Nowadays most industries have processes that require machines to operate at high temperatures. These applications demand special lubricants that can handle extreme operating temperatures by maintaining their lubrication properties, keeping the system clean and providing a reasonable service life. The ultimate goal is to sustain high machine reliability while controlling maintenance costs. In many cases, a synthetic lubricant may be the best choice.
What is Considered a High Temperature?
Before selecting a high-temperature lubricant, you must first know when a temperature is considered to be high. Unfortunately, there is no single right answer to this question.
For the sake of reference, generally an oil that is able to work at temperatures higher than 210-250 degrees F (100-120 degrees C) for a normal or extended drain interval may be assumed to be a high-temperature lubricant. Of course, other sources may have different opinions on this temperature range.
The well-known Arrhenius rate rule, which relates to lubricant use versus temperature, states that for every increase of 18 degrees F (10 degrees C), the oil life is cut in half.
This equation was originally formulated for mineral oils, but while the lifespan is different for various product technologies, the rule is applicable for both mineral and synthetic lubricants. This means that a mineral oil with a weak formulation may be used at higher temperatures if it is changed frequently, but that is not practical or cost-effective in most cases.
The same principle applies to the base stocks used in greases. The grease’s thickener influences the performance at higher temperatures due to its oxidation resistance, as well as the dropping point that it imparts to the grease. It is recommended to use a grease below its dropping point to ensure the lubricant stays in place. See the sidebar below for a few simple rules to help determine the maximum operating temperature based on a grease’s dropping point.
High-temperature Operation
A lubricant’s operating temperature will depend on several factors, such as the heat produced in and around the machine. Heat may also be generated as a result of normal or abnormal conditions.
Normal or expected conditions would include the machine’s environment (production process and climate conditions), mechanical work realized by the machine, the combustion action in internal combustion machines and the internal fluid friction of the lubricant. Abnormal conditions would consist of an unusual mechanical issue, excessive loads or speeds, lubricant viscosity that is too low or high, and a deficient insulating material.
Reasons for Choosing a High-temperature Lubricant
Before beginning the lubricant selection process, it is important to consider the reason a high-temperature lubricant is desired or required. For instance, it may be a requirement of the original equipment manufacturer (OEM).
This means a particular brand or lubricant type has been tested by the OEM with approved results. In many cases, this is a condition for warranty, so it is advisable to use the recommended lubricant type. Also, always verify the operating conditions to ensure they are consistent with what is expected by the OEM.
Another reason a high-temperature lubricant might be chosen is because of an abnormal machine condition. However, while a better performing lubricant may help mitigate the problem, it is more imperative to correct the root cause of the issue.
New operating conditions or the use of a new technology may also be motivation for favoring high-temperature lubricants, along with simply desiring to enhance performance for improved reliability.
Fluid |
Strengths |
Weaknesses |
Applications |
Polyalphaolefins (PAOs) |
High VI, high thermal oxidative stability, low volatility, good flow properties at low temperatures, nontoxic and compatible with mineral oils |
Limited biodegradability, limited additive solubility, seal shrinkage risk |
Engine oils, gear oils, bearing oils, compressor oils, high-temperature grease, lube-for-life applications |
Diesters and Polyolesters |
Nontoxic, biodegradable, high VI, good low-temperature properties, miscible with mineral oils |
Low viscosities only, bad hydrolytic stability, limited seal and paint compatibility |
Compressor oils, high-temperature grease, co-base stock with PAOs, bearing oils, gear oils, oil mist, jet engine oils |
Phosphate Esters |
Fire-resistant, biodegrades quickly, excellent wear resistance, scuffing protection |
Low VI, limited seal compatibility, not miscible with mineral oils, moderate hydrolytic stability |
Fire-resistant hydraulic fluids used in power plants, factories, marine vessels, mining, aircraft and mobile equipment |
Polyalkylene Glycols (PAGs) |
Excellent lubricity, nontoxic, good thermal and oxidative stability, high VI |
Additives marginally miscible, not miscible with mineral oils, limited seal/paint compatibility |
Refrigeration compressors, brake fluids (water soluble), fire-resistant fluids (water soluble), gas compressors (low gas solubility), worm and high-temperature gears, chain lube (clean burn off), metal-working and quenchants, H1 food-grade lubricants |
Silicones and Perfluoropolyethers (PFPEs) |
Highest VI, high chemical stability, excellent seal compatibility, very good thermal and oxidative stability |
Worst mixed and boundary film lubrication properties, not miscible with mineral oils or additives |
High-temperature fluids, specialty greases, lubricant-contacting chemicals, some brake fluids |
Lubricant Selection
The first step in the lubricant selection process for a high-temperature application is to estimate the average operating temperature or temperature range. At this point, a temperature-control initiative may be implemented, such as installing a heat exchanger, insulant or additional ventilation. Also, be sure the OEM requirements and current machine conditions match the lubricant’s specifications.
The expected performance improvement should be specific, such as to achieve increased varnish or deposit control, extended relubrication intervals or enhanced lubrication properties. Assess the pros and cons of switching lubricants in terms of cost, compatibility, change-out procedures, etc.
To obtain the desired results, you may need to be more specific in terms of the lubricant’s technical properties. The suggested parameters or attributes to consider include the viscosity required by the machine or components at the operating temperature, the film strength properties, the oxidation resistance, the compatibility of the new lubricant with the current lubricant as well as with the synthetic materials in the machine, the potential impact of typical contaminants around the machine, and any OEM or industry standards.
Please note that synthetics are not the only suitable lubricants for high temperatures. Mineral oils with strong refining and additive packages may work as well. Synthetic lubricants must also be changed. Their advantage over mineral oils is that the change intervals are extended. Typically, the higher the operating temperature, the greater the benefit of using a synthetic lubricant.
3 Simple Rules for Maximum Operating Grease Temperature
Your equipment requires lubricating grease to efficiently function. One of the most important qualities of a grease is its dropping point. Simply put, the dropping point is the temperature at which grease becomes a liquid. It’s crucial to understand that dropping point tests the maximum temperature that a grease will hold its form, not the maximum temperature at which it can operate. There are three simple rules for calculating a grease’s maximum operating temperature from its dropping point test results.
- If the dropping point is less than 300 degrees F, subtract 75 degrees F from the dropping point.
- If the dropping point is higher than 300 degrees F but less than 400 degrees F, subtract 100 degrees F from the dropping point.
- If the dropping point is higher than 400 degrees F, subtract 150 degrees F from the dropping point.
The values subtracted may be even larger if extended relubrication intervals are desired. Also, keep in mind that regreasing intervals must be more frequent at higher temperatures due to the Arrhenius rate rule.
Base Stocks Used at High Temperatures
The charts above compare the operating temperature ranges of different base stocks for mineral and synthetic lubricants. Note that these ranges represent normal values according to the base stock type. They do not reflect the comparative life of the lubricant. At high temperatures, the lifespan of synthetics is much longer than similar mineral oil products. There are also more synthetic base stocks that can work at high temperatures, such as diesters, polyglycols, polyolesters, etc.
The table below can be used as a general reference for the maximum service application of greases according to the thickener in the formulation.
The chart at the bottom of the page compares how grease consistency changes with temperature in two greases: simple lithium and lithium complex. The latter is classified as a high-temperature grease even in formulas with mineral oil.
Type |
Dropping Point, °C |
Maximum Service |
Simple Lithium |
175 |
120 to 135 |
Lithium Complex |
250+ |
150 to 175 |
Polyurea |
250+ |
150 to 175 |
Calcium |
90 |
60 to 70 |
Anhydrous Calcium |
140 |
90 to 110 |
Calcium Complex |
260+ |
190 to 220 |
Modified Clay |
280+ |
190 to 220 |
Sodium |
190 |
135 to 150 |
Sodium Complex |
250+ |
170 to 190 |
Strengths and Weaknesses of High-temperature Lubricants
When choosing a high-temperature lubricant, you must be aware of the potential drawbacks in order to select the best possible product. The table above provides the strengths and weaknesses of common synthetic lubricants.
These charts are intended for general reference only, as various technologies in the marketplace may result in different specifications or performance.
Remember, when selecting high-temperature lubricants, follow the appropriate methodology to determine the right option according to your equipment conditions and reliability objectives. Always weigh the pros and cons, and analyze the expected economic and operational benefits so you can be sure you are choosing the correct lubricant for your high-temperature application.
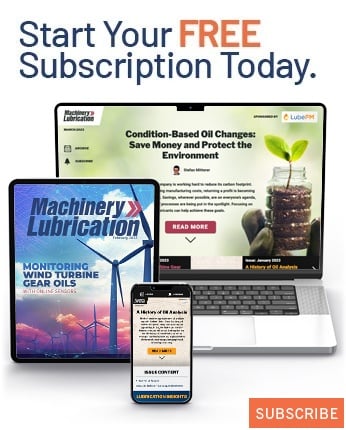