evidence to the root cause. Make sure your lab doesn’t dismiss its value and fail to perform this critical test.
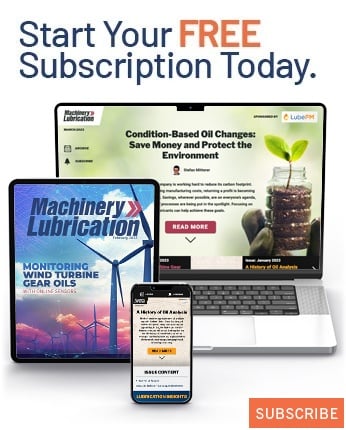