Samarco is a privately owned Brazilian mining company that produces iron-ore pellets. In 2010, the management team decided to drastically change their lubrication practices, as they realized this was an area in need of improvement that could bring great results. Their plan involved several changes, with one of them being a new lube room.
In early 2014, Samarco began making modifications. By the end of the year, the new lube room was completed. However, it is now more than just a lube room. With a training room and a modern onsite laboratory, it was designed to hold the lubrication technicians and all members of the team.
Previously, the lube room was partially open and exposed to a very dirty environment. Access to the room was not controlled. Lubricants were poorly handled, and funnels and buckets were often used. New lubricants were not sampled or filtered before use. There was a lack of receiving procedures, quality control and spill containment. Breathers were not used on drums or containers of new lubricants. One filter cart was utilized to filter all types of lubricants, and it only removed particles and did not have the right filters for the task. New oils that were filtered were stored outside. The onsite laboratory had old equipment and could only perform a few tests. In addition, the lab had no ventilation, and several chemicals were stored inside. Lubricant identification was also poor, as unmarked oil and grease drums were frequently seen.
Samarco's old lube room was partially open, and access to the room was not controlled.
Previously, new oils were stored outside.
Lubricants were poorly handled, and funnels and buckets were often used.
After all the changes were made, the new lube station featured different rooms for the treatment of used oil as well as for receiving and treating new oil. New oil is pumped through hard piping to the treatment room. Now only the filtration technician has access to the treatment room. There is also a new lab, a training room, offices and a storage room for filters, breathers, quick-connects, etc. All storage cabinets for chemical products are also fireproof.
There are four offline absolute filtration stations for used oils and 12 stations for new oils. Each has three minimess valves to draw samples. Oils are delivered to reusable containers by individual reels. An identification system was created with colors and shapes for all oils and greases. The spill containment for each container has the same capacity as the container. If the container leaks, the oil goes to an external container with a 2,000-liter capacity.
Access to the lube room is now controlled.
New oil is pumped through hard piping to the treatment room.
The lubricant receiving room is separate from the treatment rooms.
The new onsite lab has modern equipment and a technician who is able to quickly test new and used oils. There's also a storage area for lubrication-related materials such as breathers, reusable containers, Zerks, etc.
By filtering its new oil, Samarco has been able to extend oil change intervals, as lubricants are delivered to machines with the appropriate cleanliness levels.
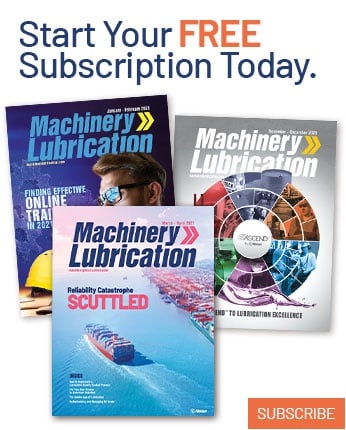