Polished machine surfaces can improve equipment performance by reducing friction and increasing efficiency. There are many ways to polish machine surfaces, with the results depending on the desired outcome. When it comes to lubricants, additives can be used to help chemically polish these surfaces during the running-in process. However, problems can arise if you do not understand the proper way to polish surfaces or how lubricant selection factors into the equation.
What Is Polishing Wear?
ASM International defines polishing wear as the interactions between two solids that remove material from and produce a polished finish on one or both of them. If you think of a polished surface, you might imagine something that reflects light or appears very bright.
When I was a child, I remember seeing cans of silver polish used on serving trays and utensils to restore their original luster. These polishing compounds usually fall into two categories: chemical compounds and abrasive compounds. Each has a purpose and reason for use.
46% | of lubrication professionals say abrasive wear is the most common wear mode in machinery at their plant, according to a recent survey at MachineryLubrication.com |
Abrasive Polishing
Abrasive compounds are often pastes with a solid particle blended into them. After the compound is applied to a surface, it is rubbed with a cloth or against another solid surface. During this action, the abrasives cut and score the surfaces, resulting in a polished face.
This is a common practice with engine valves, as polishing can improve performance and prevent carbon buildup. Another term for this type of polishing is mechanical polishing, since it requires mechanical force to move the parts together. Sometimes these abrasive compounds are called grinding or lapping compounds.
This form of abrasive wear occurs inside machines when small particles are suspended in the lubricant and become trapped between moving components. These particles in the oil can act like a polishing compound and begin polishing the parts in which they come into contact. You can see this kind of polishing wear in most systems, although it is particularly prevalent in gears and hydraulics.
Chemical Polishing
Chemical polishing happens when a chemical is corrosive enough to remove the surface layer of metal, exposing the underlying metal, which typically is reflective and very polished. This type of polishing is most like the silver polish mentioned earlier.
In this mechanism, a mildly corrosive compound is applied to a surface. The compound then reacts with the surface material, forming a soft film on the metal. When the polish is removed, it takes this soft film with it, leaving behind an unoxidized and often brightly polished surface.
The Pros of Polishing Wear
Polishing wear can be used to your advantage. When machine parts are highly polished, there tends to be less drag or friction between the parts. This will help with the equipment’s efficiency by reducing amp draw, fuel consumption and possibly even the operating temperatures.
Machine surfaces are often rough with microscopic projections known as asperities. These asperities greatly contribute to the friction between moving parts. The larger the asperities, the more friction will be generated, which must be overcome during operation.
A good example of this would be rubbing two pieces of sandpaper against each other. Each piece of grit on the paper represents an asperity. If rubbed together, the individual pieces of grit come in contact and require more force to pass over each other. When machine parts are finely polished, it is like reducing or removing the grit from the paper. Less or smaller grit means less force and less surface damage when these parts move relative to one another.
In terms of lubrication, more polished machine surfaces require a smaller lubricating film for protection. The goal of a well-oiled machine is to have a lubricating film that is larger than the surface asperities. When the surfaces are very rough, the film must be larger. This is typically achieved by using higher viscosity lubricants.
The higher the viscosity, the more viscous drag in the machine and the more fuel or energy that must be consumed to churn through the lubricant. If the machine parts are finely polished and have smaller asperities, the lubricant film can be smaller, and subsequently a lower viscosity lubricant can be used. This means less viscous drag and better energy efficiency.
The Cons of Polishing Wear
Although polishing can be beneficial in many ways, it can also be a negative process if it occurs unintentionally. Unintended polishing may take place when a concentration of solid contaminants reaches a certain point in both the size and number of hard particles.
While the machine is operating, this mixture of oil and particles moves throughout the system. These particles begin cutting into the machine surfaces, leaving behind small, linear scrapes that ultimately lead to a polished surface.
Another example of how polishing can happen unintentionally is when the wrong additive package is selected for a piece of equipment. Many gear oils rely on the addition of extreme-pressure (EP) additives to aid in lubricating moving parts in boundary lubrication regimes. Some of these EP additives are chemically aggressive and actually eat or pit into machine parts, causing chemical polishing.
When the additive package is matched appropriately with the machine, this chemical reaction will be mild, and the soft metal film formed by the polishing process can be beneficial in reducing machine wear during boundary lubrication conditions.
When the additive package is not matched correctly, the resulting chemical wear becomes far too extreme, removing more surface metal and ultimately reducing the machine’s surface profile. As the surface profile is reshaped, the parts do not mate together as well and in some cases can lead to catastrophic failure.
Machines most susceptible to aggressive chemical polishing are those that employ the use of a soft metal or a softer metal alloy. A good example would be a worm-drive gearbox. Frequently, the worm is made of steel, while the worm wheel is made of brass or some copper alloy.
Chemically aggressive EP additives will attack the soft copper. This polishing process typically will go beyond the mild surface polish and turn into severe chemical corrosion, leading to the eventual failure of the machine.
Prevention
To ensure the oil you use will not cause severe chemical polishing, check the lubricant’s technical data sheet for the results of the ASTM D130 test, which is known as the copper strip corrosion test. How the lubricant performs on this test will tell you how corrosive the fluid and additives are to softer metals.
The test takes a strip of freshly polished copper and subjects it to the candidate fluid. After it is heated, the strip is examined for corrosion. The results are reported on a scale ranging from 1A (virtually no corrosion) to 4C (severe corrosion). If you have soft metal alloys in your equipment (worm gears, some hydraulic valve spools, etc.), select a lubricant with a 1A rating. If the machine doesn’t have softer metals, you can choose a more aggressive lubricant and still have less risk of extreme chemical polishing.
It is possible to catch polishing wear before it becomes a problem. Perhaps one of the easiest ways to determine if polishing is taking place is to perform a visual inspection of the machine parts. These inspections can be done with a borescope. Check the mating surfaces for light reflection, which is typically the telltale sign of polishing wear.
In the event you can’t visually inspect the machine surfaces, study your oil analysis reports. Examine the wear debris and determine whether the trends are linear, supporting a normal wear pattern, or if the machine is beginning to produce more debris than in the past. Although it may be difficult to conclude from the reports whether the wear mechanism is polishing wear, this will give you some indication of a potential problem before it creates the need for equipment replacement or a rebuild.
Fortunately, this wear mode can be prevented by ensuring that your lubricant is clean. Filtering the oil will reduce the number of particles that lead to polishing and mitigate or delay polishing wear from occurring. To impede chemical polishing, choose the proper lubricant and additive package. If you don’t know which lubricant to select, contact the equipment manufacturer, a lube supplier or a consultant to assist you in this process.
Using the wrong lubricant can have disastrous results, while the correct one can provide years of uninterrupted service life. Finally, keep in mind that although polishing wear can have both good and bad consequences, it usually is best to avoid any wear mode, as this will help your equipment last longer and ensure less downtime.
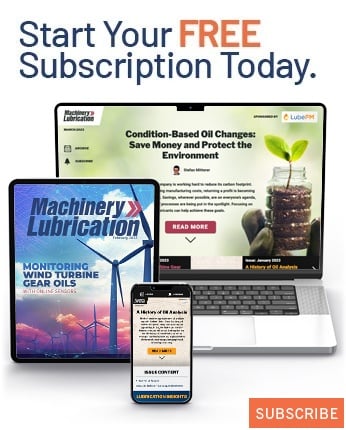