The lubricant is arguably one of the most essential components of a machine, but it also happens to be one of the most vulnerable. Greatly influencing this vulnerability is the temperature, which has an inverse correlation to the most important lubricant property - viscosity. By becoming aware of the potential effects that temperature can have on your lubricants, you can better understand how a machine could fail and hopefully prevent future failures.
Lubricant viscosity has a dependent relationship with temperature.
Startup Temperature
Startup temperature is the ambient temperature upon initial startup of a machine before the lubricant has a chance to reach the operating temperature. During typical operation, the many contributors to heat generation such as friction will cause the temperature to rise and reach an equilibrium with its surroundings, also known as the machine’s operating temperature.
Knowing a machine’s operating temperature is crucial when selecting the appropriate lubricant viscosity, since viscosity has a dependent relationship with the surrounding temperature.
Cold Machine Starts
The term “cold machine starts” refers to low ambient temperatures that can be detrimental to a machine’s operability. The vehicle and mobile equipment industries have long been developing solutions for this challenge of dealing with extreme temperatures, including those in very cold environments.
This has led to the creation of advanced lubricant formulations, such as pour point depressant additives and multi-viscosity oils, as well as advanced engine designs with the integration of block and pan heaters.
Lubricant Failure
To comprehend the potential machine failure modes associated with a cold start, it is essential to review the ways in which a lubricant can fail from these conditions, both physically and chemically.
Not only does the lubricant become more viscous at cold temperatures because of the temperature-viscosity relationship, but it can eventually congeal when it passes below a certain temperature point called the pour point. Under test methods defined by ASTM D97, the pour point describes the cold temperature point in which the oil begins to become immobile and will no longer flow.
For example, gear oil at a cold enough temperature can be placed on the floor and stood upon like a block of ice. However, unlike water, which maintains a constant viscosity until it solidifies at an exact temperature, oil will gradually become thicker and congeal at varying rates. This makes it challenging to set lubricant selection standards for the equipment operation.
Therefore, even though the oil has not yet reached the pour point, the viscous nature of the cold oil can cause substantial flow restriction in machine components like hydraulic or circulating oil pumps. The consequences of a pump flow restriction can be catastrophic, with effects such as surface wear from vaporous cavitation and bearing wear from starvation.
Some additives are affected by the low temperature conditions of machine startup. For instance, certain extreme-pressure additives are only activated at elevated temperatures as a result of surface friction from high speeds or high loads. If the machine is operating at slower speeds during startup and in a cold environment, the additive can become significantly less effective.
Other additives like rust inhibitors can have poor solubility and stratify to the bottom of sumps and storage containers during prolonged stagnant periods in cold temperatures. If the oil continues to operate at cold temperatures, the foam tendency can increase, especially with low viscosity oils. All these degradative effects on lubricant additives will result in limited protection of the machine components from corrosion, premature wear and foam.
Filter Resistance and Failure
All machines behave differently to high viscosity in cold-start conditions, depending on the design of the machine and the component sensitivities. For example, in any system where fluid is circulated, such as a forced circulating lube oil system or a wet sump circulating system, the oil should flow through a filter.
The filter elements will naturally cause flow restriction. Higher flow restriction results in a higher pressure drop, leading to the filter bypass valve opening (if equipped), the filter element rupturing or both. Because the viscosity increases during a cold start, the pressure drop also increases due to increased resistance through the filter element.
Unfortunately, the potential for failure is not isolated to the filter in these conditions. Not only can the filter rupture, but it can also trigger a chain reaction with other secondary failures on the machine.
When the oil starts to channel in between cracks as the filter ruptures, the buildup of contaminants on the filter has a chance to push through all at once. The mass ingression of particles will then directly promote wear on the machine.
Generally, the leading cause of failure from cold-start conditions is from increased flow resistance. Even if the filter doesn’t rupture, the viscous oil will result in damage. The table below illustrates how viscosity can change as a result of a temperature change. A 220 ISO VG oil with a viscosity index of approximately 100 will increase to more than 5,000 centistokes when the temperature drops to 0 degrees C (32 degrees F).
Lubricant Starvation
Most mechanical methods that help supply oil to lubricated components will become hindered when temperatures drop. As mentioned previously, if the oil is designed to flow through piping, such as a lube oil circulating system, the oil can become greatly restricted and starve the machine.
Other oil-lifting devices can also lose their effectiveness under such conditions. Ring oilers start to drag, causing unwanted friction, while oil slingers hold onto the viscous oil, resulting in an insufficient distribution of lubricant to higher lubrication zones.
Grease Applications
Grease has similar risks in cold environments since the oil within the grease still abides by the temperature-viscosity relationship. The potential for lubricant starvation from a lack of grease application is a common issue.
With any application method designed to push grease through an orifice or grease line, such as a centralized grease system, single-point lubricator or even manual greasing, grease movement may be significantly restricted in cold temperatures.
Consequently, the grease may not be properly applied in the component’s friction zones. Certain greases intended for cold temperatures are formulated to handle these conditions. Test methods such as ASTM D4793 and D1478 have been developed to determine how grease restricts motion in a bearing under cold temperatures.
Gearbox Systems
Most types of gearboxes are at risk of starvation, including splash-lubricated, wet sump circulating systems or forced lube oil circulating systems. When the oil is too viscous during startup, it cannot reach the gear meshing zones due to a lack of injector pressure or channeling of the oil in splash-lubricated systems.
As a result, the unlubricated high-pressure contact pivot points on the gear teeth can become damaged. In addition, any gear system that must overcome the churning effects applied by the viscous oil will experience limited power transmission as well.
Engines
Nowadays, it is common for machines in cold environments to be equipped with heating elements to allow the machine to start. However, as temperatures continue to drop, simply using block heaters does not eliminate the risk to engine components which have not yet mitigated localized oil that remains below the pour point.
For instance, even though the machine may be freely turning over at startup, if the oil sump is still in a gelled state, the lubricant cannot perform its role properly. This can lead to engine seizure. Air pockets can form in the gelled oil, called air binding, and starve the pump of oil.
To prevent this, pan heaters and higher quality lubricants are often used to help keep the viscosity down. When conditions are uncertain, you can observe the oil flow from the tip of the dipstick for assurance of the oil’s viscous state.
Oil kinematic viscosity combined with temperature in centistokes (cSt)
Journal Bearings
The oil wedge formed during rotation of a journal in the bearing housing is a careful balance of speed, viscosity and load. In any circumstance when the viscosity is undesirably high, such as when temperatures are very low, the oil can begin to whip around the journal, causing the shaft to wobble. Excessive wear can then occur from the reduced working clearances.
Hydraulics
For hydraulic systems, the biggest risks in cold temperatures are cavitation and filter element failures in hydraulic pumps, as mentioned previously. Another problem that can arise involves hydraulic seals. While contamination and installation issues are the most common reasons why seals leak and fail, cold starts and cold operating temperatures also pose a threat of seal embrittlement.
Bearings
Bearings with rolling elements will have reduced mobility when oil or grease becomes too viscous in cold temperatures. Viscous oil leads to churning losses and skidding of the rollers. Skidding will damage the rolling elements and cage structure. Friction increases as these components are damaged and can result in a failure.
In grease applications, the oil in the grease becomes considerably challenged at low temperatures. The base oil separation rate will be insufficient at low temperatures because the viscous oil will stay trapped in the thickener held outside the raceway. During these conditions, lubricant starvation can cause early bearing failure.
Beware of Vaporous Cavitation
Vaporous cavitation is particularly concerning, as it is symptomatic of high pressure differentials in the pump, such as during high viscosity cold starts. As oil is drawn in on the suction side of a hydraulic pump, dissolved air is desorbed from the oil coalescing with vaporous bubbles, which then continue to expand.
These larger vaporous bubbles respond destructively when compression occurs during the pump’s transition from the suction side to the high-pressure side. This sudden and drastic increase in pressure forces these bubbles to collapse, leading to damage of the nearby oil and machine surfaces from the adiabatic effect.
Avoiding Machine Failure During Cold Starts
Thankfully, over the last few decades, lubricant manufacturers have become aware of the effects that cold temperatures can have on machines. This has led them to develop formulations that can handle these conditions, including during machine starts.
The base oil plays a major role, as many highly refined mineral oils and synthetics are less affected by temperature swings. This is represented by the viscosity index. Viscosity index improvers can enhance this property. The higher the viscosity index, the less change in viscosity per a change in temperature.
Pour point depressants can also improve the characteristics of oil in cold temperatures. These base oil and additive properties, along with a correctly selected viscosity grade or multi-viscosity grade, offer viable solutions in cold temperatures.
Nevertheless, at times lubricant formulations may not be enough to avoid the pitfalls of cold starts. In these cases, machines can be equipped to overcome the frigid elements through the installation of block and pan heaters, as mentioned previously, as well as pre-lube systems that prepare the machine’s components for a cold start.
The consequential failure that can arise from not properly preparing for cold-start conditions will be gradual and indirect. Not only can cold temperatures be the root cause of unfavorable lubricant conditions, but their presence can also trigger a chain reaction, leading to highly viscous lubricants, which introduce the opportunity for lubricant starvation, increased contamination, premature wear generation, inactive additives and other impending effects.
Once machine operators and reliability engineers are aware of the risks that cold temperatures present, particularly at startup, adjustments can be made to prevent these chain reactions from occurring.
References
Applied Hydraulics Magazine. (1956, February). 67-70.
Bbehrouz, A. (2014, September). “Dead Sensor.” Mechanical Engineering Magazine.
Cash. W. (2016, April). “Best Ways to Combat Oil Gelation.” Machinery Lubrication.
Diemand. D. (1990, December). “Lubricants at Low Temperatures.” Cold Regions Technical Digest.
Fitch, E.C. (2002, July). “Temperature Stability of Lubricants and Hydraulic Fluids.” Machinery Lubrication.
Fitch, J.C. (2012, August). “The Hidden Dangers of Lubricant Starvation.” Machinery Lubrication.
Hochmann. M. (2013, March). “Gear Lubrication – Gear Protection Also at Low Oil Temperature.” Gear Solutions.
Khonsari, M. & Booser, E.R. (2007, March). “Low Temperature and Viscosity Limits.” Machinery Lubrication.
Manney, D. “Extend the life of your gearbox with predictive maintenance.” Retrieved from www.lselectric.com/extend-the-life-of-your-gearbox-with-predictive-maintenance.
“OWI-Lab invests in -40°C cold start-up test bench for wind turbine drivetrain components.” Retrieved from www.owi-lab.be/content/owi-lab-invests-40%C2%B0c-cold-start-test-bench-wind-turbine-drivetrain-components.
Wikström, V. (2000, November). “Lubrication of Bearings at Low Temperatures.” Retrieved from http://evolution.skf.com/us/low-temperatures.
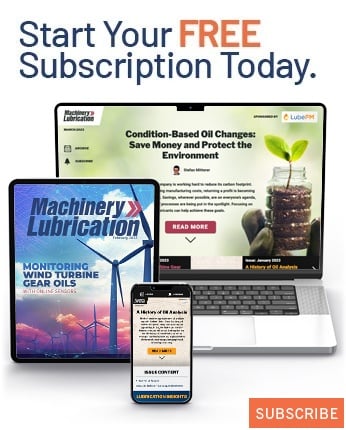