“What are the best practices for storing and handling oil drums?”
Oil drums should be stored indoors away from potential contamination. This would include dust, humidity from process steam and washdown areas. Do not keep oil drums on the factory floor or in the machine shop, since contaminants like metalworking or welding particles and production dust could easily find their way into the drums.
Temperature variations in the storage areas will cause the oil drums to “breathe.” During the heat of the day, the air and liquid will expand, while at night when things cool down, they will contract. This contraction will pull microscopic particles of dust and moisture into the drum. Either of these types of contamination can severely diminish your lubricant’s performance and in turn will affect the life of your machinery.
Drum bungs should be kept sealed and tight at all times. The use of high-quality desiccant or particle breathers will help keep out moisture and dirt. The desiccant gel wicks moisture from the air as the drum “breathes.” Most of these types of breathers also have a particle breather, which makes them even more effective. However, if there is little to no moisture in the air, a good particle breather may be all that is required.
If your oil drums cannot be stored as described above, be sure to at least use drum covers or store the drums horizontally with the bungs at the 3 and 9 o'clock positions. This will help to prevent contaminants from entering the drums if they are more than half full, as the oil will cover the bungs.
Ideally, drums should be stored on proper storage racks using the first-in/first-out (FIFO) method to maintain a good stock rotation. This is very important because any lubricant that has been sitting in the back of the storage area for five years has a good chance of having stratified additives, meaning the additives have fallen out of suspension within the oil.
As with all lubricant storage, oil drums should be stored in a clean, cool and dry environment. Also, try to maintain a consistent temperature. Best practice would be to have an air-conditioned room at a constant 70 degrees F, since extreme temperatures can affect the life and effectiveness of your lubricants. If you will follow these storage and handling practices, you will be well on your way to lubrication excellence.
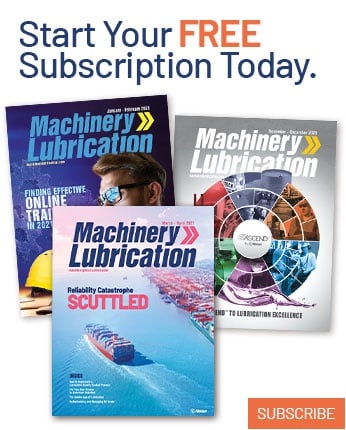