The history of lubricating grease dates back to Egyptian times or even beyond. Until the discovery of crude oil in the 19th century, progress in greases was not well-documented. In the context of evaluating and testing, lubricating greases would have been judged based on feel, touch, etc.
In the last couple of centuries and especially in the last century, phenomenal progress has been made in grease development with many different types of greases, such as lithium/lithium complex, aluminum complex, calcium sulfonate, barium complex, polyurea, etc. Surprisingly, lubricating greases are still judged by their appearance, feel and odor, even though these have little impact on service or quality.
On the other hand, the properties that do influence an actual application, such as consistency/mechanical stability, load-carrying capacity, water resistance, oxidation stability and high-temperature life, etc., are often overlooked.
The Effect of Color on Lubricating Grease
One can find a variety of colored greases on the market, including white, black, blue, red, green, purple, translucent, yellow/golden, etc. There are various opinions and perceptions about the colors of greases.
To be more specific on colors, white greases are indicative of greases for food machinery, while black greases are moly/graphite greases for severe operating conditions. Although there is no hard and fast rule, red could be indicative of grease for high temperatures, blue for cold temperatures and green for environment friendliness. Below are some interesting results regarding the effects of color on grease properties.
Grease Whiteners
To make grease white, the most commonly used whiteners are titanium dioxide (TiO2) and zinc oxide (ZnO), which are generally used as solid powders. The amount of these compounds in lubricating greases may vary from 0.5-10 percent or even more depending upon the extent and other ingredients used to make base greases.
In a recent study, different percentages of TiO2 and/or ZnO in lithium, lithium complex, aluminum complex and calcium sulfonate greases were used and then examined for the effects of these whiteners on the dropping point, penetration, mechanical stability, anti-wear, storage hardening and oil separation.
The results have been complied in Table 1. This table reveals that the addition of titanium dioxide and zinc oxide did not have any significant effect on the dropping point.
However, in 5 percent concentrations, softening in penetration was indicated. In terms of mechanical stability, tested as penetration after 10,000 double strokes, the change in the worked penetration (60 double strokes) to penetration after 10,000 strokes was more when these whiteners were added in more than 2 percent concentrations, especially in lithium, lithium complex and aluminum complex greases, while no significant impact was noted with calcium sulfonate greases.
As for wear measured by the wear scar diameter (WSD), the incorporation of TiO2 and ZnO slightly increased the wear scar diameter. There was also an increase in oil separation in lithium and lithium complex greases.
Sunlight, Heat and Water
It is important to consider the environment to which grease is normally subjected, including exposure to sunlight, heat and water due to application requirements or when containers are not stored in ideal conditions. When grease is exposed to light, its color starts to fade and does not carry the same visual appeal as it did at the time of manufacturing/packaging.
Similarly, when grease is exposed to heat/high temperatures, it becomes dark or changes to a dull/light shade. Additionally, in actual application, the color of grease tends to darken over time. The presence of water also negatively affects the color of grease.
For example, when red grease was floated on water for 24 hours, it not only emulsified but also changed its color from red to orange. Therefore, from an application point of view, a grease’s color adds little value to its overall performance.
Liquid Dyes
Dyes are used in greases in extremely small proportions and should not be of much concern. Still, certain classes of dyes can pose environmental and health issues. The concentration of dye used may vary from 0.001 to 0.5 percent or more, depending on the intensity of color needed.
In order to study the effects of dyes on grease properties, various amounts of dye were added to grease and tested for penetration, dropping point and copper corrosion. According to these studies, the color of dye does not affect penetration or the dropping point, but it does adversely affect copper corrosion at higher concentrations of 0.1 percent or greater. This indicates that if you use dye in higher concentrations, it might impact the grease’s corrosion resistance properties.
Effects of Polymers/Tackifiers
Polymers are incorporated into grease to improve the consistency, shear stability, water resistance, adhesion and tack properties. On the other hand, polymers may negatively affect the cold temperature and flow properties of greases.
The effects of polymers on grease thickeners have been studied and are shown in Table 2. In lithium-12 hydroxy stearate grease (lithium-12), all the polymers slightly improved the dropping point and penetration, but there was no significant impact on mechanical stability.
In calcium sulfonate grease, both polymers improved penetration and exhibited good mechanical stability and roll stability in the presence of water. However, higher concentrations of polymers yielded inferior results in water spray-off properties.
The pumpability of various grease samples was also tested per the U.S. mobility test. The results indicated no significant effect on pumpability at 77 degrees F with or without polymers.
At lower temperatures (0 degrees F and minus 20 degrees F), the pumpability capability with polymers was significantly reduced and found to be dependent on the amount of polymer added. Similar results were found with lithium complex greases. The results in Table 3 indicate that pumpability is drastically reduced at lower temperatures when the grease contains polymers.
Conclusions
There have been different types of standard and sophisticated methods developed to test the quality of lubricating greases. Unfortunately, practices such as smell and touch to test tack and color are still prevalent in industry.
Studies have shown that color does not add value to any lubricating grease property but that excess amounts of dye may deteriorate some properties like copper corrosion. The addition of TiO2 and ZnO, which impart white color to greases, also do not add value to any grease properties but may increase wear and oil bleeding when used in higher concentrations.
While tack does improve certain grease properties like water resistance, yield and oil bleeding, excess amounts may be counterproductive. It has been observed that certain amounts of polymers do increase the hardening tendency of aluminum complex grease, especially if it is made with vegetable oil. Similarly, lubricating greases with polymers have indicated comparatively inferior pumpability/mobility especially at lower temperatures.
Table 1. Effects of Whiteners on Lubricating Greases
Property |
ASTM |
Lithium-12 |
Lithium Complex |
Aluminum Complex |
Calcium Sulfonate |
Without Any Whitener |
|||||
Drop Point, °F |
D 2265 |
385 |
515 |
525 |
+ 550 |
Worked Penetration |
D 217 |
280 |
286 |
298 |
292 |
10 K Strokes Penetration |
302 |
310 |
326 |
296 |
|
Wear Scar Dia., mm |
D 2266 |
0.60 |
0.55 |
0.60 |
0.45 |
Oil Separation, % |
D 6184 |
0.5 |
0.3 |
1.2 |
0.3 |
2% Whiteners (1% TiO2 + 1 % ZnO) |
|||||
Drop Point |
D 2265 |
379 |
513 |
525 |
+ 550 |
Worked Penetration |
D 217 |
283 |
284 |
305 |
290 |
10 K Strokes Penetration |
308 |
314 |
338 |
299 |
|
Wear Scar Dia., mm |
D 2266 |
0.65 |
0.55 |
0.65 |
0.50 |
Oil Separation |
D 6184 |
0.7 |
0.6 |
1.3 |
0.3 |
5% Whiteners (3% TiO2 + 2% ZnO) |
|||||
Drop Point |
D 2265 |
365 |
518 |
531 |
+ 550 |
Worked Penetration |
D 217 |
296 |
288 |
302 |
290 |
10 K Strokes Penetration |
333 |
326 |
345 |
301 |
|
Wear Scar Dia., mm |
D 2266 |
0.65 |
0.65 |
0.70 |
0.55 |
Oil Separation |
D 6184 |
1.1 |
0.8 |
1.9 |
0.5 |
Table 2. Effects of Polymers on Lithium-12 Hydroxy, Lithium Complex and Calcium Sulfonate Complex Greases
#. |
Polymer Type |
% |
DP, °F* |
Pen** |
10 K |
Penetration after 6 months |
Roll St w/10% |
WSO*** |
Lithium-12 Hydroxy Stearate Grease |
||||||||
i. |
PIB |
0 |
386 |
276 |
299 |
279 |
14.5 |
85 |
ii. |
PIB |
5.0 |
384 |
278 |
304 |
276 |
13.6 |
76 |
iii. |
PIB |
10.0 |
392 |
287 |
311 |
272 |
12.6 |
54 |
i. |
Eth-Prop |
1.0 |
395 |
279 |
302 |
310 |
8.5 |
65 |
ii. |
Eth-Prop |
2.5 |
394 |
297 |
300 |
315 |
9.2 |
81 |
i. |
Latex |
1.0 |
384 |
285 |
311 |
316 |
14.5 |
65 |
ii. |
Latex |
2.0 |
394 |
278 |
308 |
319 |
16.5 |
85 |
Lithium Complex Grease |
||||||||
i. |
Eth-Prop |
0.0 |
502 |
285 |
311 |
284 |
11.5 |
78 |
ii. |
Eth-Prop |
1.0 |
505 |
280 |
306 |
315 |
8.5 |
56 |
iii. |
Eth-Prop |
2.0 |
515 |
274 |
304 |
326 |
8.2 |
72 |
i. |
Latex |
1.0 |
508 |
281 |
315 |
316 |
10.2 |
52 |
ii. |
Latex |
2.0 |
513 |
276 |
311 |
324 |
8.2 |
83 |
Calcium Sulfonate Grease |
||||||||
i. |
Eth-Prop |
0.0 |
+550 |
302 |
305 |
298 |
295 |
56 |
ii. |
Eth-Prop |
1.0 |
+550 |
288 |
291 |
287 |
283 |
34 |
iii. |
Eth-Prop |
2.0 |
+550 |
276 |
285 |
288 |
303 |
67 |
I. |
PMA |
0.3 |
+550 |
285 |
289 |
282 |
279 |
27 |
II. |
PMA |
0.5 |
+550 |
277 |
288 |
272 |
295 |
21 |
IV. |
PMA |
1.0 |
+550 |
308 |
320 |
298 |
325 |
72 |
*DP – Drop point tested as per ASTM D2265 |
Table 3. Effects of Polymers on the Pumpability of Lubricating Greases
Grease Type |
U.S. Steel Mobility Test, gm/min |
|||||
|
Polymer type |
% |
77°F |
0°F |
-20°F |
-40°F |
Lithium-12 Hydroxy Grease |
Ethylene- Propylene |
0.0 |
662 |
15.8 |
3.9 |
- |
0.75 |
649 |
10.8 |
2.7 |
- |
||
1.5 |
648 |
8.3 |
1.9 |
- |
||
Synthetic Calcium Sulfonate Grease |
OCP + PIB |
0.0 |
968 |
60.7 |
23.0 |
6.3 |
1.0 |
- |
11.0 |
5.0 |
1.2 |
||
2.0 |
- |
4.3 |
1.2 |
0.4 |
||
Lithium Complex Grease |
Ethylene- Propylene + Polymeric Latex |
0.0 |
660 |
22.0 |
4.4 |
- |
1.0 |
442 |
10.0 |
2.1 |
- |
||
2.0 |
250 |
6.5 |
1.2 |
- |
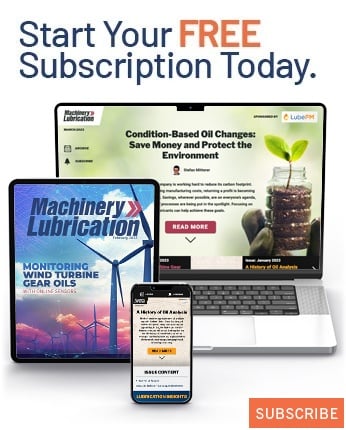