Geared systems are ubiquitous in industrial plants. Gear reducers can number in the thousands in a medium-size manufacturing facility. While not all gearboxes may be deemed critical, those that are require comprehensive condition monitoring, with oil analysis being a key component of a well-engineered program.
For many, the word critical is synonymous with the word big in relation to rotating equipment. This is a common misconception. The gearbox could be a large reducer on a turbine set, or a small gearbox on a wastewater pump, yet both may be critical to production or safety. Even a gearbox with only two quarts of oil in it may require routine fluid monitoring. The selection of gearboxes that require routine oil analysis should be based on reliability goals, not simply oil volume.
The purpose of any predictive
condition-monitoring program is to detect abnormalities in the system at a
sufficiently early stage in order to avoid unscheduled downtime. While this
may not always be possible, a good oil analysis program can go a long way toward
achieving this goal, provided the test slate is selected to detect abnormalities
based on machine wear, lubricant condition, contamination or a combination of
each. This article discusses the recommended tests to address these issues and
provides a framework for developing a well-engineered gearbox condition-monitoring
program.
Machine
Wear
Gear systems involve surface-to-surface contact. Generally, this will entail
either rolling or sliding contact, or a combination of the two, depending on
gear type, speed and load. Some wear debris is expected under normal operating
conditions. Knowing this, gear designers choose materials and manufacturing
processes that impart wear resistance to gear teeth, pinions and shafts. The
most common material used for commercial gearing systems is steel. Different
hardening techniques such as carburizing, nitriding, flame and induction hardening
are employed to obtain the desired properties and resistance to wear.
While high hardness imparts wear resistance, specifically scratch and dent resistance, nonferrous gear materials such as bronze are occasionally used. For example, worm gear applications typically combine a steel bull gear with a bronze or copper worm gear. In this case, because the worm gear is sacrificial, it is expected to wear to some degree and must be carefully monitored.
Because of this, wear metal detection and analysis is required for all gearboxes. The most common method of wear debris detection is atomic emission spectroscopy, commonly referred to as AES. AES is used to detect wear metals, additives and contaminants, and is one of the most commonly used oil analysis tests. However, care must be taken not to overstress the importance of this test because, depending on instrument type, the test may be limited to detecting particles less than 5 to 10 microns in size. While this test and its inherent size limitation may be adequate for some components, gears are particularly prone to certain wear conditions that may generate much larger particles, which may go undetected by AES alone. It is important when selecting a gearbox test slate to understand common gearbox wear mechanisms, the typical particle size distributions produced by the mechanisms and to relate these to the value of detecting them using AES and other wear particle detection methods.
Common gear wear mechanisms include:
Normal Sliding (Rubbing)
During normal gear tooth sliding, the type of wear particles generated are rubbing
wear particles less than 10 micrometer to 15 micrometer in size. These are laminar
shaped, with smooth surfaces. However, during the break in of a new gear set,
the wear particles generated are larger than normal rubbing wear particles and
have a different generation mechanism. Similarly, excessive wear caused by an
overload condition, misalignment or insufficient lubrication will generally
have a much larger particle size, beyond the size range limitation of AES.
Pitting
Pitting is a fatigue phenomenon that occurs when a fatigue crack initiates at
the surface of a gear tooth or at a small depth below the surface. The crack
usually propagates for a short distance in the direction almost parallel to
the tooth surface before turning or branching to the surface after repeated
cycles. When cracks grow to the extent that a piece of the surface material
is released, a pit is formed. If several pits grow together, the resulting large
pit is often referred to as a spall. Moisture in the lubricant can promote pitting
through local hydrogen embrittlement of the metal. Similarly, abrasive particles
in the oil will also cause pitting by indenting and scratching the tooth surface,
causing stress concentrations, and disrupting the lubricant film. Depending
on the severity, pitting may result in 10-micron or greater sized particles
that are flat, with jagged edges and directional fatigue lines. Fatigue failure
is often missed by oil analysis if AES is the only detection method employed
for wear debris.
Micropitting
In gears that are surface hardened (carburized, nitride, induction hardened
and flame hardened), pitting may occur on a smaller scale, typically less than
10 microns in size. To the naked eye, the area where micropitting occurred appears
frosted, a popular term describing micropitting. In this case, much smaller
particles are observed, which may be detectable with AES, although as the problem
grows, macropits are formed which can exceed the detection capabilities of AES.
Abrasion
Abrasive wear in gear sets is typically caused by hard, sharp-edged particles
that contaminate the lubricant. Contaminants in the gear set can be internally
generated, ingested through breathers and seals or added during maintenance.
Internally generated particles are wear particles sourced from components in
the system. These wear particles are especially abrasive because they become
work hardened when they are trapped between gear teeth. Again depending on severity,
abrasive wear particles can be 5 microns and greater.
Scuffing/Adhesion
Scuffing, often referred to as adhesion, occurs in gear teeth under boundary
lubrication conditions. If the lubricant film is insufficient or the oil has
depleted or ineffective EP protection, metal-to-metal contact can break down
the oxide film that usually protects the gear surface. When this occurs, bare
metal surfaces may locally weld and tear, resulting in catastrophic damage of
the gear teeth and the formation of large chunks. The solid phase welding of
the gear surfaces results due to extremely high frictional heat. Inspection
of gear teeth surface will show torn surfaces and metal transfer from one surface
to other. Gears are most vulnerable when they are new and their surfaces are
not smoothened due to proper running-in. Scoring of a gear has a similar effect
as scuffing. Accurate gear teeth, rigid gear mounting and good alignment will
reduce the chance of scuffing.
Because many of the wear mechanisms commonly encountered by gears result in what are usually considered large particles (greater than 10 microns), it is important to include AES, RDE (rotating disk electrode spectroscopy), XRF (x-ray fluorescence spectroscopy), RFS (rotrode filter spectroscopy) and DRF (direct reading ferrography) in the routine test slate selection to help detect active gear wear.
Whenever high wear rates are observed, it is vital that the root cause be investigated and corrected to prevent further problems. In gear applications, one of the most effective tools is complete analytical ferrography (AF). In AF, the active wear mechanism can be determined based on particle morphology, including particle size, shape, color and edge detail. Examples of common ferrographic images are shown in Figures 1, 2 and 3. Whenever elevated wear is detected by AES, RDE, XRF, RFS or DRF, complete analytical ferrography should be considered as an exception test to help determine the root cause of the wear problem.
Figure 1. Normal Rubbing
Wear
Figure 2. Severe Gear
Fatigue Wear
Figure 3. Cutting
Wear
Contamination
Gear systems may be open or enclosed. Open gears are expected to operate with
higher levels of contamination than enclosed sets such as bath-lubricated systems.
The most common contamination-related problems involve moisture and airborne
abrasive particles from external sources.
Because of this, gear test slates should include routine particle and water contamination tests.
ISO Particle Count
Although ISO particle counting was originally developed to determine fluid cleanliness
in hydraulic systems, it can also be used effectively to monitor gearboxes.
Significant increases in the particle count can indicate that a filter has failed (if equipped), contamination is entering the system or the wear rate has increased. Just like monitoring hydraulic systems, gearbox particle count analysis is contingent on setting effective target cleanliness limits. However, the average fluid cleanliness of a gear system is likely to be significantly higher than a typical hydraulic system, with target cleanliness levels adjusted accordingly. Just like wear debris analysis, particle counting depends on exception testing to diagnose the root cause of an elevated particle count.
Water
Water is an undesirable contaminant in gear oil. Too much can cause the lubricant
to degrade, accelerate corrosion and promote wear. It should always be checked
as part of any oil analysis program.
There are several common methods used for monitoring for water. The oldest and easiest test method is the crackle test, which simply involves dispensing a drop of oil onto a heated hot plate. Other commonly employed methods include FTIR and the Karl Fischer test. Both the crackle test and FTIR are sensitive down to 500 to 1000 ppm and are usually adequate as a screening tool for most gearboxes. More exact quantification of the amount of water present may require the more expensive Karl Fischer test. However, for most gearbox applications, Karl Fischer is best used as an exception test based on a positive crackle or FTIR test.
Lubricant
Condition
Gear lubricants generally have high-quality mineral or synthetic base stocks,
carefully selected for their viscosity properties and fortified with additives
such as antiwear or extreme pressure agents, rust and antioxidant compounds.
In order to ensure quality lubrication, lubricant condition monitoring is an
important aspect of any gear oil test program.
Additives
In addition to revealing machine wear, AES provides information about the lubricant’s
additive package. AW additives typically contain zinc and phospherous. EP additives
are trended by looking at phosphorous alone. If the gear oil contains a detergent
additive, it will typically be revealed by calcium, magnesium and/or barium.
A note about additive trending, AES measures atoms, not molecules. If an additive
molecule is chemically degraded, the elemental levels may remain unchanged.
FTIR, which measures the concentration of various molecules, can provide some
resolution about additive levels. But, its performance is hindered by functional
group interferences, poor repeatability and hyper-sensitivity to accuracy of
the reference oil.
Viscosity
Viscosity is the most important physical property of a lubricant and should
be checked periodically. The lubricant must have suitable flow characteristics
to ensure that an adequate supply reaches lubricated parts at different operating
temperatures, while maintaining a adequate viscosity at operating temperatures
to prevent wear from occurring.
The viscosity of gear oils vary depending on the grade, as well as the degree of oxidation and contamination encountered in-service. If the viscosity of the lubricant differs by more than 10 percent from new oil specification, an oil change is recommended. Measuring viscosity is essential in any test package for gears.
Oxidation
When the oil is oxidized or has become too acidic, the oil must be changed.
There are a number of tests used to monitor oil oxidation; the two most common
are acid number (AN) and FTIR. For gear systems, oxidation is a key parameter,
which needs to be monitored routinely. Because AN can sometimes give ambiguous
results due to the effects of mildly acidic AW and EP additives, it is often
better to use FTIR as a routine screening tool, with AN reserved as the exception
test.
Based on these arguments, a generic test slate for gears is given in Table 1. While this series of tests can be considered a good starting point, test slates, as well as targets and limits should be adjusted based on reliability goals and operational environment. Nevertheless, by selecting an appropriate test slate, oil analysis can be an effective condition-monitoring tool for any gearbox, complementing other technologies such as vibration analysis and thermography.
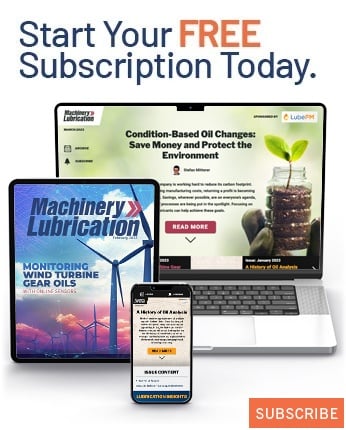