There are many ways to define what constitutes an oil flush. Whether you are discussing oil flushing with contractors, equipment manufacturers or maintenance personnel, it is important to use the same terminology to prevent confusion. This article breaks down oil flushing into four distinct categories and includes when each action is appropriate.
Circulation Filtration
This process can take place when the system is in production and running the system pumps in their normal flow pattern. It typically involves external filtration circulating on the reservoir. Many maintenance personnel call this an oil flush due to achieving a cleanliness level below the normal or manufacturer's operating specifications.
This process is appropriate when performing annual maintenance that is limited in scope and time, i.e., reservoir cleaning, filter/lubricant changing (if same type), etc. Do not use this process if the outage includes pipe breaks or opening of the bearing housings. A third-party laboratory or field kits can be used to verify the particle count and determine completion.
Rinse/Purge
This process is utilized when filling the system with a neutral fluid or new charge of oil. The steps include draining the system, refilling the reservoir to the minimum circulation level and using system pumps circulating in the normal flow path.
Generally, this procedure is employed when making a wholesale lubricant change during a conversion or displacing detergents or cleaners used during varnish mitigation. The cleanliness level is often verified with only the particle count. If performing varnish mitigation, you may also involve a third-party lab or field test kits.
System Flush
A system flush is just as it sounds. This type of flush takes place when utilizing the "system pumps." It requires the installation of bypasses (jumper hoses) around all critical components, such as bearings and control valves, as well as the removal of all orifice plates and blinding of accumulators or any items that could be damaged by flushing. Inspection screens or media are used to verify cleanliness along with particle counts.
This process can be employed for light maintenance work, i.e., changing of a temperature-control valve or for non-critical systems such as redundant boiler feed pumps. Avoid this process if the unit is critical and can become the controlling factor of a deadline during a turnaround. Keep in mind that using system pumps to flush out foreign material will take longer than utilizing an external pump to increase flow.
High-Velocity Oil Flush
Many people believe high velocity occurs once you achieve turbulent flow. Turbulent flow occurs at high Reynolds numbers and is dominated by inertial forces, which tend to produce chaotic eddies, vortices and other flow instabilities. In layman's terms, the oil rapidly changes directions and bounces through the pipe's internals. This assists in breaking off material on the walls and top sides of the pipe's interior.
If the right velocity is not achieved, the oil moves through in a laminar pattern (a straight line), following the path of least resistance and leaving behind material that can damage your system. A Reynolds number of 4,000 is the minimum flow rate that can cause your fluid to become violent or "turbulent" inside the piping. However, in 99 percent of the cases, this is not enough turbulence to pick up and remove particulate.
When performing a high-velocity oil flush, target a minimum of two to three times the normal system flow rate and, if possible, aim for a Reynolds number of 20,000. Multiple Reynolds calculator apps and websites are available. When in doubt, run your numbers through one of these tools to verify the flow rate.
The high-velocity oil flushing process includes bypassing system pumps and utilizing an external unit. Like the system flush, it involves the installation of bypasses (jumper hoses) around all critical components, such as bearings and control valves, as well as the removal of all orifice plates and blinding of accumulators or any items that could be damaged by flushing.
Inspection screens or media are used along with particle counts to verify cleanliness. This process should be used during all major maintenance procedures, system failures or when large amounts of foreign material have been introduced.
About the Author
Larry Jordan has worked with industrial lubricants for 29 years and is a subject-matter expert in high-velocity oil flushing and oil conditioning. Larry is currently a senior services technical adviser at Reliable Industrial Group. For more of Larry's oil flushing tips and advice, contact him via LinkedIn at: https://www.linkedin.com/in/larry-jordan-10b25456/.
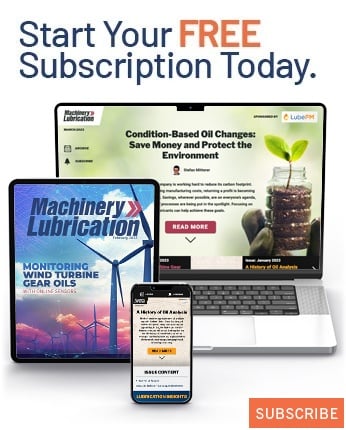